High-quality brass forging for industrial applications
By:Admin
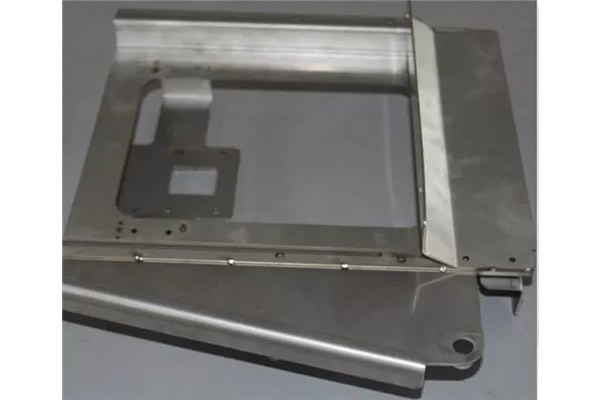
Established in {}, {} has built a strong reputation for delivering top-notch brass forging solutions to its clients worldwide. The company's state-of-the-art facilities are equipped with advanced forging equipment and technologies, allowing them to meet the most demanding requirements of their customers. Their team of highly skilled engineers and technicians has the expertise to design and produce intricate brass forged components with precision and efficiency.
One of the key advantages of brass forging is its ability to produce parts with excellent mechanical properties. The process enhances the strength, durability, and impact resistance of the brass, making it ideal for applications that require high performance and reliability. With its superior corrosion resistance and electrical conductivity, brass forged products from {} are widely used in critical environments where safety and reliability are paramount.
In addition to its functional properties, brass forging also offers aesthetic benefits. The process allows for intricate designs and shapes to be achieved, giving the finished products a visually appealing appearance. This makes brass forging a popular choice for decorative and architectural applications, where the visual appeal is as important as the performance.
Furthermore, {} recognizes the importance of quality and precision in brass forging. The company adheres to strict quality control measures at every stage of the manufacturing process to ensure that the finished products meet the highest industry standards. From material selection to final inspection, every step is meticulously monitored and tested to guarantee the quality and reliability of the brass forged components.
Another notable aspect of {}'s brass forging capabilities is its ability to offer custom solutions. The company works closely with its clients to understand their specific requirements and provide tailored forging solutions that meet their unique needs. Whether it's a prototype, a small batch, or a large-scale production, {} has the flexibility and expertise to deliver cost-effective and high-quality brass forged products on time and within budget.
With a strong commitment to innovation and continuous improvement, {} stays at the forefront of brass forging technology. The company invests in research and development to explore new techniques and materials, aiming to further enhance the performance and efficiency of its forging processes. This dedication to innovation and advancement ensures that {} remains a trusted partner for its clients, offering cutting-edge solutions that meet the evolving demands of the industry.
As the global demand for brass forged products continues to grow, {} is well-positioned to meet the needs of its customers. With its extensive experience, advanced capabilities, and unwavering dedication to quality, the company is poised to remain a leader in the brass forging industry for years to come. Whether it's for industrial, commercial, or decorative applications, {} is the go-to source for high-quality, precision-crafted brass forged components.
