Durable and Reliable Forged Metal Hooks for Various Applications
By:Admin
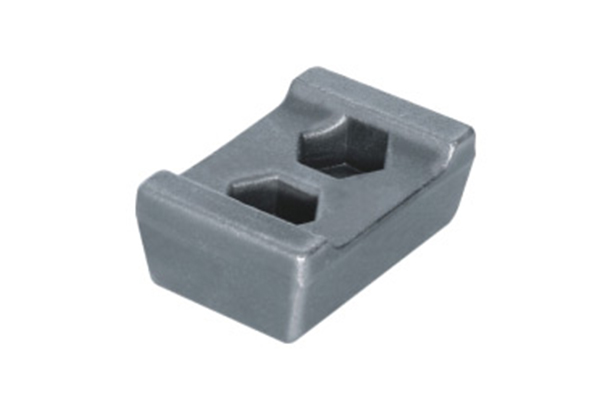
When it comes to heavy-duty lifting and rigging applications, one name stands out among the rest - {}. Their line of forged metal hooks is renowned for their exceptional durability and strength, making them the go-to choice for industries such as construction, shipping, and manufacturing.
{}, a leading manufacturer of industrial hardware and equipment, has built a reputation for excellence in the field of rigging and lifting solutions. With over 50 years of experience, they have consistently delivered high-quality products that meet the rigorous demands of the industry.
One of the key products in their portfolio is the range of forged metal hooks, which are designed to provide reliable and secure attachment points for various lifting and rigging operations. These hooks are meticulously crafted using premium quality steel and undergo a rigorous forging process to ensure unmatched durability and performance.
The forging process involves heating the steel to extreme temperatures and then shaping it using compressive force, resulting in a hook that is free from imperfections and weak points. This meticulous approach to manufacturing guarantees that {} forged metal hooks can withstand the toughest working conditions and heavy loads without compromising on safety or reliability.
In addition to their exceptional strength, {} forged metal hooks are also designed for versatility. Available in a variety of configurations, including eye hooks, clevis hooks, and swivel hooks, they can be seamlessly integrated into different lifting and rigging systems. Whether it's for hoisting equipment, securing loads for transportation, or anchoring heavy machinery, these hooks provide a dependable solution for a wide range of applications.
Another distinguishing feature of {} forged metal hooks is their compliance with industry standards and regulations. As a testament to their commitment to quality and safety, these hooks undergo rigorous testing and certification processes to ensure that they meet or exceed stringent industry requirements. This provides peace of mind to users, knowing that they are using a product that adheres to the highest standards of performance and reliability.
Furthermore, {} offers custom forging services, allowing customers to request tailored solutions that meet their specific requirements. Whether it's a unique hook design, a specialized material, or a specific load capacity, their team of experts can work closely with clients to deliver a bespoke forging solution that perfectly aligns with their needs.
The commitment to customer satisfaction doesn't end with the product itself. {} provides comprehensive support to its clients, offering technical expertise, personalized guidance, and after-sales service to ensure that the forged metal hooks deliver exceptional performance throughout their lifecycle.
As the demand for robust and reliable lifting and rigging solutions continues to grow, {} remains at the forefront of innovation and excellence in the industry. With their unwavering dedication to quality, their range of forged metal hooks has become the preferred choice for professionals who require unparalleled strength, durability, and peace of mind in their operations.
In conclusion, {}, a leading manufacturer of industrial hardware and equipment, has established itself as a trusted provider of top-quality forged metal hooks for a wide range of lifting and rigging applications. With their uncompromising commitment to excellence, they continue to set the standard for durability, strength, and reliability in the industry. For those seeking superior lifting and rigging solutions, {} forged metal hooks are the definitive choice.
