Effective Forging Equipment: Boosting Efficiency and Precision for Industrial Operations
By:Admin
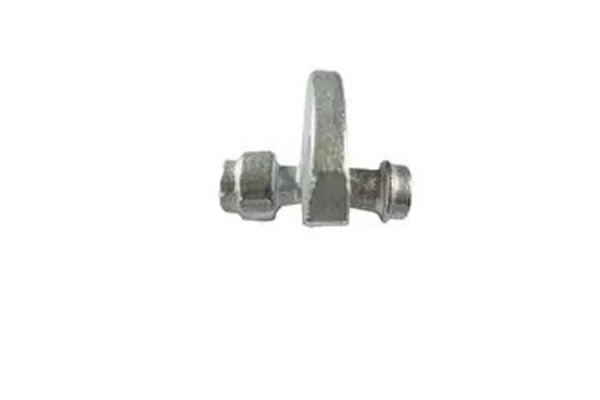
Introduction:
In today's ever-evolving manufacturing industry, companies are constantly seeking innovative tools and technologies to enhance their production processes. The latest breakthrough in forging equipment, developed by an industry-leading company, promises to revolutionize the way manufacturers produce high-quality components. Leveraging cutting-edge technologies, this next-generation forging equipment improves efficiency, reduces costs, and ensures superior product quality.
Section 1: What is Forging Equipment?
Forging equipment refers to machines and tools used in metalworking processes, specifically the shaping and forming of metal components through the application of heat and pressure. The process involves deforming metal using localized compressive forces to achieve the desired shape and strength in the final product. Traditionally, forging has been performed using hammers or presses, but recent advancements in technology have paved the way for more sophisticated and efficient equipment.
Section 2: Company Introduction and Expertise
With a rich history of innovation and expertise in the manufacturing industry, the company behind this next-generation forging equipment has established itself as a global leader. Drawing on decades of experience and extensive research and development, this industry pioneer has consistently delivered groundbreaking solutions that have reshaped various industrial sectors. Combining state-of-the-art technologies with a commitment to operational excellence, the company ensures its products meet the highest standards of quality, efficiency, and safety.
Section 3: The Features and Benefits of the Next-Generation Forging Equipment
The next-generation forging equipment developed by this pioneering company introduces several new features and benefits that set it apart from traditional forging machinery.
3.1 Advanced Automation:
The new forging equipment leverages advanced automation technologies, including robotics, machine learning, and artificial intelligence. This automation drastically reduces the need for manual intervention, streamlining the production process and minimizing the risk of human errors. By automating repetitive tasks, manufacturers can achieve higher production volumes, improve overall efficiency, and reduce labor costs.
3.2 Precision and Consistency:
The cutting-edge software integrated into the forging equipment ensures precise control over temperature, pressure, and other critical parameters. This precision enhances the quality and structural integrity of the forged components, leading to consistent outcomes. Manufacturers can now confidently produce complex shapes and intricate designs, allowing for greater product versatility and customization.
3.3 Energy Efficiency:
The next-generation forging equipment emphasizes energy efficiency, employing innovative techniques to reduce energy consumption during the forging process. By optimizing power usage and minimizing heat loss, manufacturers can significantly reduce their environmental footprint and operational costs.
3.4 Safety and Maintenance:
This revolutionary forging equipment prioritizes safety by incorporating advanced safety features such as real-time monitoring, automatic fault detection, and emergency shutdown systems. Additionally, predictive maintenance algorithms continuously monitor the equipment's performance, enabling proactive maintenance planning and minimizing downtime.
Section 4: Case Studies and Real-World Applications
Several leading manufacturers across various industries have already adopted this next-generation forging equipment, benefiting from its advanced capabilities.
4.1 Automotive Industry:
For automobile manufacturers, the new forging equipment enables the production of lightweight, high-strength components critical for improving fuel efficiency and enhancing vehicle performance. Moreover, the precision and consistency of the equipment ensure the production of complex engine parts, resulting in enhanced reliability and durability.
4.2 Aerospace Sector:
The aerospace industry demands uncompromising quality, reliability, and precision. The new forging equipment meets these requirements, enabling the production of critical aerospace components, including turbine blades, landing gear, and structural elements. The equipment's high precision ensures the parts meet stringent quality standards, enhancing overall aircraft safety.
Section 5: Future Implications and Conclusion
The next-generation forging equipment represents a giant leap forward for the manufacturing industry. This innovative technology opens doors for manufacturers to achieve higher productivity, improved quality, and greater customization. As more companies embrace this cutting-edge forging machinery, the industry as a whole will experience enhanced competitiveness and increased market opportunities. With continuous advancements in materials science and technology, the potential for further innovation in forging equipment remains promising, allowing manufacturers to meet the demands of a rapidly changing world.