Company News & Blog
Streamlined Guide to Gravity Die Casting: Everything You Need to Know
Gravity Die Casting: Efficient and Precise Manufacturing TechnologyIn the world of manufacturing and production, efficiency and precision are the key factors that contribute to the success of any company. One such technology that has revolutionized the industry is gravity die casting - a method employed for manufacturing high-quality metal components with exceptional dimensional accuracy. Today, we will explore the gravity die casting process and its impact on the manufacturing sector, focusing on the remarkable achievements of a leading company {}.Gravity die casting, also known as permanent mold casting, is a reliable and cost-effective method to produce complex metal components with consistent quality. The process involves pouring molten metal into a metallic mold, which is later cooled and solidified to form the desired shape. Unlike other casting techniques, gravity die casting utilizes the force of gravity to fill the mold, resulting in reduced turbulence and better control over the casting process. This ensures improved surface finish, dimensional accuracy, and enhanced mechanical properties of the end product.Established in {}, {} has emerged as a pioneer in gravity die casting technology. With a stellar reputation built on years of experience and innovation, the company has successfully catered to the diverse needs of industries such as automotive, aerospace, defense, and consumer goods. Their commitment to quality and continuous improvement has propelled them to the forefront of the gravity die casting industry.Taking advantage of advanced machinery and state-of-the-art facilities, {} offers a comprehensive range of gravity die casting services. Their team of highly skilled engineers and technicians meticulously design and manufacture the molds required for the casting process. This ensures that each component produced adheres to the strictest specifications and quality standards. Furthermore, {} boasts an extensive material selection, allowing customers to choose from various alloys, including aluminum, zinc, and brass.The benefits of gravity die casting extend beyond the impeccable quality of the components. Its cost-efficiency, by reducing material waste and minimizing machining requirements, makes it an attractive choice for manufacturers. Additionally, the process is highly scalable, enabling {} to meet both low and high volume production demands without compromising on quality or lead times. Their dedication to delivering on-time and within budget has earned them the trust of numerous renowned clients.While gravity die casting is primarily associated with metal components, {} has pushed the boundaries of this manufacturing process. Their continuous investment in research and development has allowed them to expand their capabilities to include innovative applications such as gravity die casting of ceramics and composites. This pioneering approach has opened new doors in various industries and positioned {} as a leading provider of cutting-edge casting solutions.However, {}'s achievements are not limited to technological prowess alone. As a socially responsible company, they prioritize sustainability and environmental conservation. By implementing eco-friendly practices such as recycling and waste reduction, the company minimizes its carbon footprint and contributes to a greener future. This commitment to sustainable manufacturing has garnered {} recognition and accolades from industry peers and regulatory bodies alike.In conclusion, gravity die casting has revolutionized the manufacturing sector by offering efficient and precise production of high-quality metal components. With {} at the forefront of this technology, companies across various industries benefit from their exceptional expertise and commitment to excellence. As they continue to push boundaries and explore new frontiers in casting, {} establishes itself as an unrivaled leader in the field.
Understanding the Process of Cold Die Forging: Benefits and Applications
Cold Die Forging Process: A Precision Technique for Manufacturing{Company Name} is a leading manufacturer in the forging industry, specializing in cold die forging processes. With years of expertise and cutting-edge technology, we have been at the forefront of providing precision-engineered metal components to various industries, including automotive, aerospace, and construction.Cold die forging is a highly precise and efficient manufacturing process that allows for the production of complex and high-strength metal components. Unlike hot forging, which involves heating the metal to a high temperature, cold die forging involves shaping the metal at or near room temperature. This results in superior mechanical properties and a finer surface finish, making it an ideal technique for producing components that require tight tolerances and exceptional strength.The cold die forging process begins with the selection of high-quality raw materials, typically steel or aluminum alloys. These materials are then heated to a specific temperature and shaped using precision dies and punches. The force applied during the forging process results in the seamless formation of the desired component, with minimal material waste and a high degree of dimensional accuracy.At {Company Name}, we have invested in state-of-the-art forging equipment and automation technology to ensure the consistency and precision of our cold die forging processes. Our skilled engineers and technicians work closely with our clients to understand their unique requirements and develop tailored forging solutions that meet their exact specifications.One of the key advantages of cold die forging is its ability to produce components with superior mechanical properties. The process results in a refined grain structure and enhanced material strength, making the forged components resistant to fatigue, impact, and wear. This makes cold die forged components ideal for demanding applications in industries such as automotive, where safety and reliability are paramount.Furthermore, cold die forging allows for the production of complex and intricately shaped components with exceptional dimensional accuracy. This level of precision is essential for industries such as aerospace, where even the smallest deviation from the design specifications can compromise the performance and safety of the final product.In addition to its mechanical properties and dimensional accuracy, cold die forging also offers cost savings and production efficiencies. The high-speed production rates and minimal material waste associated with the process result in lower production costs and shorter lead times, providing our clients with a competitive edge in their respective markets.{Company Name} has a proven track record of delivering high-quality, precision-engineered components through our cold die forging processes. Our relentless commitment to quality and innovation has earned us the trust of leading companies in the automotive, aerospace, and construction industries, and we continue to push the boundaries of what is possible in the forging industry.As we look to the future, we remain dedicated to investing in research and development to further enhance our cold die forging capabilities. By staying at the forefront of technological advancements and industry trends, we are confident in our ability to continue providing our clients with the most advanced and reliable forging solutions.In conclusion, cold die forging is a precision manufacturing process that offers numerous advantages, including superior mechanical properties, dimensional accuracy, and cost savings. {Company Name} is proud to be a leader in this field, providing our clients with high-quality, precision-engineered components that meet the most demanding requirements. With our commitment to excellence and innovation, we are well-positioned to continue driving the advancement of cold die forging and delivering superior forging solutions to our clients worldwide.