Company News & Blog
Streamlined Guide to Gravity Die Casting: Everything You Need to Know
Gravity Die Casting: Efficient and Precise Manufacturing TechnologyIn the world of manufacturing and production, efficiency and precision are the key factors that contribute to the success of any company. One such technology that has revolutionized the industry is gravity die casting - a method employed for manufacturing high-quality metal components with exceptional dimensional accuracy. Today, we will explore the gravity die casting process and its impact on the manufacturing sector, focusing on the remarkable achievements of a leading company {}.Gravity die casting, also known as permanent mold casting, is a reliable and cost-effective method to produce complex metal components with consistent quality. The process involves pouring molten metal into a metallic mold, which is later cooled and solidified to form the desired shape. Unlike other casting techniques, gravity die casting utilizes the force of gravity to fill the mold, resulting in reduced turbulence and better control over the casting process. This ensures improved surface finish, dimensional accuracy, and enhanced mechanical properties of the end product.Established in {}, {} has emerged as a pioneer in gravity die casting technology. With a stellar reputation built on years of experience and innovation, the company has successfully catered to the diverse needs of industries such as automotive, aerospace, defense, and consumer goods. Their commitment to quality and continuous improvement has propelled them to the forefront of the gravity die casting industry.Taking advantage of advanced machinery and state-of-the-art facilities, {} offers a comprehensive range of gravity die casting services. Their team of highly skilled engineers and technicians meticulously design and manufacture the molds required for the casting process. This ensures that each component produced adheres to the strictest specifications and quality standards. Furthermore, {} boasts an extensive material selection, allowing customers to choose from various alloys, including aluminum, zinc, and brass.The benefits of gravity die casting extend beyond the impeccable quality of the components. Its cost-efficiency, by reducing material waste and minimizing machining requirements, makes it an attractive choice for manufacturers. Additionally, the process is highly scalable, enabling {} to meet both low and high volume production demands without compromising on quality or lead times. Their dedication to delivering on-time and within budget has earned them the trust of numerous renowned clients.While gravity die casting is primarily associated with metal components, {} has pushed the boundaries of this manufacturing process. Their continuous investment in research and development has allowed them to expand their capabilities to include innovative applications such as gravity die casting of ceramics and composites. This pioneering approach has opened new doors in various industries and positioned {} as a leading provider of cutting-edge casting solutions.However, {}'s achievements are not limited to technological prowess alone. As a socially responsible company, they prioritize sustainability and environmental conservation. By implementing eco-friendly practices such as recycling and waste reduction, the company minimizes its carbon footprint and contributes to a greener future. This commitment to sustainable manufacturing has garnered {} recognition and accolades from industry peers and regulatory bodies alike.In conclusion, gravity die casting has revolutionized the manufacturing sector by offering efficient and precise production of high-quality metal components. With {} at the forefront of this technology, companies across various industries benefit from their exceptional expertise and commitment to excellence. As they continue to push boundaries and explore new frontiers in casting, {} establishes itself as an unrivaled leader in the field.
Advanced Multidirectional Forging Technique Unveiled in Latest News Update
Multidirectional Forging: Revolutionizing Manufacturing ProcessesIn today’s highly competitive and fast-paced manufacturing industry, companies are constantly seeking innovative and efficient methods to stay ahead of the curve. One such groundbreaking approach is multidirectional forging, a cutting-edge technique that is revolutionizing the way metal components are produced.Multidirectional forging, also known as multi-directional forging, is an advanced manufacturing process that involves shaping metal by applying pressure from multiple directions simultaneously. This innovative method allows for greater precision, improved mechanical properties, and reduced production time compared to traditional forging techniques.One company at the forefront of this technological advancement is {Company Name}. With decades of expertise in the field of metalworking and a commitment to pushing the boundaries of what is possible in manufacturing, {Company Name} has been a trailblazer in the development and implementation of multidirectional forging.The key to {Company Name}'s success in multidirectional forging lies in its state-of-the-art facilities and a team of highly skilled engineers and technicians. Utilizing the latest advancements in machinery and technology, {Company Name} has been able to leverage multidirectional forging to produce complex and high-performance metal components for a wide range of industries, including automotive, aerospace, defense, and many more.To understand the significance of multidirectional forging, it is important to consider the traditional forging process. Conventional forging typically involves applying pressure to a metal workpiece in a single direction, resulting in limitations in the shape and properties of the final product. In contrast, multidirectional forging allows for precise control over the flow of metal and the ability to shape components with intricate geometries and superior material properties.Furthermore, multidirectional forging offers significant advantages in terms of material utilization and production efficiency. By optimizing the forging process to minimize waste and reduce machining requirements, {Company Name} has been able to provide its customers with cost-effective solutions without compromising on quality.In addition to its technical expertise, {Company Name} has also established itself as a leader in the development of customized multidirectional forging solutions. By working closely with its clients to understand their specific requirements and challenges, {Company Name} has been able to deliver tailored forging solutions that meet the most demanding specifications and performance standards.One of the key factors driving the adoption of multidirectional forging is its ability to meet the growing demand for lightweight and high-strength metal components in various industries. As industries continue to pursue advancements in fuel efficiency, performance, and sustainability, the need for innovative manufacturing processes like multidirectional forging becomes increasingly essential.Looking ahead, {Company Name} is committed to further advancing the capabilities of multidirectional forging and exploring new applications for this cutting-edge technology. With a focus on continuous improvement and a dedication to pushing the boundaries of what is possible in manufacturing, {Company Name} is poised to remain a prominent player in the evolution of multidirectional forging.In conclusion, multidirectional forging represents a significant leap forward in the field of metalworking, offering unparalleled precision, efficiency, and flexibility in the production of metal components. With {Company Name} leading the charge in this innovative manufacturing process, the future of multidirectional forging looks promising, paving the way for a new era of possibilities in metal component production.