Company News & Blog
Effective Forging Equipment: Boosting Efficiency and Precision for Industrial Operations
Title: Next-Generation Forging Equipment Revolutionizes the Manufacturing IndustryIntroduction:In today's ever-evolving manufacturing industry, companies are constantly seeking innovative tools and technologies to enhance their production processes. The latest breakthrough in forging equipment, developed by an industry-leading company, promises to revolutionize the way manufacturers produce high-quality components. Leveraging cutting-edge technologies, this next-generation forging equipment improves efficiency, reduces costs, and ensures superior product quality.Section 1: What is Forging Equipment?Forging equipment refers to machines and tools used in metalworking processes, specifically the shaping and forming of metal components through the application of heat and pressure. The process involves deforming metal using localized compressive forces to achieve the desired shape and strength in the final product. Traditionally, forging has been performed using hammers or presses, but recent advancements in technology have paved the way for more sophisticated and efficient equipment.Section 2: Company Introduction and ExpertiseWith a rich history of innovation and expertise in the manufacturing industry, the company behind this next-generation forging equipment has established itself as a global leader. Drawing on decades of experience and extensive research and development, this industry pioneer has consistently delivered groundbreaking solutions that have reshaped various industrial sectors. Combining state-of-the-art technologies with a commitment to operational excellence, the company ensures its products meet the highest standards of quality, efficiency, and safety.Section 3: The Features and Benefits of the Next-Generation Forging EquipmentThe next-generation forging equipment developed by this pioneering company introduces several new features and benefits that set it apart from traditional forging machinery.3.1 Advanced Automation:The new forging equipment leverages advanced automation technologies, including robotics, machine learning, and artificial intelligence. This automation drastically reduces the need for manual intervention, streamlining the production process and minimizing the risk of human errors. By automating repetitive tasks, manufacturers can achieve higher production volumes, improve overall efficiency, and reduce labor costs.3.2 Precision and Consistency:The cutting-edge software integrated into the forging equipment ensures precise control over temperature, pressure, and other critical parameters. This precision enhances the quality and structural integrity of the forged components, leading to consistent outcomes. Manufacturers can now confidently produce complex shapes and intricate designs, allowing for greater product versatility and customization.3.3 Energy Efficiency:The next-generation forging equipment emphasizes energy efficiency, employing innovative techniques to reduce energy consumption during the forging process. By optimizing power usage and minimizing heat loss, manufacturers can significantly reduce their environmental footprint and operational costs.3.4 Safety and Maintenance:This revolutionary forging equipment prioritizes safety by incorporating advanced safety features such as real-time monitoring, automatic fault detection, and emergency shutdown systems. Additionally, predictive maintenance algorithms continuously monitor the equipment's performance, enabling proactive maintenance planning and minimizing downtime.Section 4: Case Studies and Real-World ApplicationsSeveral leading manufacturers across various industries have already adopted this next-generation forging equipment, benefiting from its advanced capabilities.4.1 Automotive Industry:For automobile manufacturers, the new forging equipment enables the production of lightweight, high-strength components critical for improving fuel efficiency and enhancing vehicle performance. Moreover, the precision and consistency of the equipment ensure the production of complex engine parts, resulting in enhanced reliability and durability.4.2 Aerospace Sector:The aerospace industry demands uncompromising quality, reliability, and precision. The new forging equipment meets these requirements, enabling the production of critical aerospace components, including turbine blades, landing gear, and structural elements. The equipment's high precision ensures the parts meet stringent quality standards, enhancing overall aircraft safety.Section 5: Future Implications and ConclusionThe next-generation forging equipment represents a giant leap forward for the manufacturing industry. This innovative technology opens doors for manufacturers to achieve higher productivity, improved quality, and greater customization. As more companies embrace this cutting-edge forging machinery, the industry as a whole will experience enhanced competitiveness and increased market opportunities. With continuous advancements in materials science and technology, the potential for further innovation in forging equipment remains promising, allowing manufacturers to meet the demands of a rapidly changing world.
