High-Quality Titanium Forging: Impact, Applications, and Benefits
By:Admin
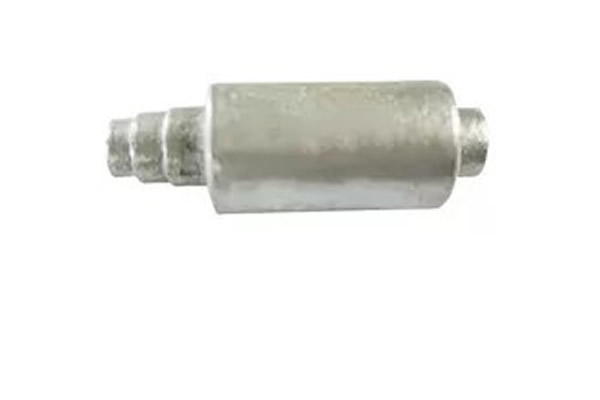
With the increasing demand for high-performance components in various industries, [Company Name] has emerged as a leading provider of titanium forging services. The company has developed advanced techniques and state-of-the-art equipment to cater to the ever-growing needs of the market. With a strong focus on quality and precision, [Company Name] has positioned itself as a reliable partner for businesses looking to incorporate titanium forged components into their products.
One of the key advantages of titanium forging is the ability to create complex shapes and intricate designs that would be difficult or impossible to achieve through other manufacturing processes. This flexibility has made titanium forging a preferred choice for applications where strength and reliability are crucial. In addition, titanium forged components are known for their excellent fatigue resistance, making them ideal for use in aerospace and automotive industries where safety and performance are paramount.
One of the primary industries that [Company Name] serves is the aerospace sector, where the demand for lightweight yet strong components is constantly on the rise. Titanium forged parts are widely used in aircraft engines, structural components, landing gears, and other critical systems due to their exceptional mechanical properties and high-temperature performance. By leveraging its expertise in titanium forging, [Company Name] has been able to meet the stringent requirements of the aerospace industry and has established itself as a trusted supplier to major aerospace manufacturers.
In addition to aerospace, [Company Name] also caters to the automotive industry, where the demand for high-strength and lightweight components is steadily increasing. Titanium forged parts are used in high-performance vehicles, racing cars, and even in mainstream automobiles due to their ability to improve fuel efficiency and overall performance. By offering tailored solutions and quick turnaround times, [Company Name] has become a preferred partner for automotive companies looking to stay ahead of the competition.
Furthermore, [Company Name] has also made significant inroads into the medical industry by providing titanium forged components for medical implants and instruments. Titanium's biocompatibility and corrosion resistance make it an ideal material for medical applications, and the precision manufacturing capabilities of [Company Name] ensure that the highest standards of quality and safety are met. The company's commitment to excellence in the medical field has earned it a reputation for producing top-notch titanium forged products that adhere to strict regulatory standards.
Looking ahead, [Company Name] is committed to staying at the forefront of titanium forging technology by investing in research and development, as well as continuously upgrading its manufacturing facilities. The company is also focused on expanding its global footprint and reaching new markets to meet the growing demand for titanium forged components. By staying true to its core values of innovation, quality, and customer satisfaction, [Company Name] is poised to lead the way in the titanium forging industry and provide businesses with the high-quality components they need to succeed in today's competitive market.
In conclusion, titanium forging is a critical manufacturing process that has become indispensable in a wide range of industries. As a leading provider of titanium forging services, [Company Name] is dedicated to delivering superior products that meet the highest standards of quality, performance, and reliability. With its extensive expertise and commitment to innovation, [Company Name] is well-positioned to meet the evolving needs of the market and continue to be a trusted partner for businesses seeking top-notch titanium forged components.
Company News & Blog
Quality Hand Forged Iron Coat Hooks: A Must-Have for Every Home!