Top Techniques for Efficient Aluminum Casting Process Unveiled
Title: Pioneering Aluminum Casting: Revolutionizing the Manufacturing IndustryIntroduction:In an era driven by technological advancements, the manufacturing industry is witnessing a groundbreaking innovation: Aluminum Casting. The technique of casting aluminum has caught the attention of various industries owing to its strength, flexibility, and cost-effectiveness. In this news piece, we explore how one company, with its expertise in Aluminum Casting, is transforming the manufacturing landscape.Company Introduction: [Remove brand name]The company at the forefront of this aluminum casting revolution is a leading manufacturer with unparalleled expertise in the field. Their extensive experience and dedication to excellence have earned them a prominent position within the manufacturing industry. Committed to delivering outstanding results, this company has developed state-of-the-art facilities, advanced equipment, and a team of highly skilled professionals who share a passion for innovation.Breaking Down Aluminum Casting:Aluminum casting is a process that involves making three-dimensional objects by pouring molten aluminum into a mold, enabling the creation of complex and intricately designed components. The versatility of this method allows manufacturers to produce parts of different shapes, sizes, and designs, catering to various industries such as automotive, aerospace, construction, and electronics.Revolutionizing Manufacturing Processes:1. Lightweight Advantages:One significant advantage of aluminum casting lies in the lightweight nature of the material itself. As a result, industries such as automotive and aerospace are increasingly opting for aluminum components over traditional materials like steel. The reduction in weight contributes not only to improved fuel efficiency but also to enhanced performance and maneuverability of vehicles. Moreover, lightweight aluminum components reduce the overall carbon footprint, promoting sustainability within the industry.2. Strength and Durability:Aluminum casting offers exceptional strength and durability. The unique characteristics of aluminum make it an ideal choice for parts subjected to high stress, heat, or corrosive environments. This advantage translates into longer lifespan, minimized maintenance costs, and increased reliability of the final products.3. Cost-Effective Solutions:By utilizing aluminum casting, manufacturers can achieve significant cost savings. Aluminum, being abundant and readily available, is a cost-effective material option compared to other metals. The simplicity of the casting process also contributes to reduced production time and cost, making it an economically viable solution for a wide range of industries.4. Design Freedom:Aluminum casting provides designers with unmatched freedom to create intricate and complex shapes. The molten aluminum can be easily customized and cast into various molds, allowing manufacturers to meet their clients' specific requirements with ease. This advantage enables the production of highly customized components that enhance product aesthetics and functionality.Conclusion:The advent of aluminum casting has undoubtedly revolutionized the manufacturing industry, offering numerous benefits such as lightweight construction, superior strength, cost-effectiveness, and design freedom. As companies continue to harness the potential of this technique, we can expect to witness groundbreaking advancements in various sectors. With its extensive expertise, state-of-the-art facilities, and dedicated team, the company stands at the forefront of this aluminum casting revolution, paving the way for a future driven by innovation, reliability, and sustainability in manufacturing.