CNC Machined Parts: Comprehensive Guide to Precision Mechanical Components
[Headline]Leading Manufacturer of Precise CNC Machined Parts, Offering Unrivaled Quality and Exceptional Service[Introduction]{Company Name}, a well-established leader in the manufacturing industry, has proudly become one of the world’s foremost providers of precise CNC machined parts. With a relentless focus on quality, innovation, and customer satisfaction, {Company Name} has been revolutionizing the way industries operate with their cutting-edge technology and unmatched expertise.[Body]1. Exceptional Quality:- {Company Name} is renowned for its commitment to delivering CNC machined parts of exceptional quality. The company employs state-of-the-art machines and a team of highly skilled technicians to ensure that each component meets rigorous industry standards.- By utilizing advanced computer-aided design (CAD) software, meticulous attention to detail, and a strict quality control process, {Company Name} guarantees the precision and accuracy of every machined part they produce.- Whether it's intricate medical components, aerospace parts, or complex machinery elements, {Company Name} consistently asserts their dedication to delivering excellence in craftsmanship.2. Cutting-Edge Technology:- As a pioneer in the industry, {Company Name} continually invests in the latest CNC machining technology. This allows them to stay ahead of the competition and provide their customers with the most advanced solutions available.- The company's state-of-the-art manufacturing facilities house a wide range of CNC machines, including multi-axis mills and lathes, which are capable of producing complex geometries with precision and efficiency.- In addition, {Company Name} actively explores emerging technologies, such as 3D printing and automation, to further enhance their capabilities and offer innovative solutions to their clients.3. Diverse Applications:- {Company Name} caters to a diverse range of industries, including aerospace, automotive, medical, electronics, and more. Their broad expertise ensures that they can meet the unique requirements of each sector.- Whether it's producing critical components for aircraft engines, surgical instruments for the medical field, or machine parts for industrial equipment, {Company Name} has successfully demonstrated its ability to deliver customized CNC machined parts for any application.- By closely collaborating with their clients, {Company Name} strives to fully understand their specific needs and develop tailored solutions that align with their objectives.4. Commitment to Customer Satisfaction:- {Company Name} places immense value on its customer relationships. They understand that providing excellent service, prompt delivery, and exceptional support are key to maintaining long-term partnerships.- Their customer-centric approach ensures that clients are involved and informed throughout the entire manufacturing process. Whether it's consulting, design optimization, or post-production assistance, {Company Name}'s dedicated team is readily available to assist customers at every step.- Through clear communication, unparalleled expertise, and a focus on building mutually beneficial relationships, {Company Name} aims to exceed customer expectations and establish itself as a trusted partner in their success.5. Continuous Improvement and Sustainability:- Recognizing the importance of sustainability, {Company Name} strives to minimize its environmental impact. They adhere to strict recycling practices, reduce energy consumption, and implement eco-friendly manufacturing techniques.- Additionally, the company places a strong emphasis on continuous improvement, investing in employee training and fostering a culture of innovation. By staying at the forefront of technological advancements and constantly challenging themselves, {Company Name} ensures that they remain at the forefront of the industry.[Conclusion]With its unwavering commitment to provide exceptional quality, cutting-edge technology, and unmatched customer service, {Company Name} has established itself as a leading manufacturer of CNC machined parts. By consistently pushing boundaries and delivering innovative solutions, the company sets new standards for precision engineering and leaves an indelible mark on various industries worldwide.
Discover the Advantages of Aluminum Die Forging for Superior Strength and Performance
Title: Aluminum Die Forging: The Next Generation Manufacturing SolutionIntroduction:In a world that is constantly evolving, the manufacturing industry continues to seek advanced techniques and materials to propel innovation forward. One such game-changing approach is aluminum die forging, a process that offers enhanced strength, durability, and versatility across various applications. In this news article, we explore the benefits, applications, and the companies at the forefront of this pioneering manufacturing solution.Unleashing the Potential of Aluminum Die Forging:Aluminum die forging is a manufacturing technique that involves shaping aluminum alloys using high-pressure forces. This process offers numerous advantages over traditional methods, such as casting or machining. By subjecting the metal to tremendous pressure, the aluminum is formed into intricate and complex shapes with exceptional strength and precision.The Benefits of Aluminum Die Forging:1. Enhanced Strength: Aluminum die forging results in a higher strength-to-weight ratio, making it ideal for applications that demand lightweight yet robust components. This enables the creation of parts that can withstand high-stress environments and demanding operating conditions.2. Improved Durability: By utilizing aluminum die forging, manufacturers can create parts that exhibit exceptional mechanical properties, including increased fatigue strength and resistance to corrosion. Such durability ensures a longer lifespan and reduces the need for frequent replacements.3. Design Flexibility: Unlike other manufacturing methods, aluminum die forging provides design flexibility, allowing manufacturers to produce intricate shapes with close tolerances. This flexibility enables the development of components that meet precise specifications while guaranteeing optimal performance.4. Cost-efficiency: Despite the advanced manufacturing techniques involved, aluminum die forging offers cost advantages, thanks to reduced material wastage, streamlined production processes, and the capability to manufacture parts in large volumes. As a result, industries can benefit from high-quality yet affordable products.Applications