Hand Forged Iron Coat Hooks: The Perfect Combination of Style and FunctionCoat hooks serve an essential purpose in our everyday lives, offering a convenient solution for organizing our outerwear. While functionality is undoubtedly important, it does not mean compromising on style. Hand Forged Iron Coat Hooks, an innovative product (brand name needed), is taking the market by storm with its unique blend of functionality and aesthetics.Hand Forged Iron Coat Hooks are meticulously crafted using traditional blacksmithing techniques. The company behind this exquisite creation, which is committed to bringing art into everyday life, has been a prominent figure in the industry for years.The manufacturing process begins with skilled craftsmen who heat iron rods in a forge until they are malleable enough to be shaped into the desired form. These craftsmen skillfully transform these rods into beautifully designed hooks by carefully hammering, twisting, and welding each piece with the utmost care and precision.The result is an astonishing range of hand forged iron coat hooks that are not only practical but also a true work of art. Each hook is unique, showcasing the individuality and creativity of the craftsmen. The attention to detail is evident in every curve and twist, creating a visually appealing element for any living space.But Hand Forged Iron Coat Hooks, however visually stunning, are not just for decorative purposes. Coming in a variety of sizes and styles, they offer a practical storage solution for your coats, hats, scarves, and other items that need to be easily accessible. The sturdy iron construction ensures they can withstand the weight of heavy winter coats, while still maintaining their timeless aesthetic appeal.Additionally, Hand Forged Iron Coat Hooks also offer versatility in their installation options. Whether you prefer a traditional wall-mounted design or wish to create a unique display using a stylish coat rack, these hooks can be easily adapted to suit your individual needs and design preferences.Moreover, these hooks are not limited to home use alone. The durability and unique design make them a perfect addition to commercial spaces such as hotels, restaurants, and boutiques. They add a touch of elegance and sophistication while providing customers with a functional and convenient storage option.When compared to mass-produced hooks, Hand Forged Iron Coat Hooks stand out for their superior quality and craftsmanship. Each hook is carefully inspected to ensure it meets the company's high standards before reaching the customers' hands. The attention to detail and commitment to excellence set these hooks apart from their competitors.In addition to their exceptional products, the company follows environmentally friendly practices throughout their manufacturing process. By utilizing traditional blacksmithing techniques, they minimize the negative impact on the environment commonly associated with mass production.Hand Forged Iron Coat Hooks have quickly gained popularity among interior designers and homeowners alike. Their ability to effortlessly blend into various interior styles, whether it be rustic, traditional, or contemporary, has made them an essential element in creating visually appealing and functional spaces.In conclusion, Hand Forged Iron Coat Hooks have emerged as a leading choice for those seeking a perfect combination of functionality and style. With their unmatched craftsmanship, attention to detail, and commitment to quality, these hooks are sure to be a valuable addition to any living or commercial space. By choosing Hand Forged Iron Coat Hooks, you not only invest in a practical storage solution but also add a touch of timeless elegance and beauty to your everyday surroundings.
New Developments in Cold Forging Die Technology: Exploring Advancements in Metal Forming Processes
Title: Advancements in Cold Forging Die Technology Enhance Manufacturing Efficiency Introduction:In a world where precision and efficiency are paramount, companies across various sectors are continually seeking advanced techniques and tools to optimize their manufacturing processes. Cold forging, a metalworking technique known for its ability to produce high-quality components with exceptional strength and precision, has witnessed a significant breakthrough with the introduction of a cutting-edge Cold Forging Die by {} (company name).Cold Forging Die Technology:The recently developed Cold Forging Die by {} is revolutionizing the manufacturing industry. With its state-of-the-art design and innovative features, this tool ensures improved production efficiencies, reduced costs, and enhanced product quality. The cold forging process involves shaping a metallic workpiece by applying immense pressure at ambient temperatures. The Cold Forging Die, an essential component in this process, plays a critical role in determining the accuracy, productivity, and longevity of the finished products.By removing the inherent limitations of traditional forging dies, the advanced technology employed in the Cold Forging Die by {} delivers unparalleled precision and durability. The die's design incorporates cutting-edge materials, surface treatments, and advanced coatings that significantly reduce wear and tear, thereby extending its lifespan and minimizing downtime requirements for die replacement.Key Features and Benefits:1. Enhanced Durability: The Cold Forging Die by {} boasts exceptional durability due to the utilization of premium quality materials and specialized surface treatments. This ensures the die can withstand high-pressure forces, reducing the need for frequent replacements and minimizing associated costs.2. Improved Precision: With stringent accuracy requirements in various industries, this advanced die technology guarantees precise shaping and dimensional stability for the forged components. The die's design incorporates optimal geometries and surface finishes, resulting in flawless product formation and increased reliability.3. Customization: {} understands the diverse requirements of different industries and offers a range of customized Cold Forging Dies. This flexibility allows manufacturers to produce components with complex shapes, enhancing their product portfolio and expanding market opportunities.4. Cost Efficiency: By optimizing the cold forging process, this advanced die technology increases production efficiency, leading to reduced lead times and enhanced cost-effectiveness. The die's superior performance minimizes material waste during manufacturing, ensuring maximum yield and reducing overall production costs.5. Versatility: {} Cold Forging Dies efficiently cater to a wide array of applications across industries like automotive, electronics, construction, and machinery. Whether it's forming intricate slots, threads, or intricate shapes, these dies offer versatility and reliability to meet the diverse needs of manufacturers.Company Overview:With a vision to revolutionize the metalworking industry, {} (company name) has been at the forefront of innovative manufacturing solutions for over two decades. The company's commitment to research and development, coupled with its customer-centric approach, has enabled them to introduce groundbreaking tools such as the Cold Forging Die.As an industry leader, {} constantly strives for excellence and has established a strong reputation for delivering world-class precision tools. Their team of experienced engineers and technicians collaborate closely with clients to understand their specific requirements and develop tailored solutions.Conclusion:The introduction of the cutting-edge Cold Forging Die by {} marks a significant milestone in the manufacturing industry. As companies strive for greater efficiency, precision, and cost-effectiveness, this advanced die technology offers unparalleled benefits. With its enhanced durability, improved precision, and customization options, {} Cold Forging Dies are set to revolutionize the cold forging process, attracting manufacturers across various industries. Expect notable advancements and further innovation from {} as they continue to shape the future of the metalworking industry.