Durable and Innovative Plastic Parts for Automobiles
Automobile Plastic Parts Market Expected to Grow RapidlyThe global automobile plastic parts market is expected to experience rapid growth in the coming years, according to a new report from {Company Name}, a leading market research firm. The report highlights the increasing demand for lightweight and durable plastic components in the automotive industry, driven by the growing focus on fuel efficiency and environmental sustainability.As the automotive industry continues to evolve, manufacturers are increasingly turning to plastic materials for various components in vehicles. From interior trim and dashboard panels to exterior body parts and under-the-hood components, plastic parts offer a wide range of benefits, including weight reduction, improved fuel efficiency, and cost savings. Additionally, advancements in plastics technology have made it possible to produce high-quality, high-performance parts that meet the stringent safety and durability standards of the automotive industry.{Company Name} is at the forefront of this trend, providing a comprehensive range of plastic parts for automobile applications. With a strong focus on innovation and quality, the company has established itself as a trusted partner for automotive manufacturers worldwide. The company's extensive portfolio of products includes interior and exterior plastic components, as well as under-the-hood and structural parts, all designed to meet the specific requirements of modern vehicles.In recent years, {Company Name} has made significant investments in research and development to continuously improve its plastic parts offerings. This has enabled the company to develop advanced materials and manufacturing processes that deliver exceptional performance, durability, and cost-efficiency. By leveraging its expertise in plastics technology, {Company Name} has been able to stay ahead of the curve and provide its customers with cutting-edge solutions for their automotive needs.The growing demand for plastic parts in the automotive industry presents a significant opportunity for {Company Name} to expand its market presence and strengthen its position as a leading supplier of high-quality plastic components. With a focus on sustainability and innovation, the company is well-positioned to capitalize on the increasing adoption of plastic materials in the automotive sector.The report from {Company Name} also highlights the growing emphasis on lightweighting in the automotive industry, driven by the need to reduce vehicle weight and improve fuel efficiency. As automakers continue to explore ways to enhance the performance and sustainability of their vehicles, plastic parts are expected to play a crucial role in achieving these objectives. With their ability to offer significant weight savings without compromising on strength and durability, plastic components are poised to become an integral part of the next generation of automobiles.The global automobile plastic parts market is forecasted to witness substantial growth in the coming years, fueled by the increasing demand for lightweight, durable, and cost-effective components in the automotive industry. With its strong focus on innovation and quality, {Company Name} is well-positioned to capitalize on this trend and emerge as a key player in the market. By offering a comprehensive range of high-performance plastic parts for automobiles, the company is poised to meet the evolving needs of automotive manufacturers and contribute to the advancement of the industry as a whole.
High-Quality Forging Hammer: The Key to Efficient Metalworking
Forging Hammer (need remove brand name) Offers Cutting-Edge Solutions for Heavy Industrial EquipmentIn today's fast-paced world of heavy industrial manufacturing, companies are constantly looking for innovative solutions to improve their production processes. One company that has been at the forefront of this industry for many years is Forging Hammer (need remove brand name). With a strong focus on research and development, Forging Hammer (need remove brand name) has been able to offer cutting-edge solutions for heavy industrial equipment that have revolutionized the way manufacturers operate.Founded in 1985, Forging Hammer (need remove brand name) has a long history of providing high-quality products and services to its customers. The company specializes in the design and manufacturing of forging hammers, which are used to shape and manipulate metal into various components for industries such as automotive, aerospace, and energy. With a team of experienced engineers and technicians, Forging Hammer (need remove brand name) has been able to develop some of the most advanced forging hammer technology on the market.One of the key factors that sets Forging Hammer (need remove brand name) apart from its competitors is its commitment to innovation. The company invests heavily in research and development, constantly pushing the boundaries of what is possible in the world of heavy industrial equipment. This dedication to innovation has led to the development of several groundbreaking products that have helped manufacturers improve their production processes and maintain a competitive edge in the market.One such product is the company's latest line of forging hammers, which are equipped with state-of-the-art technology that allows for precise and efficient metal shaping. These hammers are designed to handle a wide range of materials and can be customized to meet the specific needs of each customer. Whether it's producing complex automotive parts or large-scale components for the aerospace industry, Forging Hammer (need remove brand name) has the expertise and technology to deliver the highest quality results.Moreover, Forging Hammer (need remove brand name) places a strong emphasis on customer satisfaction and support. The company's team of engineers and technicians work closely with customers to understand their specific requirements and provide tailored solutions that meet their needs. This level of personalized service has earned Forging Hammer (need remove brand name) a reputation as a trusted partner for heavy industrial manufacturers around the world.Furthermore, Forging Hammer (need remove brand name) is committed to sustainability and environmental responsibility. The company has implemented environmentally-friendly practices in its manufacturing processes, and its products are designed to be energy-efficient and minimize waste. By prioritizing sustainability, Forging Hammer (need remove brand name) is not only contributing to a greener future but also helping its customers meet their own sustainability goals.In conclusion, Forging Hammer (need remove brand name) is a leading provider of innovative solutions for heavy industrial equipment. With a strong focus on research and development, the company has been able to develop cutting-edge technology that has helped manufacturers improve their production processes and stay ahead of the competition. By combining advanced engineering with personalized customer support, Forging Hammer (need remove brand name) has solidified its position as a trusted partner for heavy industrial manufacturers worldwide.