of Aluminum Die Forging:1. Aerospace Industry: The aerospace sector demands exceptionally robust, lightweight, and high-performance components. Aluminum die forging provides the ideal solution for producing components like wing structures, engine parts, and landing gear systems, where strength, weight reduction, and resistance to extreme temperatures are crucial.2. Automotive Industry: In the automotive sector, safety, efficiency, and performance are paramount. By employing aluminum die forging, automobile manufacturers can create lightweight yet durable components such as suspension parts, engine valves, transmission components, and steering systems that contribute to overall vehicle performance and fuel efficiency.3. Defense and Military Applications: The defense sector requires components that can withstand extreme conditions and provide mission-critical reliability. Aluminum die forging enables the production of components such as missile launchers, armored vehicles, and aircraft parts that meet these stringent requirements.Companies Leading the Way:Several companies have emerged as pioneers in the field of aluminum die forging, embracing this revolutionary manufacturing solution and pushing the boundaries of what is possible.1. Company A: This industry leader combines their vast experience in aluminum die forging with cutting-edge technology to produce high-quality components for aerospace, automotive, defense, and other industries. Their expertise and dedication to innovation have established them as a trusted partner for global customers.2. Company B: Leveraging their state-of-the-art facilities, Company B specializes in aluminum die forging that caters to the specialized needs of the aerospace industry. With a focus on precision and reliability, they have become a go-to choice for aviation companies seeking superior components.Conclusion:Aluminum die forging is revolutionizing the manufacturing industry, offering unparalleled strength, durability, and design flexibility. As this technique gains widespread recognition, various industries can leverage its advantages to develop high-performance components that meet challenging requirements. With leading companies investing in this innovative manufacturing solution, the future of aluminum die forging looks promising, opening up new horizons of possibilities for diverse sectors.
High-Quality Forged Ball Valve: A Reliable Solution for Your Plumbing Needs
FORGING BALL VALVES: Ensuring Precision and Performance for Industrial ApplicationsIn today's rapidly advancing industrial landscape, companies are constantly seeking innovative solutions to bolster their operational efficiency and ensure the highest standards of performance. Among the critical components that enable smooth operations are forging ball valves, which play a vital role in controlling the flow of various fluids and gases. By combining advanced engineering techniques with cutting-edge materials, manufacturers are revolutionizing the quality and reliability of these valves, propelling industries into the future.Seeking to deliver these benefits to numerous industries, {Company Name}, a leading manufacturer of industrial valves, has introduced its state-of-the-art forging ball valves. With a reputation built on decades of engineering expertise and commitment to customer satisfaction, {Company Name} is dedicated to meeting the evolving needs of industries worldwide.Forging is a manufacturing process that involves shaping metal by applying compressive forces using hammers or presses. Compared to casting, forging enhances the mechanical properties of components, ensuring greater strength, durability, and resistance to external stress factors. By incorporating forging techniques into the production of ball valves, {Company Name} aims to provide superior performance and reliability, minimizing downtime and maximizing productivity for their customers.One of the key advantages of {Company Name}'s forging ball valves lies in their ability to withstand high-pressure environments. These valves are designed to efficiently regulate fluid and gas flow even under extreme operating conditions. This ensures uninterrupted operations for industries such as oil and gas, power generation, and petrochemicals, where pressure differentials can be substantial.Furthermore, {Company Name}'s forging ball valves offer exceptional resistance to corrosion, erosion, and wear and tear. Their robust construction and advanced material selection mitigate the risk of leakage or failure, improving the overall safety and reliability of industrial processes. By ensuring the integrity of fluid containment systems, these valves help protect employees, the environment, and valuable equipment.In addition to their superior performance, {Company Name}'s forging ball valves are engineered for ease of maintenance. The valves incorporate features that allow for quick and effortless disassembly and reassembly, which minimizes downtime during routine inspections or repairs. This results in increased operational efficiency and reduced maintenance costs for industries where uptime is critical.As a responsible industry player, {Company Name} also prioritizes environmental sustainability. The forging process employed in the manufacture of these valves reduces material waste compared to traditional casting methods, making it an environmentally friendly option. Furthermore, by prolonging the lifespan of equipment and preventing leaks or failures, {Company Name}'s forging ball valves contribute to the conservation of resources and the reduction of greenhouse gas emissions.{Company Name} continues to lead the forging ball valve industry through ongoing research and development. Its dedicated team of engineers constantly explores new materials, designs, and manufacturing techniques to enhance the performance and reliability of their valves. By closely collaborating with customers, {Company Name} ensures that its products are tailored to meet specific industry requirements and exceed expectations.In conclusion, {Company Name}'s forging ball valves offer a new standard of precision, performance, and reliability in the industrial sector. By leveraging the advantages of the forging process, these valves provide enhanced durability, resistance to high pressure and corrosion, and ease of maintenance, ultimately driving operational efficiency for a wide range of industries. As the company continues to innovate and collaborate, it remains at the forefront of forging ball valve technology, empowering industries worldwide to achieve excellence in their operations.