Streamlined Guide to Gravity Die Casting: Everything You Need to Know
Gravity Die Casting: Efficient and Precise Manufacturing TechnologyIn the world of manufacturing and production, efficiency and precision are the key factors that contribute to the success of any company. One such technology that has revolutionized the industry is gravity die casting - a method employed for manufacturing high-quality metal components with exceptional dimensional accuracy. Today, we will explore the gravity die casting process and its impact on the manufacturing sector, focusing on the remarkable achievements of a leading company {}.Gravity die casting, also known as permanent mold casting, is a reliable and cost-effective method to produce complex metal components with consistent quality. The process involves pouring molten metal into a metallic mold, which is later cooled and solidified to form the desired shape. Unlike other casting techniques, gravity die casting utilizes the force of gravity to fill the mold, resulting in reduced turbulence and better control over the casting process. This ensures improved surface finish, dimensional accuracy, and enhanced mechanical properties of the end product.Established in {}, {} has emerged as a pioneer in gravity die casting technology. With a stellar reputation built on years of experience and innovation, the company has successfully catered to the diverse needs of industries such as automotive, aerospace, defense, and consumer goods. Their commitment to quality and continuous improvement has propelled them to the forefront of the gravity die casting industry.Taking advantage of advanced machinery and state-of-the-art facilities, {} offers a comprehensive range of gravity die casting services. Their team of highly skilled engineers and technicians meticulously design and manufacture the molds required for the casting process. This ensures that each component produced adheres to the strictest specifications and quality standards. Furthermore, {} boasts an extensive material selection, allowing customers to choose from various alloys, including aluminum, zinc, and brass.The benefits of gravity die casting extend beyond the impeccable quality of the components. Its cost-efficiency, by reducing material waste and minimizing machining requirements, makes it an attractive choice for manufacturers. Additionally, the process is highly scalable, enabling {} to meet both low and high volume production demands without compromising on quality or lead times. Their dedication to delivering on-time and within budget has earned them the trust of numerous renowned clients.While gravity die casting is primarily associated with metal components, {} has pushed the boundaries of this manufacturing process. Their continuous investment in research and development has allowed them to expand their capabilities to include innovative applications such as gravity die casting of ceramics and composites. This pioneering approach has opened new doors in various industries and positioned {} as a leading provider of cutting-edge casting solutions.However, {}'s achievements are not limited to technological prowess alone. As a socially responsible company, they prioritize sustainability and environmental conservation. By implementing eco-friendly practices such as recycling and waste reduction, the company minimizes its carbon footprint and contributes to a greener future. This commitment to sustainable manufacturing has garnered {} recognition and accolades from industry peers and regulatory bodies alike.In conclusion, gravity die casting has revolutionized the manufacturing sector by offering efficient and precise production of high-quality metal components. With {} at the forefront of this technology, companies across various industries benefit from their exceptional expertise and commitment to excellence. As they continue to push boundaries and explore new frontiers in casting, {} establishes itself as an unrivaled leader in the field.
What Is Cold Forging and How Does it Affect the Manufacturing Industry?