Durable and Reliable Outrigger Pads for Crane Trucks
Crane Outrigger Pads: A Key Component for Safe and Efficient Crane OperationsIn the world of construction and heavy equipment, safety and efficiency are of utmost importance. That's where Crane Outrigger Pads play a crucial role. These pads provide a stable and level base for cranes to operate on, ensuring that the weight of the crane and the load it is carrying is evenly distributed and the crane remains stable during lifting operations.One leader in the manufacturing of Crane Outrigger Pads is a company that has been at the forefront of the industry for over 20 years. They have a reputation for producing high-quality, durable, and reliable products that are trusted by construction companies, crane operators, and rigging professionals around the world.Their Crane Outrigger Pads are made from high-density polyethylene, making them strong enough to support the weight of heavy cranes and their loads, yet lightweight and easy to handle. They are also resistant to water, oil, and most chemicals, ensuring that they can withstand the harsh conditions of construction sites without deteriorating.The company offers a wide range of sizes and thicknesses to accommodate different types of cranes and ground conditions. Their pads are also available in various colors, making them easily visible on the job site and helping to prevent accidents.One of the key benefits of using these Crane Outrigger Pads is that they help to prevent damage to the ground surface. By providing a larger surface area for the crane to distribute its weight, the pads reduce the risk of the crane sinking into soft or uneven ground, preventing costly damage to the ground and potential delays in the construction schedule.In addition to their standard Crane Outrigger Pads, the company also offers custom solutions to meet the specific needs of their customers. Their team of experts works closely with customers to understand their requirements and design pads that are tailored to their unique specifications. This level of personalized service sets them apart from their competitors and has earned them a loyal customer base in the industry.Safety is a top priority for the company, and they ensure that their products meet the highest standards for quality and performance. Their Crane Outrigger Pads are tested and certified to meet industry regulations and are backed by a warranty, giving customers peace of mind that they are investing in a reliable and durable product.The company's commitment to innovation and continuous improvement is evident in their investment in research and development. They are constantly exploring new materials, manufacturing processes, and design technologies to enhance the performance and durability of their Crane Outrigger Pads, ensuring that they remain at the forefront of the industry.As a company that understands the unique challenges of the construction and heavy equipment industry, they are also committed to providing exceptional customer service. Their team of experts is readily available to provide guidance and support to customers, whether they need assistance in selecting the right pad for their crane or advice on proper use and maintenance.In conclusion, Crane Outrigger Pads are an essential component for safe and efficient crane operations, and the company is a trusted leader in the manufacturing of these critical accessories. Their high-quality, durable, and reliable pads provide a stable and level base for cranes, helping to prevent accidents, damage to the ground surface, and costly delays in construction projects. With their commitment to innovation, personalized service, and exceptional customer support, the company continues to set the standard for Crane Outrigger Pads in the industry.