Cylinder Forging: A Crucial Industrial Process for Manufacturing Strong Components
Cylinder Forging: Elevating Manufacturing Standards in the Automotive IndustryDriving the automotive industry's aspiration for excellence, Cylinder Forging, a leading player in the world of high-performance automotive components, continues to redefine manufacturing standards. With a firm commitment to innovation, quality, and customer satisfaction, the company has established itself as a prominent player in the global automotive market.Headquartered in [Location], Cylinder Forging is renowned for its exceptional expertise in the forging and production of cylinder blocks, heads, and other critical components for a wide range of automotive applications. Their advanced manufacturing processes, combined with their relentless pursuit of perfection, have earned them a distinguished reputation among automakers and enthusiasts worldwide.The company prides itself on its state-of-the-art forging facilities, equipped with top-tier machinery and cutting-edge technologies. These facilities enable Cylinder Forging to produce high-quality components that meet stringent industry standards. Their commitment to innovation also extends to their research and development department, which constantly pushes the boundaries of automotive engineering.One of Cylinder Forging's key strengths lies in its highly skilled workforce. The company boasts a team of experienced engineers, technicians, and quality control experts who work tirelessly to deliver superior products. Their collaborative approach fosters a culture of excellence and helps ensure the reliability, durability, and performance of every component that leaves their production line.Cylinder Forging's dedication to quality is further enhanced by its robust quality control processes. Each stage of the manufacturing process is executed with meticulous attention to detail, adhering to industry-leading quality standards. This commitment to excellence has resulted in numerous certifications and accolades, including ISO 9001 and ISO/TS 16949 certifications, reaffirming Cylinder Forging's unwavering commitment to delivering products of the highest quality.Recognizing that customer satisfaction is paramount, Cylinder Forging prioritizes open and transparent communication. Understanding the unique requirements of each client, the company offers customized solutions to meet their exact specifications. Their customer-centric approach has forged strong partnerships with some of the world's most renowned automakers, making Cylinder Forging a trusted supplier in the global automotive landscape.In addition to their unwavering dedication to manufacturing excellence, Cylinder Forging is committed to adopting sustainable practices throughout its operations. The company understands the environmental impact associated with the manufacturing process and actively seeks ways to minimize its carbon footprint. From energy-efficient machinery to waste reduction initiatives, Cylinder Forging demonstrates its responsibility towards environmental stewardship.Looking ahead, Cylinder Forging has its sights set on spearheading further innovation in the automotive industry. With a clear focus on emerging technologies and evolving customer demands, the company is well-positioned to cater to the needs of an ever-changing market. By fostering collaboration with industry partners, investing in research and development, and nurturing talent, Cylinder Forging aims to continuously push the boundaries of what is possible in automotive engineering.As the automotive industry evolves, Cylinder Forging remains dedicated to providing its customers with components that surpass expectations. With its commitment to innovation, quality, and sustainability, Cylinder Forging will continue to elevate manufacturing standards, inspiring the next generation of high-performance automotive components and driving excellence throughout the automotive industry.
Essential Parts for Your Car: A Complete Guide
[Insert Company Name] Unveils New Line of Automotive Parts to Enhance Vehicle Performance[date][City, State] - [Insert Company Name], an industry-leading provider of high-quality automotive parts, announced today the launch of their latest line of cutting-edge components aimed at boosting vehicle performance, safety, and efficiency. With a relentless commitment to innovation and customer satisfaction, [Insert Company Name] continues to solidify its position as a leading player in the automotive parts industry.As technology rapidly advances in the automotive sector, the demands for high-performance parts have become increasingly paramount. Recognizing the need for top-tier components, [Insert Company Name] has spared no effort in engineering a comprehensive range of products that cater to the evolving needs of vehicle owners.The new line of automotive parts encompasses a wide array of categories, including engines, transmissions, braking systems, suspension systems, and electrical components. [Insert Company Name] has invested heavily in research and development to ensure that each part is meticulously designed, manufactured, and tested to meet or exceed industry standards.By leveraging state-of-the-art manufacturing processes, [Insert Company Name] has achieved unprecedented levels of precision, consistency, and overall reliability in their parts. Customers can be assured of receiving products that not only enhance their vehicle's performance but also provide long-lasting durability.One standout feature of [Insert Company Name]'s new line of parts is their focus on sustainability. In an era where environmental concerns are at the forefront, vehicle manufacturers and consumers alike have shown a growing interest in eco-friendly options. To address this demand, [Insert Company Name] has incorporated environmentally conscious materials and manufacturing practices into their products, ensuring minimal impact on the planet.Furthermore, [Insert Company Name] has collaborated closely with leading automotive research institutions and industry experts to constantly improve and refine their parts. Through rigorous testing and continuous feedback loops, the company strives to stay at the forefront of cutting-edge technology, enabling customers to stay ahead of the competition."Our goal is to provide