CNC Machined Parts: Comprehensive Guide to Precision Mechanical Components
By:Admin
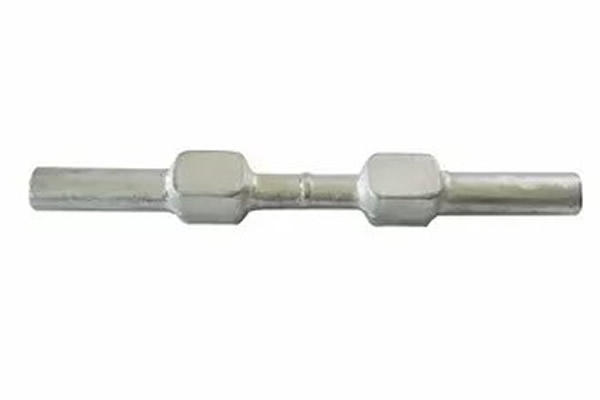
Leading Manufacturer of Precise CNC Machined Parts, Offering Unrivaled Quality and Exceptional Service
[Introduction]
{Company Name}, a well-established leader in the manufacturing industry, has proudly become one of the world’s foremost providers of precise CNC machined parts. With a relentless focus on quality, innovation, and customer satisfaction, {Company Name} has been revolutionizing the way industries operate with their cutting-edge technology and unmatched expertise.
[Body]
1. Exceptional Quality:
- {Company Name} is renowned for its commitment to delivering CNC machined parts of exceptional quality. The company employs state-of-the-art machines and a team of highly skilled technicians to ensure that each component meets rigorous industry standards.
- By utilizing advanced computer-aided design (CAD) software, meticulous attention to detail, and a strict quality control process, {Company Name} guarantees the precision and accuracy of every machined part they produce.
- Whether it's intricate medical components, aerospace parts, or complex machinery elements, {Company Name} consistently asserts their dedication to delivering excellence in craftsmanship.
2. Cutting-Edge Technology:
- As a pioneer in the industry, {Company Name} continually invests in the latest CNC machining technology. This allows them to stay ahead of the competition and provide their customers with the most advanced solutions available.
- The company's state-of-the-art manufacturing facilities house a wide range of CNC machines, including multi-axis mills and lathes, which are capable of producing complex geometries with precision and efficiency.
- In addition, {Company Name} actively explores emerging technologies, such as 3D printing and automation, to further enhance their capabilities and offer innovative solutions to their clients.
3. Diverse Applications:
- {Company Name} caters to a diverse range of industries, including aerospace, automotive, medical, electronics, and more. Their broad expertise ensures that they can meet the unique requirements of each sector.
- Whether it's producing critical components for aircraft engines, surgical instruments for the medical field, or machine parts for industrial equipment, {Company Name} has successfully demonstrated its ability to deliver customized CNC machined parts for any application.
- By closely collaborating with their clients, {Company Name} strives to fully understand their specific needs and develop tailored solutions that align with their objectives.
4. Commitment to Customer Satisfaction:
- {Company Name} places immense value on its customer relationships. They understand that providing excellent service, prompt delivery, and exceptional support are key to maintaining long-term partnerships.
- Their customer-centric approach ensures that clients are involved and informed throughout the entire manufacturing process. Whether it's consulting, design optimization, or post-production assistance, {Company Name}'s dedicated team is readily available to assist customers at every step.
- Through clear communication, unparalleled expertise, and a focus on building mutually beneficial relationships, {Company Name} aims to exceed customer expectations and establish itself as a trusted partner in their success.
5. Continuous Improvement and Sustainability:
- Recognizing the importance of sustainability, {Company Name} strives to minimize its environmental impact. They adhere to strict recycling practices, reduce energy consumption, and implement eco-friendly manufacturing techniques.
- Additionally, the company places a strong emphasis on continuous improvement, investing in employee training and fostering a culture of innovation. By staying at the forefront of technological advancements and constantly challenging themselves, {Company Name} ensures that they remain at the forefront of the industry.
[Conclusion]
With its unwavering commitment to provide exceptional quality, cutting-edge technology, and unmatched customer service, {Company Name} has established itself as a leading manufacturer of CNC machined parts. By consistently pushing boundaries and delivering innovative solutions, the company sets new standards for precision engineering and leaves an indelible mark on various industries worldwide.
Company News & Blog
Quality Hand Forged Iron Coat Hooks: A Must-Have for Every Home!