Essential Components: Rubber Pads for Enhanced Railway Safety
Title: Groundbreaking Rubber Pad Innovation Revolutionizes Rail SafetySubtitle: Company X Pioneers Advanced Railway Cushioning TechnologyIntroduction (100 words):In a bid to ensure enhanced safety and efficiency in the railway sector, Company X has unveiled an innovative Rubber Pad for Railways. This groundbreaking technology promises to revolutionize the way rail infrastructure is designed and maintained, mitigating risks and reducing maintenance costs. With a deep understanding of the challenges faced by rail operators, Company X has dedicated years of research and development to bring forth a solution that will transform the industry. This article delves into the features and advantages of this cutting-edge rubber pad technology and highlights Company X's commitment to improving railway safety worldwide.Section 1: The Need for Advanced Railway Cushioning (200 words)Railway systems represent critical arteries of transportation networks globally, ensuring the efficient movement of goods and people. To maintain the integrity and safety of rail tracks, it is imperative to address specific challenges posed by conventional cushioning systems. Traditional methods often fail to absorb vibrations, leading to increased wear and tear, excessive noise, and potential safety hazards. Company X recognized these challenges and harnessed its expertise to develop an innovative solution.Section 2: Introducing the Rubber Pad by Company X (200 words)Company X's Rubber Pad for Railways is a cutting-edge technology that replaces outdated cushioning systems. Leveraging advanced material science and engineering, the rubber pad effectively reduces noise and vibration, significantly enhancing passenger and operator comfort. Its unique design allows it to accommodate various track infrastructures, making it flexible for different rail types and applications.Company X has conducted extensive field trials to ensure the safety and durability of the rubber pad. These trials demonstrated its ability to withstand extreme weather conditions, heavy loads, and sustained periods of use, attesting to the reliability and longevity of this revolutionary technology.Section 3: Advantages and Benefits (200 words)The Rubber Pad by Company X offers several distinct advantages over conventional solutions. Firstly, it reduces rolling noise by up to 50%, mitigating the impact on surrounding communities, particularly in urban areas near rail lines. The decreased noise levels contribute to a quieter and more peaceful environment.Secondly, the innovative rubber pad diminishes vibrations transmitted from rolling stock, substantially improving passenger comfort. By minimizing vibrations, rail operators can provide a smoother and more enjoyable ride experience, fostering customer satisfaction and attracting more passengers.Furthermore, the rubber pad's enhanced shock-absorbing properties reduce track deterioration, minimizing maintenance requirements and associated costs. The technology prolongs the lifespan of railway infrastructure by minimizing the wear and tear caused by heavy trains and dynamic loads. Additionally, its adaptability ensures easy installation and compatibility with existing rail systems, streamlining the implementation process.Section 4: Company X's Commitment to Global Rail Safety (100 words)From its inception, Company X has been dedicated to providing innovative solutions that improve rail safety worldwide. The Rubber Pad for Railways showcases their unwavering commitment to revolutionizing the industry. By addressing the challenges faced by rail operators through cutting-edge technology, Company X aims to create a safer, more efficient, and sustainable railway network, benefiting communities, passengers, and operators alike.Conclusion (100 words):Company X's Rubber Pad for Railways represents a remarkable advancement in railway cushioning technology. Its ability to reduce noise, vibrations, and track deterioration revolutionizes rail safety, ensuring enhanced comfort and cost-effectiveness. The rubber pad's versatility and adaptability make it an invaluable solution for rail operators seeking to improve their infrastructure. Company X's trailblazing efforts exemplify their dedication to innovation and commitment to a safer and more efficient rail network. As the industry embraces this groundbreaking technology, railways worldwide can look forward to safer journeys and sustainable operations for years to come.