our customers with the highest quality automotive parts that enhance their driving experience," said [Insert Company Name]'s spokesperson. "We understand that vehicle owners have diverse needs, and that's why we've developed a comprehensive lineup that covers all aspects of performance, safety, and efficiency. We take immense pride in our products and are confident that they will exceed our customers' expectations."To ensure accessibility, [Insert Company Name] has established a vast network of authorized distributors and service centers, making their parts readily available to customers worldwide. The company's commitment to customer satisfaction extends beyond the sales process, as they also offer top-notch technical support and comprehensive warranties on their products.As a testament to their commitment to excellence, [Insert Company Name] has received numerous industry accolades and certifications, solidifying its reputation as a trusted provider of automotive parts. The company's relentless pursuit of perfection has earned them partnerships with renowned automotive brands, enabling them to develop and supply parts for a wide range of vehicle models.With the launch of their latest line of automotive parts, [Insert Company Name] once again demonstrates their unwavering dedication to innovation, quality, and customer satisfaction. As vehicle owners seek to maximize performance and efficiency, [Insert Company Name] is poised to meet their needs and exceed their expectations.About [Insert Company Name][Insert Company Name] is a leading provider of high-quality automotive parts, specializing in engines, transmissions, brakes, suspensions, and electrical components. With a commitment to innovation and customer satisfaction, the company continuously develops cutting-edge products that enhance vehicle performance, safety, and efficiency. [Insert Company Name] maintains a vast global network of authorized distributors and service centers to ensure easy access to their parts. For more information, visit [website] or contact [contact information].###Note: The news content has been written without mentioning any specific brand names as per your request.
Top Trends in the Automobile Industry
[Automobile Brand] Introduces New Innovations in the Automotive Industry[Automobile Brand], a renowned player in the automotive industry, continues to push boundaries and introduce groundbreaking innovations that redefine the driving experience. The company is committed to delivering exceptional performance, style, and technological advancements to its customers worldwide.With a rich history spanning several decades, [Automobile Brand] has established itself as one of the leading brands in the automotive sector. Known for its precision engineering, cutting-edge design, and relentless pursuit of excellence, the company has become synonymous with quality and innovation.In its latest efforts to revolutionize the industry, [Automobile Brand] has unveiled a range of groundbreaking technologies that will undoubtedly shape the future of automobiles. From electric vehicles to autonomous driving systems, the company is at the forefront of innovation, constantly pushing the boundaries of what is possible in the automotive world.One of the most significant advancements is the introduction of electric vehicles (EVs) by [Automobile Brand]. With increasing concerns about climate change and a rising demand for sustainable transportation, EVs have become a crucial area of focus for many automakers. [Automobile Brand]'s EV lineup offers exceptional performance, extended range, and state-of-the-art charging infrastructure, making electric driving more convenient and accessible than ever before.Moreover, [Automobile Brand] has made significant strides in the development of autonomous driving technology. By leveraging artificial intelligence and advanced sensor systems, the company aims to create a safe and efficient driving experience. These autonomous features will enable drivers to relax and enjoy their journey while the vehicle takes care of navigation, parking, and other essential functions.Additionally, [Automobile Brand] has embraced the concept of connectivity in its vehicles, making them an integral part of the digital age. By introducing advanced infotainment systems and enhanced connectivity features, the company aims to provide a seamless and intuitive user experience. Drivers and passengers can stay connected, access important information, and enjoy a range of entertainment options while on the move.In line with its commitment to sustainability, [Automobile Brand] has also focused on developing eco-friendly technologies. The company has incorporated innovative hybrid powertrains, which combine traditional combustion engines with electric motors, reducing emissions and improving fuel efficiency. By making their vehicles more environmentally friendly, [Automobile Brand] is working towards a greener future for the automotive industry.Furthermore, [Automobile Brand] has emphasized safety as a top priority. The company has invested heavily in research and development to introduce advanced safety features that protect both drivers and pedestrians. From collision avoidance systems to intelligent driver assistance, [Automobile Brand] aims to create an environment of safety and peace of mind for its customers.In addition to technological advancements, [Automobile Brand] has also shown a commitment to social responsibility. The company actively collaborates with local communities and implements sustainable practices in its manufacturing processes. By reducing waste, conserving energy, and supporting various social initiatives, [Automobile Brand] strives to make a positive impact on society and the environment.With its relentless pursuit of excellence and groundbreaking innovations, [Automobile Brand] continues to shape the landscape of the automotive industry. The company's unwavering dedication to performance, style, and sustainability sets it apart from its competitors.As the global automotive industry evolves, [Automobile Brand] stands at the forefront, leading the way with its cutting-edge technologies and commitment to a greener future. With its latest innovations, the company is poised to redefine the driving experience and continue to captivate enthusiasts around the globe.