Hand Forged Iron Coat Hooks: The Perfect Combination of Style and FunctionCoat hooks serve an essential purpose in our everyday lives, offering a convenient solution for organizing our outerwear. While functionality is undoubtedly important, it does not mean compromising on style. Hand Forged Iron Coat Hooks, an innovative product (brand name needed), is taking the market by storm with its unique blend of functionality and aesthetics.Hand Forged Iron Coat Hooks are meticulously crafted using traditional blacksmithing techniques. The company behind this exquisite creation, which is committed to bringing art into everyday life, has been a prominent figure in the industry for years.The manufacturing process begins with skilled craftsmen who heat iron rods in a forge until they are malleable enough to be shaped into the desired form. These craftsmen skillfully transform these rods into beautifully designed hooks by carefully hammering, twisting, and welding each piece with the utmost care and precision.The result is an astonishing range of hand forged iron coat hooks that are not only practical but also a true work of art. Each hook is unique, showcasing the individuality and creativity of the craftsmen. The attention to detail is evident in every curve and twist, creating a visually appealing element for any living space.But Hand Forged Iron Coat Hooks, however visually stunning, are not just for decorative purposes. Coming in a variety of sizes and styles, they offer a practical storage solution for your coats, hats, scarves, and other items that need to be easily accessible. The sturdy iron construction ensures they can withstand the weight of heavy winter coats, while still maintaining their timeless aesthetic appeal.Additionally, Hand Forged Iron Coat Hooks also offer versatility in their installation options. Whether you prefer a traditional wall-mounted design or wish to create a unique display using a stylish coat rack, these hooks can be easily adapted to suit your individual needs and design preferences.Moreover, these hooks are not limited to home use alone. The durability and unique design make them a perfect addition to commercial spaces such as hotels, restaurants, and boutiques. They add a touch of elegance and sophistication while providing customers with a functional and convenient storage option.When compared to mass-produced hooks, Hand Forged Iron Coat Hooks stand out for their superior quality and craftsmanship. Each hook is carefully inspected to ensure it meets the company's high standards before reaching the customers' hands. The attention to detail and commitment to excellence set these hooks apart from their competitors.In addition to their exceptional products, the company follows environmentally friendly practices throughout their manufacturing process. By utilizing traditional blacksmithing techniques, they minimize the negative impact on the environment commonly associated with mass production.Hand Forged Iron Coat Hooks have quickly gained popularity among interior designers and homeowners alike. Their ability to effortlessly blend into various interior styles, whether it be rustic, traditional, or contemporary, has made them an essential element in creating visually appealing and functional spaces.In conclusion, Hand Forged Iron Coat Hooks have emerged as a leading choice for those seeking a perfect combination of functionality and style. With their unmatched craftsmanship, attention to detail, and commitment to quality, these hooks are sure to be a valuable addition to any living or commercial space. By choosing Hand Forged Iron Coat Hooks, you not only invest in a practical storage solution but also add a touch of timeless elegance and beauty to your everyday surroundings.
Advanced Rubber Rail Pad: Boosting Safety and Performance on Rail Tracks
Rubber Rail Pad: Enhancing Safety and Efficiency in the Railway IndustryRailways are the backbone of transportation systems across the world, connecting businesses, communities, and individuals. Ensuring the safety and efficiency of railway operations is of paramount importance, and one crucial component that plays a significant role in achieving this goal is the rubber rail pad.[Company Introduction]The Importance of Rubber Rail PadsRubber rail pads act as a crucial interface between the railway tracks and the underlying sleepers, offering numerous benefits to the railway industry. These pads help absorb vibrations and control noise levels generated by the movement of trains, enhancing the overall comfort of passengers and residents in nearby areas. Additionally, they provide electrical insulation, reducing the risk of electric shock. Moreover, rubber rail pads also help to protect the sleepers from premature wear and tear caused by the constant impact of the train wheels, leading to increased longevity and reduced maintenance costs for railway infrastructure.Innovative Technology for Enhanced SafetyThe railway industry is constantly evolving, with the focus on leveraging advanced technologies to improve safety standards. Recognizing the importance of rubber rail pads in achieving this objective, [Company Name] has pioneered innovative technologies to develop state-of-the-art rubber rail pads that redefine industry standards. Their commitment to safety, efficiency, and sustainability has positioned them as a trusted partner across the global railway market.Advanced Design and Manufacturing Processes[Company Name] utilizes advanced design and manufacturing processes to create rubber rail pads that surpass industry expectations. The company's team of experienced engineers and technicians work diligently to incorporate cutting-edge design principles and utilize high-quality materials to ensure the durability and performance of the rubber rail pads. Their comprehensive range of products caters to various railway requirements, accommodating different track gauges, load capacities, and operating conditions.Stringent Quality Control MeasuresWith safety being a primary concern, [Company Name] maintains stringent quality control measures throughout the manufacturing process. The rubber rail pads undergo rigorous testing, adhering to international standards and specifications. The quality control team meticulously inspects and evaluates the products to ensure they meet the necessary criteria for performance, durability, and safety. This dedication to delivering superior quality products has established [Company Name] as a reliable and trusted supplier in the railway industry.Environmental SustainabilityIn