Unveiling the Intricate Process of Forging: An In-Depth Look
Title: Innovations in the Process of Forging Revolutionize Manufacturing IndustryIntroduction:The process of forging, a centuries-old technique of shaping metal, has undergone a transformation thanks to groundbreaking innovations introduced by several industry leaders. In particular, companies like {} have played a pivotal role in revolutionizing the manufacturing sector through their cutting-edge technologies and techniques. This article discusses how these advancements have improved the forging process, leading to enhanced product quality, increased production efficiency, and higher customer satisfaction.Body:1. The Foundations of Forging:Forging is the process of shaping metal through the application of tremendous pressure, usually with the help of hydraulic or mechanical force. Known for its strength, durability, and reliability, forged components find applications in various industries, including automotive, aerospace, defense, and construction. Traditionally, forging was a labor-intensive process that required skilled craftsmen to manually shape the metal into the desired form. However, with the advent of modern technologies, the forging industry has witnessed significant advancements, which have simplified and optimized the manufacturing process.2. Introduction of Advanced Materials:One key innovation lies in the utilization of advanced materials for forging applications. With the development of high-strength alloys, superalloys, and composite materials, manufacturers now have access to materials with enhanced characteristics, such as superior mechanical properties, heat resistance, and corrosion resistance. By utilizing these advanced materials, companies have been able to produce components that are not only lighter and more durable but also better suited for specific operational conditions.3. Computer-Aided Design and Manufacturing (CAD/CAM) Integration:Integration of computer-aided design and manufacturing (CAD/CAM) systems has been instrumental in streamlining the entire forging process. By digitizing the design, simulation, and manufacturing phases, engineers can now create intricate component geometries with enhanced precision and accuracy. CAD/CAM integration allows for the optimization of tooling and die designs, reducing material waste and production costs while improving overall product quality.4. Automation and Robotics:The introduction of automation and robotics in forging facilities has led to a significant boost in production efficiency and consistency. Intelligent robotic systems can now handle complex tasks previously performed by human operators, such as loading and unloading parts, transferring components between workstations, and performing quality inspections. This integration of automation not only improves productivity and reduces labor costs but also ensures a higher level of precision, repeatability, and safety throughout the manufacturing process.5. Simulation and Predictive Analysis:Simulations and predictive analysis tools are transforming the way manufacturers approach the forging process. Advanced software can simulate the behavior of metals under extreme heat and pressure, accurately predicting how they will deform, crack, or fail. By simulating different scenarios, engineers can optimize the process parameters, tooling designs, and material selection, reducing the time and costs associated with physical prototyping and testing. This technological advancement allows for faster development cycles, improved component quality, and increased overall efficiency.6. Additive Manufacturing in Forging:Additive manufacturing, often referred to as 3D printing, has also found its way into the realm of forging. Through the utilization of metal powders and advanced printing techniques, complex components can be fabricated layer by layer, eliminating the need for traditional forging processes. This disruptive technology offers increased design flexibility, reduced material waste, and shorter production times, enabling manufacturers to create intricate and lightweight components that were previously unattainable.7. Quality Assurance and Traceability:In addition to process improvements, modern forging techniques have also enhanced quality assurance and traceability. Manufacturers now employ advanced inspection technologies, such as non-destructive testing and optical measurement systems, to ensure that components meet the highest industry standards. Additionally, blockchain-based systems facilitate real-time traceability, providing customers with transparent information about the origin, production, and testing of forged components. These advancements instill confidence in the quality and reliability of the products while meeting the rigorous demands of various regulatory bodies.Conclusion:The evolution of the forging process, driven by the innovative technologies introduced by companies such as {}, has ushered in a new era of manufacturing excellence. From advanced materials and CAD/CAM integration to automation, simulation, and additive manufacturing, these advancements have significantly improved product quality, production efficiency, and customer satisfaction. The future of forging appears promising, with continued research and development propelling the industry towards greater innovation and success.
Ultimate Guide to Die Casting: Everything You Need to Know
Die Casting Company Expands Operations to Meet Growing Demand[Company Name] has recently announced the expansion of their die casting operations in response to an increasing demand for their products. The company, which has been a leading manufacturer of high-quality die-cast components for various industries, is now set to enhance their production capabilities to better serve their customers.With the expansion, [Company Name] will be able to offer a wider range of die casting services, including the production of complex and intricate components for automotive, aerospace, and industrial applications. This move comes as a strategic response to the growing demand for die-cast parts in these industries, and the company is poised to capitalize on this burgeoning market.“As a forward-thinking company, we are always looking for ways to improve our operations and better serve our customers,” said the CEO of [Company Name]. “The expansion of our die casting operations is a testament to our commitment to meeting the needs of our clients and providing them with the highest quality products.”The new facility will be equipped with state-of-the-art die casting machines and technology, allowing the company to produce components with superior precision and quality. Additionally, the expansion will also create job opportunities for local residents, further stimulating economic growth in the region.[Company Name] has established a strong reputation for delivering innovative and reliable die casting solutions, and the expansion of their operations further solidifies their position as a leader in the industry. Their team of experienced engineers and technicians work closely with clients to develop custom die casting solutions that meet their specific requirements.The company’s expertise and unwavering commitment to quality have earned them the trust of numerous clients across various industries. With the expansion of their operations, [Company Name] is well-positioned to further expand their client base and solidify their standing as a premier die casting manufacturer.In addition to the expansion of their die casting operations, [Company Name] has also been making efforts to incorporate sustainable and environmentally friendly practices into their manufacturing processes. They have invested in advanced technologies that minimize waste and energy consumption, demonstrating their dedication to sustainability.“We understand the importance of environmental responsibility, and we are continuously exploring ways to reduce our environmental impact,” the CEO added. “By incorporating sustainable practices into our operations, we are not only benefitting the environment, but also ensuring the long-term success of our business.”The expansion of [Company Name]’s die casting operations represents a significant milestone for the company, and a testament to their continued growth and success. With their unwavering dedication to quality, innovation, and sustainability, [Company Name] is poised to further strengthen their position as a leading die casting manufacturer in the industry.