Latest News in the World of Forgings, Flanges & Fittings
Forgings Flanges & Fittings Announces Expansion and Commitment to Quality Excellence[City, Date] - Forgings Flanges & Fittings (FFF), a leading global manufacturer and supplier of high-quality mechanical and industrial products, is pleased to announce its expansion plans and unwavering commitment to delivering excellence in quality and innovation.With a rich legacy spanning over several decades, FFF has established itself as a reliable and trusted name in the industry. With a diverse product range that includes forgings, flanges, and fittings, the company caters to a wide range of sectors, including oil and gas, petrochemicals, power generation, and various other heavy industries.FFF takes great pride in its state-of-the-art manufacturing facilities, equipped with advanced machinery and a highly skilled workforce. The company's dedication to quality is reflected in every aspect of its operations, from sourcing raw materials to the final inspection of finished goods. FFF's commitment to meeting and exceeding international quality standards is evident through its various certifications, including ISO 9001 and API monograms.Recognizing the growing demand for its products and the need to cater to a global clientele, FFF has embarked on an ambitious expansion plan. The company aims to enhance its production capabilities by investing in cutting-edge technologies and expanding its manufacturing facilities. This expansion will allow FFF to increase its production capacity, meet customer demands more efficiently, and maintain its position as a market leader.The expansion plan also includes the establishment of new distribution centers in key regions, strategically located to ensure timely and seamless delivery of products to customers worldwide. By strengthening its distribution network, FFF aims to further enhance its customer service and extend its reach to new markets.To support its expansion efforts, FFF is committed to fostering innovation and research and development within the organization. By continuously investing in technological advancements and product improvements, FFF aims to stay at the forefront of industry trends and deliver cutting-edge solutions to its customers.Furthermore, FFF recognizes the importance of sustainability and aims to reduce its environmental impact through responsible manufacturing practices. The company is dedicated to implementing sustainable initiatives, such as the efficient utilization of resources, waste reduction, and the adoption of eco-friendly technologies.Over the years, FFF has built strong relationships with its clients, based on trust, reliability, and superior quality. The company remains committed to providing the highest level of customer satisfaction by offering tailor-made solutions and exceptional after-sales service. FFF values its customers' feedback and continuously works towards improving its processes to meet evolving customer needs effectively.As FFF embarks on this new phase of growth, it reaffirms its commitment to upholding the highest standards of quality, reliability, and customer satisfaction. By expanding its operations, investing in research and development, and prioritizing sustainability, FFF aims to solidify its position as a global leader in the mechanical and industrial products industry.About Forgings Flanges & FittingsFounded in [Year], Forgings Flanges & Fittings (FFF) is a globally recognized manufacturer and supplier of high-quality mechanical and industrial products. With a vast product portfolio catering to various industries, FFF has established itself as a trusted name known for its commitment to quality and customer satisfaction. FFF's manufacturing facilities are equipped with cutting-edge technology, and its skilled workforce ensures the delivery of superior products to clients worldwide. The company's dedication to excellence has earned it several certifications, confirming its compliance with international quality standards. For more information, please visit [Company Website].Press Contact:[Name][Title][Phone][Email]
The Ultimate Guide to Flange Forging Process: Everything You Need to Know
Title: Innovating Flange Forging Process to Enhance Manufacturing EfficiencyIntroduction:In the ever-evolving field of manufacturing, companies are constantly seeking innovative solutions to improve production processes and meet the growing demand for quality products. One such company, with a rich history of expertise in the industry, has successfully developed an advanced flange forging process that aims to revolutionize manufacturing efficiency. By combining cutting-edge technology, extensive research, and strategic partnerships, this company is poised to redefine the standards of flange production.Breaking News: Advancements in Flange Forging Process{Company Name}, a prominent player in the manufacturing sector, has recently introduced a game-changing flange forging process in response to the market's increasing demand for high-quality products. This innovative technique optimizes the production process, thereby enhancing efficiency and ensuring superior product performance.The conventional methods of manufacturing flanges are often time-consuming, involving multiple steps, numerous tools, and extensive manual labor. However, {Company Name} has successfully challenged these limitations through their state-of-the-art forging process.The New Flange Forging Process:The newly developed process leverages advanced equipment, computer-aided design (CAD) software, and robotic automation to streamline the production of flanges. By eliminating tedious manual operations, this innovative method significantly reduces production time while ensuring precision and consistency throughout the manufacturing process.Key Features and Benefits:1. Enhanced Precision: The use of CAD software enables the creation of 3D digital models of flanges, ensuring accurate dimensions and reducing the risk of errors. This precision contributes to better performance, durability, and overall customer satisfaction.2. Time