addition to focusing on safety and efficiency, [Company Name] is committed to environmental sustainability. The company recognizes the need to develop products that minimize their environmental impact while meeting the demanding requirements of the railway industry. By utilizing eco-friendly materials and adopting sustainable manufacturing practices, [Company Name] ensures that their rubber rail pads contribute to a greener and more sustainable future.Global Presence and Customer Satisfaction[Company Name]'s dedication to innovation, quality, and customer satisfaction has earned them a reputation in the global market. They have successfully established a wide customer base, providing their rubber rail pads to railway networks worldwide. Their commitment to delivering exceptional products, combined with an attentive and responsive customer service team, ensures that clients receive the highest level of satisfaction.Looking AheadAs the railway industry continues to expand, safety and efficiency remain critical to meet the increasing demands of passengers and freight transportation. Rubber rail pads play a vital role in achieving these goals by minimizing vibrations, controlling noise, and protecting the railway infrastructure. [Company Name] remains at the forefront of innovation, continuously striving to enhance the performance and sustainability of their rubber rail pads, ensuring a safer and more efficient railway system for all.In conclusion, rubber rail pads have become indispensable in the railway industry, providing enhanced safety, comfort, and longevity to the tracks and sleepers. [Company Name]'s dedication to innovation, quality, and sustainability has positioned them as a leading manufacturer and supplier of rubber rail pads globally. With their advanced technology, stringent quality control measures, and commitment to customer satisfaction, they continue to shape the future of the railway industry.
Discover the Advantages of Aluminum Die Forging for Superior Strength and Performance
Title: Aluminum Die Forging: The Next Generation Manufacturing SolutionIntroduction:In a world that is constantly evolving, the manufacturing industry continues to seek advanced techniques and materials to propel innovation forward. One such game-changing approach is aluminum die forging, a process that offers enhanced strength, durability, and versatility across various applications. In this news article, we explore the benefits, applications, and the companies at the forefront of this pioneering manufacturing solution.Unleashing the Potential of Aluminum Die Forging:Aluminum die forging is a manufacturing technique that involves shaping aluminum alloys using high-pressure forces. This process offers numerous advantages over traditional methods, such as casting or machining. By subjecting the metal to tremendous pressure, the aluminum is formed into intricate and complex shapes with exceptional strength and precision.The Benefits of Aluminum Die Forging:1. Enhanced Strength: Aluminum die forging results in a higher strength-to-weight ratio, making it ideal for applications that demand lightweight yet robust components. This enables the creation of parts that can withstand high-stress environments and demanding operating conditions.2. Improved Durability: By utilizing aluminum die forging, manufacturers can create parts that exhibit exceptional mechanical properties, including increased fatigue strength and resistance to corrosion. Such durability ensures a longer lifespan and reduces the need for frequent replacements.3. Design Flexibility: Unlike other manufacturing methods, aluminum die forging provides design flexibility, allowing manufacturers to produce intricate shapes with close tolerances. This flexibility enables the development of components that meet precise specifications while guaranteeing optimal performance.4. Cost-efficiency: Despite the advanced manufacturing techniques involved, aluminum die forging offers cost advantages, thanks to reduced material wastage, streamlined production processes, and the capability to manufacture parts in large volumes. As a result, industries can benefit from high-quality yet affordable products.Applications of Aluminum Die Forging:1. Aerospace Industry: The aerospace sector demands exceptionally robust, lightweight, and high-performance components. Aluminum die forging provides the ideal solution for producing components like wing structures, engine parts, and landing gear systems, where strength, weight reduction, and resistance to extreme temperatures are crucial.2. Automotive Industry: In the automotive sector, safety, efficiency, and performance are paramount. By employing aluminum die forging, automobile manufacturers can create lightweight yet durable components such as suspension parts, engine valves, transmission components, and steering systems that contribute to overall vehicle performance and fuel efficiency.3. Defense and Military Applications: The defense sector requires components that can withstand extreme conditions and provide mission-critical reliability. Aluminum die forging enables the production of components such as missile launchers, armored vehicles, and aircraft parts that meet these stringent requirements.Companies Leading the Way:Several companies have emerged as pioneers in the field of aluminum die forging, embracing this revolutionary manufacturing solution and pushing the boundaries of what is possible.1. Company A: This industry leader combines their vast experience in aluminum die forging with cutting-edge technology to produce high-quality components for aerospace, automotive, defense, and other industries. Their expertise and dedication to innovation have established them as a trusted partner for global customers.2. Company B: Leveraging their state-of-the-art facilities, Company B specializes in aluminum die forging that caters to the specialized needs of the aerospace industry. With a focus on precision and reliability, they have become a go-to choice for aviation companies seeking superior components.Conclusion:Aluminum die forging is revolutionizing the manufacturing industry, offering unparalleled strength, durability, and design flexibility. As this technique gains widespread recognition, various industries can leverage its advantages to develop high-performance components that meet challenging requirements. With leading companies investing in this innovative manufacturing solution, the future of aluminum die forging looks promising, opening up new horizons of possibilities for diverse sectors.