How Casting Machinery is Revolutionizing the Industry
[Remove Brand Name] Introduces Cutting-Edge Casting Machinery for Enhanced Production Efficiency[date], [Location] - [Remove Brand Name], a global leader in manufacturing innovative industrial machinery, has recently introduced its latest line of cutting-edge casting machinery to meet the growing demand for enhanced production efficiency in various sectors. The state-of-the-art equipment combines advanced technology and precision engineering to streamline casting processes and enable companies to optimize their manufacturing capabilities.With a rich history of over [X] years in the industry, [Remove Brand Name] has consistently delivered high-quality machinery solutions to its clients across the globe. The company's extensive research and development efforts have resulted in the creation of the newest generation of casting machinery, which promises to revolutionize the way industries produce cast metal components.The casting machinery developed by [Remove Brand Name] is designed to cater to the diverse needs of industries such as automotive, aerospace, construction, and more. By leveraging advanced automation and intelligent control systems, this machinery offers unparalleled precision, speed, and efficiency in the casting process.One of the key features of [Remove Brand Name]'s casting machinery is its ability to optimize the allocation of resources, resulting in significant cost savings. The machinery is equipped with cutting-edge sensors and monitoring systems, allowing for real-time data collection and analysis. This data-driven approach empowers manufacturers to make informed decisions, identify bottlenecks, and streamline production processes for maximum efficiency.Furthermore, the state-of-the-art machinery boasts a user-friendly interface and intuitive controls, ensuring a seamless integration into existing production setups. The customizable nature of the machinery enables companies to adapt it to their specific requirements and achieve consistent and high-quality output.In addition to its advanced features, the casting machinery also emphasizes safety measures. [Remove Brand Name]'s commitment to worker safety is reflected in the machinery's design, which incorporates multiple safety mechanisms to minimize risks during operation. By adhering to industry standards and guidelines, [Remove Brand Name] ensures that its machinery provides a safe working environment for operators."Introducing our latest line of casting machinery is a significant milestone for [Remove Brand Name]," said [Spokesperson's Name], the spokesperson for [Remove Brand Name]. "We believe that this cutting-edge technology will enable our clients to achieve unprecedented levels of productivity and efficiency. Our aim is to empower industries to meet their production targets while maintaining superior quality standards."The launch of the new casting machinery aligns with [Remove Brand Name]'s vision of driving innovation in the industrial machinery sector. By constantly pushing boundaries and exploring new possibilities, the company remains committed to providing its customers with state-of-the-art solutions that enhance their ability to compete in the global market.To ensure efficient deployment of the machinery, [Remove Brand Name] offers comprehensive after-sales service and support to its customers. Through a global network of service centers and highly trained engineers, the company guarantees prompt assistance and swift resolution of any technical issues that may arise.As industries across the globe strive to optimize their manufacturing processes, [Remove Brand Name]'s cutting-edge casting machinery presents a compelling solution. By investing in this advanced equipment, companies can achieve higher production efficiency, reduce costs, and deliver superior products to their customers.About [Remove Brand Name]:[Remove Brand Name] is a renowned global manufacturer of industrial machinery, with a focus on innovation and customer satisfaction. With a wide range of products catering to diverse industries, the company delivers cutting-edge solutions that empower businesses to thrive in today's competitive market.For further information, visit [website] or contact:[Company Name][Contact Person][Position][Email][Phone Number]
Top Car Parts: Essential Components for Efficient Vehicle Performance
Title: Leading Automotive Supplier Car Parts Unveils Innovative Solutions for Better Vehicle PerformanceIntroduction:Car Parts is a renowned automotive supplier with a strong reputation for providing high-quality components to the global automotive industry. With a commitment to innovation and continuous improvement, Car Parts has announced its latest range of ground-breaking solutions designed to enhance vehicle performance and deliver an exceptional driving experience. In this news article, we will explore the company's new offerings and how they are set to revolutionize the automotive industry.Paragraph 1: Car Parts has introduced an array of cutting-edge products that aim to improve vehicle performance, safety, and efficiency. These state-of-the-art components have been