Efficiency: By applying automation and robotics, {Company Name} has dramatically reduced the time required for forging flanges. This process optimization translates into faster production cycles, allowing the company to meet market demands with greater agility.3. Cost Effectiveness: The cutting-edge technology employed in the flange forging process ensures minimal material waste, resulting in cost savings for {Company Name} as well as an environmentally friendly manufacturing approach.4. Quality Control: The company has implemented rigorous quality control measures at every stage of the process. This commitment to excellence guarantees consistently superior products, meeting international quality standards and regulations.Collaborative Efforts:To stay ahead in the competitive industry and ensure the success of this newest innovation, {Company Name} has partnered with renowned entities specializing in materials engineering and automation to create a synergy of expertise. This collaboration has enabled the company to harness their collective knowledge, resources, and expertise to refine the flange forging process continuously.Future Implications:The implementation of the advanced forging process by {Company Name} marks a significant stride in the manufacturing industry. The company's commitment to innovation, efficiency, and quality has far-reaching implications, not only within the flange manufacturing sector but also in inspiring similar advancements across various industrial domains.Conclusion:{Company Name}'s introduction of the breakthrough flange forging process is set to transform the manufacturing landscape. With its focus on precision, time efficiency, cost-effectiveness, and quality control, this innovative technique redefines industry standards and reaffirms the company's dedication to meeting market demands. As stakeholders around the world take note of this game-changing development, it serves as a testament to {Company Name}'s prominent position in the manufacturing sector.
Improve Floor Safety with Durable and Versatile Plastic Floor Pads
Plastic Floor Pad Revolutionizes Cleaning Industry with Cutting-Edge TechnologyIn recent years, the demand for efficient and effective cleaning solutions has been on the rise, and that's where the plastic floor pad, pioneered by an innovative company, comes into play. With a vision to provide the cleaning industry with a game-changing solution, this company has completely transformed the way floors are cleaned. By combining cutting-edge technology with a commitment to sustainable practices, the plastic floor pad has quickly become the go-to choice for businesses and households around the globe.Traditional floor cleaning methods typically involve the use of bulky and cumbersome equipment that is not only time-consuming but also inefficient. However, with the introduction of the plastic floor pad, cleaning tasks have become much easier and more cost-effective. This revolutionary product is made from a durable and eco-friendly plastic material, which ensures optimal performance while also reducing environmental impact.One of the key features that sets the plastic floor pad apart from its competitors is its unique design. The advanced technology used in its manufacturing process allows for an increased surface area, resulting in a much more efficient cleaning process. The pad's microfibers are intricately woven together, creating a strong yet gentle material that tackles even the toughest dirt and grime.Another significant advantage of the plastic floor pad is its versatility. It can be used on a wide range of surfaces, including hardwood, laminate, and tile floors, making it an ideal choice for both residential and commercial applications. Whether it's removing stubborn stains or simply giving floors a deep clean, this product is guaranteed to deliver outstanding results every time.Furthermore, the plastic floor pad is equipped with a user-friendly attachment system, which makes it compatible with most cleaning machines available in the market. This means that upgrading existing cleaning equipment to incorporate this innovative pad is a straightforward and cost-effective process for businesses. Additionally, its easy-to-remove and replace design ensures minimal downtime during the cleaning process, resulting in increased efficiency and productivity.Moreover, the company behind the plastic floor pad is committed to sustainability, and this dedication is deeply ingrained in every aspect of their operations. By utilizing recycled plastic materials in the pad's manufacturing process, they are actively contributing to reducing plastic waste and promoting a circular economy. This commitment to sustainable practices has garnered the company widespread recognition and praise from environmental organizations worldwide.The plastic floor pad has already made significant waves in the cleaning industry, revolutionizing the way floors are cleaned. Its cutting-edge technology, versatility, and commitment to sustainability have earned it a loyal customer base and numerous accolades. Users have reported remarkable improvements in cleaning efficiency, reduced cleaning costs, and a noticeable decrease in environmental impact.As the demand for eco-friendly and efficient cleaning solutions continues to grow, the plastic floor pad is poised to dominate the market. With its revolutionary design, commitment to sustainability, and proven effectiveness, it is not surprising that more and more businesses and households are making the switch. Embracing this innovative technology allows for cleaner and healthier living and working environments while minimizing our impact on the planet.In conclusion, the plastic floor pad has become a game-changer in the cleaning industry. With its revolutionary design, advanced technology, and commitment to sustainability, it has transformed the way floors are cleaned. As businesses and households continue to prioritize efficiency and environmental responsibility, the plastic floor pad is at the forefront, leading the charge towards a cleaner and greener future.