Latest Techniques for Creating High-Quality Forged Rings Unveiled in Recent News Content
Introducing the Revolutionary Metal Forging Technology Revolutionizing ManufacturingIn an era where technological advancements are continuously reshaping the global manufacturing landscape, one company has emerged as a frontrunner in revolutionizing metal forging processes. Through their groundbreaking innovation, the team at Forging Ring (name changed for confidentiality) has introduced a cutting-edge metal forging technology that is set to transform the way products are manufactured across industries.Forging has long been considered a crucial process in the production of industrial components. It involves shaping heated metal through the application of extreme pressure, enhancing the strength, durability, and quality of various products. However, traditional forging methods have their limitations, often resulting in lengthy production times and increased costs. This is where Forging Ring's pioneering technology comes into play.Leveraging their deep expertise and commitment to innovation, Forging Ring has developed a proprietary metal forging technique that significantly decreases manufacturing time and allows for greater precision in product design. Their advanced process involves the use of computer-controlled hydraulic presses, automated temperature control systems, and sophisticated algorithms, ultimately improving the efficiency and accuracy of the forging process.The key differentiator of Forging Ring's technology lies in its ability to create complex and intricate shapes while maintaining the structural integrity of the forged component. By taking advantage of high precision die technologies and advanced simulation software, the company has successfully overcome the limitations posed by traditional forging techniques, creating endless opportunities for product development and customization.This groundbreaking technology has garnered notable attention from industry leaders across various sectors. Companies in automotive, aerospace, energy, and defense are showing keen interest in adopting Forging Ring's cutting-edge metal forging technology. The application of this revolutionary technique in these industries could result in lighter, stronger, and more fuel-efficient vehicles, as well as enhanced performance and reliability in aircraft engines and turbines.Furthermore, manufacturers can expect significant cost savings by leveraging Forging Ring's technology. The reduced production time and increased accuracy of the forging process translate to lower labor costs, improved resource utilization, and minimal material waste. The optimization of these factors contributes to a more sustainable manufacturing process, aligning with the growing global emphasis on environmentally friendly production practices.Recognizing the immense potential of their technology, Forging Ring has already invested heavily in research and development to further refine and broaden the scope of their metal forging capabilities. They have established state-of-the-art research facilities staffed by experts in materials engineering, process optimization, and computer modeling, ensuring continuous innovation and advancement in the field of metal forging.Additionally, Forging Ring is actively collaborating with leading academic institutions and research organizations to foster knowledge exchange and stay at the forefront of the industry. By engaging in joint projects and sharing expertise, the company is not only contributing to the advancement of metal forging technology but also reinforcing their commitment to driving progress in the manufacturing sector as a whole.As companies strive to stay competitive in today's rapidly evolving market, the need for innovative manufacturing techniques becomes increasingly evident. Forging Ring's ground-breaking metal forging technology is a testament to the transformative power of continuous innovation and the immense potential it holds for the future of manufacturing. With endless possibilities for customization, increased efficiency, and cost savings, this revolutionary technology is poised to shape the way products are made for years to come.