meticulously designed and thoroughly tested to meet the demanding needs of the modern automotive industry. With a dedicated team of experts, Car Parts focuses on addressing critical challenges in the sector, such as reducing emissions, increasing fuel efficiency, and enhancing durability.Paragraph 2: One of the highlights of Car Parts' latest offerings is the revolutionary Engine Enhancement Module (EEM). This groundbreaking technology enables vehicles to achieve optimal engine performance while simultaneously reducing environmental impact. By seamlessly integrating with the vehicle's existing engine control unit, the EEM optimizes fuel injection, ignition timing, and air-fuel ratio, resulting in improved power, efficiency, and reduced emissions. Car Parts' EEM represents a significant milestone in the pursuit of sustainable transportation.Paragraph 3: In addition to the EEM, Car Parts recognizes the importance of safety in the automotive industry. The company is proud to introduce its Advanced Driver Assistance Systems (ADAS), designed to enhance vehicle safety and reduce the risk of accidents. Car Parts' ADAS utilizes state-of-the-art sensors and cutting-edge algorithms to enable features such as blind-spot detection, lane departure warnings, and adaptive cruise control. These intelligent systems work together harmoniously to provide drivers with an extra layer of protection, ensuring a safer driving experience for all.Paragraph 4: Car Parts' commitment to innovation doesn't stop at engines and safety. The company has also unveiled a range of lightweight materials and components that significantly contribute to improving overall vehicle efficiency. By employing advanced engineering techniques and utilizing materials such as carbon fiber, Car Parts' lightweight solutions reduce the weight of vehicles without compromising strength or safety. This results in improved fuel economy, reduced emissions, and enhanced agility.Paragraph 5: To meet the diverse needs of their global clientele, Car Parts maintains an extensive network of manufacturing facilities across several regions. These strategically located facilities enable Car Parts to efficiently meet customer demands while ensuring the highest standards of quality and reliability. With an unwavering commitment to customer satisfaction, the company also offers exceptional after-sales service, ensuring a seamless ownership experience for their clients worldwide.Conclusion:Car Parts' groundbreaking solutions have set a new benchmark in the automotive industry. With their focus on enhancing vehicle performance, safety, and environmental sustainability, the company is poised to drive the automotive industry forward. By consistently pushing the boundaries of innovation and delivering top-notch products and services, Car Parts continues to establish itself as a leading automotive supplier globally. As the industry embraces technological advancements, Car Parts remains at the forefront, revolutionizing the future of automotive excellence.
Discover the Latest Steel Sheet & Plate Innovations in the Market
Title: Steel Sheet & Plate Industry Fosters Growth Opportunities Amidst Challenging TimesIntroduction:In a dynamic global market, the steel industry has played a pivotal role in driving economic growth, infrastructural development, and technological progress across various sectors. One such company spearheading this growth is renowned for its exceptional quality steel sheet and plate manufacturing, while constantly setting new benchmarks for innovation and sustainability.1. Overview of the Steel Sheet & Plate Industry:The steel sheet and plate industry has witnessed remarkable growth over the years, becoming an integral part of numerous sectors such as construction, automotive, aerospace, and manufacturing. Steel sheets and plates, made from carbon, alloy, or stainless steel, are essential materials with diverse applications, ranging from structural frameworks, machinery parts, to decorative purposes.2. Environmental Commitment and Sustainability:In line with global sustainability goals, the steel sheet and plate manufacturer recognizes the importance of environmentally conscious practices. By implementing advanced technologies, the company has significantly reduced carbon emissions and optimized energy consumption in its manufacturing processes. Consistent efforts are being made to minimize waste and promote efficient recycling strategies.3. Technological Advancements and Innovation:To meet the ever-evolving demands of industries, the company remains at the forefront of research and development in steel production. Through cutting-edge technologies, such as advanced rolling mills and automated quality control systems, they ensure the highest standards of precision, durability, and product customization. This commitment to technological innovation has enabled them to stay ahead of market trends and further expand their product portfolio.4. Market Expansion and Growth:The steel sheet and plate manufacturer has experienced exponential growth in recent years, owing to its high-quality products, competitive pricing, and deep-rooted customer relationships. By