Top Car Parts: Essential Components for Efficient Vehicle Performance
Title: Leading Automotive Supplier Car Parts Unveils Innovative Solutions for Better Vehicle PerformanceIntroduction:Car Parts is a renowned automotive supplier with a strong reputation for providing high-quality components to the global automotive industry. With a commitment to innovation and continuous improvement, Car Parts has announced its latest range of ground-breaking solutions designed to enhance vehicle performance and deliver an exceptional driving experience. In this news article, we will explore the company's new offerings and how they are set to revolutionize the automotive industry.Paragraph 1: Car Parts has introduced an array of cutting-edge products that aim to improve vehicle performance, safety, and efficiency. These state-of-the-art components have been meticulously designed and thoroughly tested to meet the demanding needs of the modern automotive industry. With a dedicated team of experts, Car Parts focuses on addressing critical challenges in the sector, such as reducing emissions, increasing fuel efficiency, and enhancing durability.Paragraph 2: One of the highlights of Car Parts' latest offerings is the revolutionary Engine Enhancement Module (EEM). This groundbreaking technology enables vehicles to achieve optimal engine performance while simultaneously reducing environmental impact. By seamlessly integrating with the vehicle's existing engine control unit, the EEM optimizes fuel injection, ignition timing, and air-fuel ratio, resulting in improved power, efficiency, and reduced emissions. Car Parts' EEM represents a significant milestone in the pursuit of sustainable transportation.Paragraph 3: In addition to the EEM, Car Parts recognizes the importance of safety in the automotive industry. The company is proud to introduce its Advanced Driver Assistance Systems (ADAS), designed to enhance vehicle safety and reduce the risk of accidents. Car Parts' ADAS utilizes state-of-the-art sensors and cutting-edge algorithms to enable features such as blind-spot detection, lane departure warnings, and adaptive cruise control. These intelligent systems work together harmoniously to provide drivers with an extra layer of protection, ensuring a safer driving experience for all.Paragraph 4: Car Parts' commitment to innovation doesn't stop at engines and safety. The company has also unveiled a range of lightweight materials and components that significantly contribute to improving overall vehicle efficiency. By employing advanced engineering techniques and utilizing materials such as carbon fiber, Car Parts' lightweight solutions reduce the weight of vehicles without compromising strength or safety. This results in improved fuel economy, reduced emissions, and enhanced agility.Paragraph 5: To meet the diverse needs of their global clientele, Car Parts maintains an extensive network of manufacturing facilities across several regions. These strategically located facilities enable Car Parts to efficiently meet customer demands while ensuring the highest standards of quality and reliability. With an unwavering commitment to customer satisfaction, the company also offers exceptional after-sales service, ensuring a seamless ownership experience for their clients worldwide.Conclusion:Car Parts' groundbreaking solutions have set a new benchmark in the automotive industry. With their focus on enhancing vehicle performance, safety, and environmental sustainability, the company is poised to drive the automotive industry forward. By consistently pushing the boundaries of innovation and delivering top-notch products and services, Car Parts continues to establish itself as a leading automotive supplier globally. As the industry embraces technological advancements, Car Parts remains at the forefront, revolutionizing the future of automotive excellence.