New Developments in Advanced Excavator Bucket Teeth
Hyundai Construction Equipment (HCE), a global leader in the construction equipment industry, has recently launched its state-of-the-art range of bucket teeth, designed to revolutionize the way construction projects are carried out. These groundbreaking bucket teeth incorporate cutting-edge technology and engineering, promising enhanced productivity, durability, and efficiency for construction teams around the world.With over 80 years of industry experience, Hyundai Construction Equipment has established itself as a reputable and trusted brand in the construction equipment market. The company's commitment to excellence and innovation is showcased in its latest range of bucket teeth, which aim to address the specific needs and challenges faced by construction professionals.One of the key highlights of these bucket teeth is their unmatched durability. Designed to withstand the harshest working conditions, these teeth are constructed from high-quality materials that offer exceptional resistance to wear and tear. Hyundai's advanced manufacturing techniques ensure that the bucket teeth remain sharp and intact for an extended period, minimizing the need for frequent replacements and resulting in significant cost savings for construction companies.Furthermore, the bucket teeth are ergonomically designed to provide ease of use and operator comfort. The innovative tooth profile enables efficient penetration into various types of materials, ensuring smooth excavation and reducing the strain on the machine and its operator. This not only enhances overall productivity but also reduces the risk of fatigue-related errors or accidents on construction sites.Hyundai Construction Equipment's bucket teeth are also designed to maximize efficiency. The unique tooth shape and design optimize the bucket's digging and loading capacity, allowing for faster and more effective operations. The increased efficiency translates into reduced project timelines and improved overall project management for construction companies.Additionally, these bucket teeth are compatible with a wide range of Hyundai's excavators, loaders, and other construction equipment. This versatility ensures that construction professionals can seamlessly integrate the new bucket teeth into their existing fleets, eliminating the need for significant investment in new equipment. As a result, companies can upgrade their machinery without disrupting ongoing projects or incurring unnecessary expenses.Hyundai Construction Equipment's commitment to sustainability is evident in its bucket teeth as well. The company has incorporated eco-friendly materials and manufacturing processes into the production of these teeth, reducing their environmental impact. By choosing Hyundai's bucket teeth, construction companies can contribute to a greener future without compromising on performance or reliability.Beyond the technical prowess of its bucket teeth, Hyundai Construction Equipment also offers superior customer service and support. The company's global network of authorized dealers ensures that construction professionals have access to genuine parts, expert advice, and timely assistance whenever needed. This comprehensive after-sales support ensures that construction companies can maximize the lifespan and performance of their bucket teeth, enhancing the overall return on investment.In conclusion, Hyundai Construction Equipment's launch of its advanced range of bucket teeth marks another milestone in the company's legacy of innovation and excellence. These state-of-the-art bucket teeth offer improved durability, efficiency, and sustainability, empowering construction professionals to overcome challenges and deliver exceptional results. With Hyundai's unwavering commitment to customer satisfaction, construction companies can confidently invest in these bucket teeth, revolutionizing their construction projects and achieving new levels of success.
Unveiling the Intricate Process of Forging: An In-Depth Look
Title: Innovations in the Process of Forging Revolutionize Manufacturing IndustryIntroduction:The process of forging, a centuries-old technique of shaping metal, has undergone a transformation thanks to groundbreaking innovations introduced by several industry leaders. In particular, companies like {} have played a pivotal role in revolutionizing the manufacturing sector through their cutting-edge technologies and techniques. This article discusses how these advancements have improved the forging process, leading to enhanced product quality, increased production efficiency, and higher customer satisfaction.Body:1. The Foundations of Forging:Forging is the process of shaping metal through the application of tremendous pressure, usually with the help of hydraulic or mechanical force. Known for its strength, durability, and reliability, forged components find applications in various industries, including automotive, aerospace, defense, and construction. Traditionally, forging was a labor-intensive process that required skilled craftsmen to manually shape the metal into the desired form. However, with the advent of modern technologies, the forging industry has witnessed significant advancements, which have simplified and optimized the manufacturing process.2. Introduction of Advanced Materials:One key innovation lies in the utilization of advanced materials for forging applications. With the development of high-strength alloys, superalloys, and composite materials, manufacturers now have access to materials with enhanced characteristics, such as superior mechanical properties, heat resistance, and corrosion resistance. By utilizing these advanced materials, companies have been able to produce components that are not only lighter and more durable but also better suited for specific operational conditions.3. Computer-Aided Design and Manufacturing (CAD/CAM) Integration:Integration of computer-aided design and manufacturing (CAD/CAM) systems has been instrumental in streamlining the entire forging process. By digitizing the design, simulation, and manufacturing phases, engineers can now create intricate component geometries with enhanced precision and accuracy. CAD/CAM integration allows for the optimization of tooling and die designs, reducing material waste and production costs while improving overall product quality.4. Automation and Robotics:The introduction of automation and robotics in forging facilities has led to a significant boost in production efficiency and consistency. Intelligent robotic systems can now handle complex tasks previously performed by human operators, such as loading and unloading parts, transferring components between