collaborating with various industries, the company has successfully diversified its market presence, catering to both domestic and international clients.5. COVID-19 Impact and Resilience:Despite the unprecedented challenges posed by the COVID-19 pandemic, the steel sheet and plate industry has exhibited commendable resilience. The manufacturer swiftly adapted to the changing landscape by implementing stringent safety protocols, ensuring uninterrupted production, and meeting customer demand during these challenging times. With increasing infrastructure investments and recovery of global markets, the company remains optimistic about future growth prospects.6. Commitment to Quality and Customer Satisfaction:Central to the manufacturer's success is its unwavering commitment to quality assurance and customer satisfaction. Rigorous quality control measures are implemented throughout the production process, ensuring that each steel sheet and plate meets stringent industry standards. Additionally, a dedicated customer support network enhances the overall experience, providing technical assistance, after-sales service, and timely delivery.7. Corporate Social Responsibility Initiatives:Emphasizing the importance of giving back to society, the steel sheet and plate manufacturer actively engages in various corporate social responsibility initiatives. By supporting education, healthcare, and environmental conservation projects, the company aims to create a positive impact on the communities it operates in. This commitment not only aligns with their core values but also fosters positive relationships with stakeholders.Conclusion:In conclusion, the steel sheet and plate industry continues to witness significant growth and innovation, driven by companies at the forefront of this sector. This prominent steel manufacturer, exemplifying remarkable environmental practices, technological advancements, and unwavering commitment to quality, has established itself as an industry leader. With a resilient approach to navigating challenging times, the company remains steadfast in its pursuit of sustainable development, promising a prosperous future for the steel sheet and plate industry.
Unveiling the Intricate Process of Forging: An In-Depth Look
Title: Innovations in the Process of Forging Revolutionize Manufacturing IndustryIntroduction:The process of forging, a centuries-old technique of shaping metal, has undergone a transformation thanks to groundbreaking innovations introduced by several industry leaders. In particular, companies like {} have played a pivotal role in revolutionizing the manufacturing sector through their cutting-edge technologies and techniques. This article discusses how these advancements have improved the forging process, leading to enhanced product quality, increased production efficiency, and higher customer satisfaction.Body:1. The Foundations of Forging:Forging is the process of shaping metal through the application of tremendous pressure, usually with the help of hydraulic or mechanical force. Known for its strength, durability, and reliability, forged components find applications in various industries, including automotive, aerospace, defense, and construction. Traditionally, forging was a labor-intensive process that required skilled craftsmen to manually shape the metal into the desired form. However, with the advent of modern technologies, the forging industry has witnessed significant advancements, which have simplified and optimized the manufacturing process.2. Introduction of Advanced Materials:One key innovation lies in the utilization of advanced materials for forging applications. With the development of high-strength alloys, superalloys, and composite materials, manufacturers now have access to materials with enhanced characteristics, such as superior mechanical properties, heat resistance, and corrosion resistance. By utilizing these advanced materials, companies have been able to produce components that are not only lighter and more durable but also better suited for specific operational conditions.3. Computer-Aided Design and Manufacturing (CAD/CAM) Integration:Integration of computer-aided design and manufacturing (CAD/CAM) systems has been instrumental in streamlining the entire forging process. By digitizing the design, simulation, and manufacturing phases, engineers can now create intricate component geometries with enhanced precision and accuracy. CAD/CAM integration allows for the optimization of tooling and die designs, reducing material waste and production costs while improving overall product quality.4. Automation and Robotics:The introduction of automation and robotics in forging facilities has led to a significant boost in production efficiency and consistency. Intelligent robotic systems can now handle complex tasks previously performed by human operators, such as loading and unloading parts, transferring components between workstations, and performing quality inspections. This integration of automation not only improves productivity and reduces labor costs but also ensures a higher level of precision, repeatability, and safety throughout the manufacturing