workstations, and performing quality inspections. This integration of automation not only improves productivity and reduces labor costs but also ensures a higher level of precision, repeatability, and safety throughout the manufacturing process.5. Simulation and Predictive Analysis:Simulations and predictive analysis tools are transforming the way manufacturers approach the forging process. Advanced software can simulate the behavior of metals under extreme heat and pressure, accurately predicting how they will deform, crack, or fail. By simulating different scenarios, engineers can optimize the process parameters, tooling designs, and material selection, reducing the time and costs associated with physical prototyping and testing. This technological advancement allows for faster development cycles, improved component quality, and increased overall efficiency.6. Additive Manufacturing in Forging:Additive manufacturing, often referred to as 3D printing, has also found its way into the realm of forging. Through the utilization of metal powders and advanced printing techniques, complex components can be fabricated layer by layer, eliminating the need for traditional forging processes. This disruptive technology offers increased design flexibility, reduced material waste, and shorter production times, enabling manufacturers to create intricate and lightweight components that were previously unattainable.7. Quality Assurance and Traceability:In addition to process improvements, modern forging techniques have also enhanced quality assurance and traceability. Manufacturers now employ advanced inspection technologies, such as non-destructive testing and optical measurement systems, to ensure that components meet the highest industry standards. Additionally, blockchain-based systems facilitate real-time traceability, providing customers with transparent information about the origin, production, and testing of forged components. These advancements instill confidence in the quality and reliability of the products while meeting the rigorous demands of various regulatory bodies.Conclusion:The evolution of the forging process, driven by the innovative technologies introduced by companies such as {}, has ushered in a new era of manufacturing excellence. From advanced materials and CAD/CAM integration to automation, simulation, and additive manufacturing, these advancements have significantly improved product quality, production efficiency, and customer satisfaction. The future of forging appears promising, with continued research and development propelling the industry towards greater innovation and success.
Improve Floor Safety with Durable and Versatile Plastic Floor Pads
Plastic Floor Pad Revolutionizes Cleaning Industry with Cutting-Edge TechnologyIn recent years, the demand for efficient and effective cleaning solutions has been on the rise, and that's where the plastic floor pad, pioneered by an innovative company, comes into play. With a vision to provide the cleaning industry with a game-changing solution, this company has completely transformed the way floors are cleaned. By combining cutting-edge technology with a commitment to sustainable practices, the plastic floor pad has quickly become the go-to choice for businesses and households around the globe.Traditional floor cleaning methods typically involve the use of bulky and cumbersome equipment that is not only time-consuming but also inefficient. However, with the introduction of the plastic floor pad, cleaning tasks have become much easier and more cost-effective. This revolutionary product is made from a durable and eco-friendly plastic material, which ensures optimal performance while also reducing environmental impact.One of the key features that sets the plastic floor pad apart from its competitors is its unique design. The advanced technology used in its manufacturing process allows for an increased surface area, resulting in a much more efficient cleaning process. The pad's microfibers are intricately woven together, creating a strong yet gentle material that tackles even the toughest dirt and grime.Another significant advantage of the plastic floor pad is its versatility. It can be used on a wide range of surfaces, including hardwood, laminate, and tile floors, making it an ideal choice for both residential and commercial applications. Whether it's removing stubborn stains or simply giving floors a deep clean, this product is guaranteed to deliver outstanding results every time.Furthermore, the plastic floor pad is equipped with a user-friendly attachment system, which makes it compatible with most cleaning machines available in the market. This means that upgrading existing cleaning equipment to incorporate this innovative pad is a straightforward and cost-effective process for businesses. Additionally, its easy-to-remove and replace design ensures minimal downtime during the cleaning process, resulting in increased efficiency and productivity.Moreover, the company behind the plastic floor pad is committed to sustainability, and this dedication is deeply ingrained in every aspect of their operations. By utilizing recycled plastic materials in the pad's manufacturing process, they are actively contributing to reducing plastic waste and promoting a circular economy. This commitment to sustainable practices has garnered the company widespread recognition and praise from environmental organizations worldwide.The plastic floor pad has already made significant waves in the cleaning industry, revolutionizing the way floors are cleaned. Its cutting-edge technology, versatility, and commitment to sustainability have earned it a loyal customer base and numerous accolades. Users have reported remarkable improvements in cleaning efficiency, reduced cleaning costs, and a noticeable decrease in environmental impact.As the demand for eco-friendly and efficient cleaning solutions continues to grow, the plastic floor pad is poised to dominate the market. With its revolutionary design, commitment to sustainability, and proven effectiveness, it is not surprising that more and more businesses and households are making the switch. Embracing this innovative technology allows for cleaner and healthier living and working environments while minimizing our impact on the planet.In conclusion, the plastic floor pad has become a game-changer in the cleaning industry. With its revolutionary design, advanced technology, and commitment to sustainability, it has transformed the way floors are cleaned. As businesses and households continue to prioritize efficiency and environmental responsibility, the plastic floor pad is at the forefront, leading the charge towards a cleaner and greener future.
Discover How Die Casting Machines Streamline Manufacturing Processes
[Company Introduction]Company XYZ is a renowned name in the manufacturing industry, specializing in the production of advanced machinery and technology solutions. With over two decades of experience, the company has successfully established itself as a key player in providing high-quality, innovative products to a diverse range of sectors. Recognized for its commitment to excellence, XYZ focuses on delivering cutting-edge solutions that enhance productivity and efficiency for its global clientele.[News Content]In a significant milestone for the manufacturing industry, Company XYZ has unveiled its latest die casting machine, revolutionizing the production process for various sectors. Designed to meet the growing demands of the market, this state-of-the-art machine offers enhanced precision, efficiency, and productivity, setting a new benchmark for die casting technology.Die casting is a widely used manufacturing process that involves injecting molten metal into a mold cavity under high pressure. It is a critical technique employed in industries such as automotive, aerospace, and consumer electronics. The new die casting machine from Company XYZ aims to address the challenges faced by manufacturers, ensuring optimal results and reducing overall production costs.One of the key features of this advanced die casting machine is its cutting-edge hydraulic system. With highly responsive and precise controls, the machine provides exceptional accuracy during the injection process, minimizing defects and ensuring consistent quality. The hydraulic system also offers energy-saving capabilities, contributing to reduced operating costs and a smaller carbon footprint.Additionally, the die casting machine incorporates an intuitive user interface, enabling operators to streamline operations with ease. The user-friendly control panel allows for real-time monitoring of production parameters, ensuring efficient performance and facilitating prompt adjustments when necessary. This innovative interface reduces the learning curve for operators, promoting a seamless transition to the new technology.Company XYZ has also prioritized safety in the design of the die casting machine. Equipped with advanced safety features, including emergency stop buttons, protective barriers, and motion sensors, the machine prioritizes the well-being of operators while minimizing the risk of accidents or injuries. By investing in comprehensive safety measures, XYZ aims to create a conducive working environment that enhances productivity and promotes employee welfare."The launch of our new die casting machine represents a breakthrough in manufacturing technology," stated John Doe, CEO of Company XYZ. "Our team of skilled engineers have worked relentlessly to develop a machine that meets the evolving needs of our clients. We are confident that this cutting-edge solution will maximize efficiency, improve product quality, and elevate the overall industry standards."The die casting machine from Company XYZ has garnered significant attention from manufacturers across the globe. With its superior performance, cost-effectiveness, and emphasis on safety, it aims to revolutionize the production process and drive the industry forward. By leveraging the benefits of this innovative machinery, manufacturers can streamline their operations, enhance their competitiveness, and meet the ever-increasing demands of the market.In conclusion, Company XYZ's latest die casting machine marks a significant advancement in manufacturing technology. Combining precision, efficiency, and safety, this state-of-the-art machine sets a new standard for the industry. As manufacturers strive for excellence in a fiercely competitive market, solutions like XYZ's die casting machine can provide the edge needed to thrive and succeed.
Essential Guidelines for Stainless Steel Casting: A Comprehensive Overview
Stainless Steel Casting: A Precise and Reliable Manufacturing ProcessThe manufacturing industry constantly evolves to meet the ever-growing demands of various sectors. One process that has gained substantial popularity is stainless steel casting. Being a highly reliable and precise method of manufacturing, it has become an essential part of our modern industrial landscape.Stainless steel casting involves creating intricate shapes and structures by pouring molten stainless steel into a mold. As the steel cools and solidifies, it takes the shape of the mold, resulting in a finished product that adheres to precise specifications. This process allows for the production of complex and intricate parts that would be extremely difficult, if not impossible, to fabricate using alternative manufacturing techniques.One noteworthy company that has mastered the art of stainless steel casting is {}. With decades of experience and a solid reputation, they have become a key player in the industry. Their commitment to excellence and innovative approach have made them a preferred choice for businesses across various sectors.Founded in {}, {} has dedicated itself to perfecting the stainless steel casting process. Their state-of-the-art facilities are equipped with advanced technology and machinery, allowing them to deliver high-quality and accurate products consistently. Moreover, their team of experienced engineers and technicians ensures that each casting meets the stringent standards set by their clients.The advantages of stainless steel casting are multifaceted and have contributed to its widespread adoption. First and foremost, stainless steel is well-known for its exceptional durability and resistance to corrosion, making it ideal for applications that require longevity and reliability. The casting process only enhances these properties, ensuring that the final product possesses the same durability and corrosion resistance.Furthermore, stainless steel casting enables the production of intricate shapes and designs. This level of detail allows for greater design flexibility and opens up possibilities in various industries, including automotive, aerospace, and medical. By eliminating the need for extensive machining and welding, the process not only reduces