process.5. Simulation and Predictive Analysis:Simulations and predictive analysis tools are transforming the way manufacturers approach the forging process. Advanced software can simulate the behavior of metals under extreme heat and pressure, accurately predicting how they will deform, crack, or fail. By simulating different scenarios, engineers can optimize the process parameters, tooling designs, and material selection, reducing the time and costs associated with physical prototyping and testing. This technological advancement allows for faster development cycles, improved component quality, and increased overall efficiency.6. Additive Manufacturing in Forging:Additive manufacturing, often referred to as 3D printing, has also found its way into the realm of forging. Through the utilization of metal powders and advanced printing techniques, complex components can be fabricated layer by layer, eliminating the need for traditional forging processes. This disruptive technology offers increased design flexibility, reduced material waste, and shorter production times, enabling manufacturers to create intricate and lightweight components that were previously unattainable.7. Quality Assurance and Traceability:In addition to process improvements, modern forging techniques have also enhanced quality assurance and traceability. Manufacturers now employ advanced inspection technologies, such as non-destructive testing and optical measurement systems, to ensure that components meet the highest industry standards. Additionally, blockchain-based systems facilitate real-time traceability, providing customers with transparent information about the origin, production, and testing of forged components. These advancements instill confidence in the quality and reliability of the products while meeting the rigorous demands of various regulatory bodies.Conclusion:The evolution of the forging process, driven by the innovative technologies introduced by companies such as {}, has ushered in a new era of manufacturing excellence. From advanced materials and CAD/CAM integration to automation, simulation, and additive manufacturing, these advancements have significantly improved product quality, production efficiency, and customer satisfaction. The future of forging appears promising, with continued research and development propelling the industry towards greater innovation and success.
How Forging Blanks are Used in Manufacturing Processes
Forging Blank is a process that involves shaping metal into a specific form through the use of heat and pressure. This process is widely used in the manufacturing industry to produce a wide range of products, from automotive parts to industrial machinery.One company that is at the forefront of the forging blank industry is {}. This company has been in operation for over 50 years and has established itself as a leading provider of high-quality forged products. With a strong emphasis on innovation and continuous improvement, {} has been able to stay ahead of the competition and meet the evolving needs of its customers.The company's state-of-the-art manufacturing facilities are equipped with the latest technology and equipment, allowing them to produce forging blanks of the highest quality. Their team of experienced engineers and technicians work tirelessly to ensure that each product meets the stringent standards set by the industry.{}'s forging blanks are used in a wide range of applications, including automotive, aerospace, and industrial equipment. The company has developed strong relationships with some of the leading companies in these industries, providing them with the confidence that they can rely on {}'s products to meet their requirements.In addition to their manufacturing capabilities, {} also offers a range of value-added services to their customers. These services include engineering support, material selection, and prototype development, allowing their customers to bring their ideas to life with the help of {}'s expertise.One of the key factors that sets {} apart from its competitors is its commitment to sustainability. The company has implemented a number of initiatives to reduce its environmental impact, including the use of energy-efficient manufacturing processes and the recycling of waste materials. By taking a proactive approach to sustainability, {} is not only reducing its environmental footprint but also positioning itself as a responsible and forward-thinking supplier.Looking to the future, {} is committed to continuing its investment in research and development, with a focus on developing new and innovative forging techniques. By staying at the forefront of technological advancements, {} is ensuring that it remains a leader in the industry and can continue to meet the evolving needs of its customers.In conclusion, the forging blank industry is a vital part of the manufacturing sector, and companies like {} play a crucial role in meeting the demands of this industry. With its cutting-edge manufacturing facilities, strong emphasis on quality and innovation, and commitment to sustainability, {} is well-positioned to continue its success in the years to come.
Top-Quality CNC Milling Parts for Precision Engineering Needs
[Company Name] Expands Product Range with CNC Milling Parts [City, Date] - [Company Name], a leading manufacturer and supplier of precision components, is pleased to announce the expansion of its product range with the addition of high-quality CNC milling parts. This new addition to their offering is a testament to the company's commitment to meeting the diverse needs of its customers and enhancing its position in the market.CNC milling is a highly versatile process that allows for the creation of complex and intricate parts with impeccable precision. By utilizing computer numerical control (CNC) technology, [Company Name] can now produce milling components with extraordinary accuracy and efficiency. With state-of-the-art machinery and a team of skilled technicians, the company is well-equipped to cater to a wide range of industries, including automotive, aerospace, medical, and more.These CNC milling parts are manufactured using premium materials such as aluminum, brass, stainless steel, and various engineering plastics. The company ensures that the materials used meet the highest industry standards, guaranteeing the durability and reliability of their products. Designed to withstand rigorous applications and environments, these milling parts are ideal for various industrial applications, including prototyping, production, and customization.[Company Name]'s CNC milling parts offer numerous benefits to their customers. Firstly, the high precision and accuracy achieved by utilizing CNC technology ensure that the final products meet or exceed the strictest quality standards. This translates to improved efficiency and reduced waste, ultimately enhancing the overall productivity of businesses that rely on these components. Moreover, with the ability to produce intricate designs, customers can achieve highly customized parts that seamlessly integrate into their projects.Additionally, [Company Name] takes pride in its commitment to delivering exceptional customer service. With a strong focus on collaboration, the company works closely with its clients to understand their specific requirements and provide tailor-made solutions. From initial design and prototyping to the final production, the company's team of experts offers comprehensive support throughout the entire process. This personalized approach sets [Company Name] apart from its competitors and ensures that customers receive the highest level of satisfaction.The introduction of CNC milling parts is a strategic move by [Company Name] to expand its product range and capture a larger market share. By diversifying their offering, the company aims to create new opportunities, attract more customers, and fortify their position as a reliable and innovative supplier in the industry. With their commitment to quality, precision, and customer satisfaction, [Company Name] is confident in its ability to meet the evolving needs of the market and exceed customer expectations.Looking ahead, [Company Name] plans to continue investing in research and development to further enhance its CNC milling capabilities. By staying at the forefront of technological advancements, the company aims to provide cutting-edge solutions that contribute to the success of its customers' projects.For more information about [Company Name]'s CNC milling parts and their complete range of precision components, please visit their website [website link].About [Company Name]:[Company Name] is a leading manufacturer and supplier of precision components, offering a wide range of products for various industries. With a commitment to quality, innovation, and customer satisfaction, [Company Name] has established itself as a trusted partner in the market. The company's state-of-the-art facilities, skilled workforce, and dedication to excellence position it as a reliable source for precision components. For more information, please visit [website link].Media Contact:[Contact Name][Company Name][Email Address][Phone Number]
High-Quality Forged Ball Valve: A Reliable Solution for Your Plumbing Needs
FORGING BALL VALVES: Ensuring Precision and Performance for Industrial ApplicationsIn today's rapidly advancing industrial landscape, companies are constantly seeking innovative solutions to bolster their operational efficiency and ensure the highest standards of performance. Among the critical components that enable smooth operations are forging ball valves, which play a vital role in controlling the flow of various fluids and gases. By combining advanced engineering techniques with cutting-edge materials, manufacturers are revolutionizing the quality and reliability of these valves, propelling industries into the future.Seeking to deliver these benefits to numerous industries, {Company Name}, a leading manufacturer of industrial valves, has introduced its state-of-the-art forging ball valves. With a reputation built on decades of engineering expertise and commitment to customer satisfaction, {Company Name} is dedicated to meeting the evolving needs of industries worldwide.Forging is a manufacturing process that involves shaping metal by applying compressive forces using hammers or presses. Compared to casting, forging enhances the mechanical properties of components, ensuring greater strength, durability, and resistance to external stress factors. By incorporating forging techniques into the production of ball valves, {Company Name} aims to provide superior performance and reliability, minimizing downtime and maximizing productivity for their customers.One of the key advantages of {Company Name}'s forging ball valves lies in their ability to withstand high-pressure environments. These valves are designed to efficiently regulate fluid and gas flow even under extreme operating conditions. This ensures uninterrupted operations for industries such as oil and gas, power generation, and petrochemicals, where pressure differentials can be