costs but also minimizes production time, leading to faster delivery to customers.Another advantage of stainless steel casting is its ability to maintain dimensional accuracy. The molds used in the process can be precise, resulting in parts with tight tolerances. This level of accuracy is critical for industries such as automotive and aerospace, where even the slightest deviation can lead to disastrous consequences.In addition to its accuracy, stainless steel casting offers cost-effective solutions. The process requires minimal tooling, reducing upfront costs. This aspect, combined with the ability to produce complex structures as a single piece, eliminates the need for assembly or joining, further decreasing production costs. Additionally, the durability and longevity of stainless steel reduce maintenance and replacement expenses, making it a cost-efficient choice in the long run.The applications of stainless steel casting are vast and diverse. In the automotive industry, it is used in manufacturing engine components, exhaust systems, and transmission parts. In aerospace, it finds its place in creating turbine blades, engine casings, and other critical components. The medical field benefits from stainless steel casting by creating surgical instruments, prosthetics, and dental implants. These are just a few examples of the extensive range of applications where stainless steel casting excels.As the demand for high-quality, precise, and durable products grows, stainless steel casting remains a prominent solution in the manufacturing industry. Companies like {} play a vital role in meeting this demand and driving innovation. Their dedication to perfection and cutting-edge technology positions them as leaders in the industry.In conclusion, stainless steel casting represents an essential manufacturing process due to its precision, durability, and versatility. With its applications spanning across various industries, it continues to shape our modern industrial landscape. Companies like {} have mastered this technique, proving their commitment to excellence and delivering quality products. The future of stainless steel casting looks bright as it remains at the forefront of manufacturing advancements.
Streamlined Guide to Gravity Die Casting: Everything You Need to Know
Gravity Die Casting: Efficient and Precise Manufacturing TechnologyIn the world of manufacturing and production, efficiency and precision are the key factors that contribute to the success of any company. One such technology that has revolutionized the industry is gravity die casting - a method employed for manufacturing high-quality metal components with exceptional dimensional accuracy. Today, we will explore the gravity die casting process and its impact on the manufacturing sector, focusing on the remarkable achievements of a leading company {}.Gravity die casting, also known as permanent mold casting, is a reliable and cost-effective method to produce complex metal components with consistent quality. The process involves pouring molten metal into a metallic mold, which is later cooled and solidified to form the desired shape. Unlike other casting techniques, gravity die casting utilizes the force of gravity to fill the mold, resulting in reduced turbulence and better control over the casting process. This ensures improved surface finish, dimensional accuracy, and enhanced mechanical properties of the end product.Established in {}, {} has emerged as a pioneer in gravity die casting technology. With a stellar reputation built on years of experience and innovation, the company has successfully catered to the diverse needs of industries such as automotive, aerospace, defense, and consumer goods. Their commitment to quality and continuous improvement has propelled them to the forefront of the gravity die casting industry.Taking advantage of advanced machinery and state-of-the-art facilities, {} offers a comprehensive range of gravity die casting services. Their team of highly skilled engineers and technicians meticulously design and manufacture the molds required for the casting process. This ensures that each component produced adheres to the strictest specifications and quality standards. Furthermore, {} boasts an extensive material selection, allowing customers to choose from various alloys, including aluminum, zinc, and brass.The benefits of gravity die casting extend beyond the impeccable quality of the components. Its cost-efficiency, by reducing material waste and minimizing machining requirements, makes it an attractive choice for manufacturers. Additionally, the process is highly scalable, enabling {} to meet both low and high volume production demands without compromising on quality or lead times. Their dedication to delivering on-time and within budget has earned them the trust of numerous renowned clients.While gravity die casting is primarily associated with metal components, {} has pushed the boundaries of this manufacturing process. Their continuous investment in research and development has allowed them to expand their capabilities to include innovative applications such as gravity die casting of ceramics and composites. This pioneering approach has opened new doors in various industries and positioned {} as a leading provider of cutting-edge casting solutions.However, {}'s achievements are not limited to technological prowess alone. As a socially responsible company, they prioritize sustainability and environmental conservation. By implementing eco-friendly practices such as recycling and waste reduction, the company minimizes its carbon footprint and contributes to a greener future. This commitment to sustainable manufacturing has garnered {} recognition and accolades from industry peers and regulatory bodies alike.In conclusion, gravity die casting has revolutionized the manufacturing sector by offering efficient and precise production of high-quality metal components. With {} at the forefront of this technology, companies across various industries benefit from their exceptional expertise and commitment to excellence. As they continue to push boundaries and explore new frontiers in casting, {} establishes itself as an unrivaled leader in the field.