substantial.Furthermore, {Company Name}'s forging ball valves offer exceptional resistance to corrosion, erosion, and wear and tear. Their robust construction and advanced material selection mitigate the risk of leakage or failure, improving the overall safety and reliability of industrial processes. By ensuring the integrity of fluid containment systems, these valves help protect employees, the environment, and valuable equipment.In addition to their superior performance, {Company Name}'s forging ball valves are engineered for ease of maintenance. The valves incorporate features that allow for quick and effortless disassembly and reassembly, which minimizes downtime during routine inspections or repairs. This results in increased operational efficiency and reduced maintenance costs for industries where uptime is critical.As a responsible industry player, {Company Name} also prioritizes environmental sustainability. The forging process employed in the manufacture of these valves reduces material waste compared to traditional casting methods, making it an environmentally friendly option. Furthermore, by prolonging the lifespan of equipment and preventing leaks or failures, {Company Name}'s forging ball valves contribute to the conservation of resources and the reduction of greenhouse gas emissions.{Company Name} continues to lead the forging ball valve industry through ongoing research and development. Its dedicated team of engineers constantly explores new materials, designs, and manufacturing techniques to enhance the performance and reliability of their valves. By closely collaborating with customers, {Company Name} ensures that its products are tailored to meet specific industry requirements and exceed expectations.In conclusion, {Company Name}'s forging ball valves offer a new standard of precision, performance, and reliability in the industrial sector. By leveraging the advantages of the forging process, these valves provide enhanced durability, resistance to high pressure and corrosion, and ease of maintenance, ultimately driving operational efficiency for a wide range of industries. As the company continues to innovate and collaborate, it remains at the forefront of forging ball valve technology, empowering industries worldwide to achieve excellence in their operations.
High-Quality Custom Forging Parts for Various Industries
Custom Forging Parts is a company that specializes in providing high-quality, custom forging solutions for various industries. With over 20 years of experience in the industry, they have built a strong reputation for their reliability, quality, and customer service. Their diverse capabilities and advanced technology allow them to produce a wide range of custom forging parts to meet their clients' unique specifications.The company is known for their commitment to excellence and their ability to deliver tailor-made solutions for all of their customers. From initial design to final production, Custom Forging Parts works closely with their clients to ensure that their products meet the highest standards of quality and performance. Their team of highly skilled engineers and technicians are dedicated to providing innovative solutions and exceeding customer expectations.One of the key advantages of working with Custom Forging Parts is their ability to produce custom forging parts in a variety of materials, including carbon steel, stainless steel, aluminum, and more. This flexibility allows them to meet the specific needs of each customer and provide them with the best possible solution for their application. Whether it's a small batch of prototypes or a large-scale production run, Custom Forging Parts has the capabilities to deliver high-quality parts on time and within budget.In addition to their custom forging capabilities, Custom Forging Parts also offers a range of value-added services to further meet the needs of their customers. These services include machining, heat treating, surface finishing, and testing, ensuring that their products are ready for use upon delivery. This comprehensive approach to manufacturing allows them to provide a one-stop solution for all of their customers' forging needs.Furthermore, Custom Forging Parts is committed to maintaining the highest standards of quality and safety in all of their operations. They adhere to stringent quality control processes and invest in the latest technology to ensure that every part they produce meets the required specifications and complies with industry standards. This dedication to quality and safety has earned them the trust and loyalty of many customers across various industries.The company also takes pride in their ability to provide cost-effective solutions without compromising on quality. By leveraging their experience, expertise, and advanced manufacturing capabilities, they are able to optimize their processes and deliver products at competitive prices. This value proposition has been a significant factor in their success and has allowed them to establish long-term relationships with many of their clients.Custom Forging Parts serves a wide range of industries, including automotive, aerospace, defense, energy, and more. Their ability to adapt to the unique requirements of each industry and provide custom solutions has made them a preferred partner for many companies looking for high-quality forging parts.With a strong commitment to excellence, a customer-centric approach, and a dedication to innovation, Custom Forging Parts continues to be a leading provider of custom forging solutions for a diverse range of industries. Their ability to deliver high-quality, custom forging parts has positioned them as a trusted partner for companies looking for reliable and cost-effective manufacturing solutions. As they continue to expand their capabilities and invest in the latest technologies, Custom Forging Parts is well-positioned to meet the evolving needs of the market and provide their customers with the best possible forging solutions.