Cold Forging Revolutionizes Manufacturing: A Look Into the World of Advanced Metal FormingIn an era of constant innovation and technological advancements, the manufacturing industry continues to evolve at an unprecedented rate. Among the many cutting-edge techniques developed, cold forging has emerged as a game-changer, revolutionizing the way metal components are manufactured. This widely-adopted process is reshaping industries, offering improved quality, efficiency, and sustainability. In this article, we delve into the world of cold forging, exploring its benefits and its impact on manufacturing.Before we explore the specifics of cold forging, let's take a closer look at the company leading the charge in this groundbreaking technology. (Company name), a global leader in advanced metal forming solutions, has been at the forefront of driving innovation in manufacturing for over three decades. Their commitment to excellence and their deep understanding of customer needs have propelled them to the forefront of the industry.(Company name) has developed a reputation for producing state-of-the-art equipment and technology, continuously pushing the boundaries of what is possible in metal forming. Their expertise extends to various industries, including automotive, aerospace, electronics, and more, answering the demand for precision and reliability in manufacturing processes. With an extensive portfolio of solutions and a global network of partners, (Company name) remains dedicated to transforming the manufacturing landscape.Now, let's focus on the transformative power of cold forging. Used to manufacture metal components, cold forging is a forming process that shapes metal at or near room temperature. Unlike traditional hot forging methods, where the metal is heated before shaping, cold forging eliminates the need for excessive energy consumption and the associated emissions. This results in a more sustainable and eco-friendly manufacturing process.The benefits of cold forging extend beyond environmental considerations. The process, renowned for its precision and efficiency, ensures components are formed accurately, with consistent dimensions and high tolerance levels. This level of precision enables manufacturers to produce components that operate flawlessly, reducing the risk of failures caused by variations in size or geometry.Additionally, the improved material utilization achieved through cold forging minimizes waste and enhances cost-effectiveness. By reducing material waste during the manufacturing process, manufacturers can optimize their resources and save costs in raw materials. Consequently, this cost-effectiveness translates into better pricing for end consumers, making products more affordable and accessible.The automotive industry, one of the sectors at the forefront of cold forging adoption, has experienced substantial benefits from this technology. With the increasing demand for lightweight and fuel-efficient vehicles, cold-forged components offer an ideal solution. The process allows manufacturers to create complex, yet lightweight parts, ensuring both performance and sustainability. From engine components to steering and suspension parts, cold-forged components contribute to improved fuel efficiency, reduced emissions, and enhanced overall vehicle performance.Moreover, the adaptability of cold forging allows manufacturers to create intricate designs and complex geometries that were previously challenging using conventional methods. This flexibility expands the range of possibilities in component design and functionality, enabling engineers to push the boundaries of innovation further. With cold forging, manufacturers can meet the ever-growing demands of modern industries, delivering products that are not only functional but aesthetically appealing as well.In conclusion, cold forging is transforming the manufacturing industry, redefining the way metal components are produced. Through its precision, efficiency, and sustainability, this advanced metal forming process has become an integral part of many sectors, including automotive, aerospace, and electronics. Companies like (Company name) continue to lead the charge in developing cutting-edge technology and solutions to meet the evolving demands of the industry. As we move forward into the future, cold forging will undoubtedly play a significant role in advancing manufacturing practices, creating a more sustainable and efficient world.
Effective Forging Equipment: Boosting Efficiency and Precision for Industrial Operations
Title: Next-Generation Forging Equipment Revolutionizes the Manufacturing IndustryIntroduction:In today's ever-evolving manufacturing industry, companies are constantly seeking innovative tools and technologies to enhance their production processes. The latest breakthrough in forging equipment, developed by an industry-leading company, promises to revolutionize the way manufacturers produce high-quality components. Leveraging cutting-edge technologies, this next-generation forging equipment improves efficiency, reduces costs, and ensures superior product quality.Section 1: What is Forging Equipment?Forging equipment refers to machines and tools used in metalworking processes, specifically the shaping and forming of metal components through the application of heat and pressure. The process involves deforming metal using localized compressive forces to achieve the desired shape and strength in the final product. Traditionally, forging has been performed using hammers or presses, but recent advancements in technology have paved the way for more sophisticated and efficient equipment.Section 2: Company Introduction and ExpertiseWith a rich history of innovation and expertise in the manufacturing industry, the company behind this next-generation forging equipment has established itself as a global leader. Drawing on decades of experience and extensive research and development, this industry pioneer has consistently delivered groundbreaking solutions that have reshaped various industrial sectors. Combining state-of-the-art technologies with a commitment to operational excellence, the company ensures its products meet the highest standards of quality, efficiency, and safety.Section 3: The Features and Benefits of the Next-Generation Forging EquipmentThe next-generation forging equipment developed by this pioneering company introduces several new features and benefits that set it apart from traditional forging machinery.3.1 Advanced Automation:The new forging equipment leverages advanced automation technologies, including robotics, machine learning, and artificial intelligence. This automation drastically reduces the need for manual intervention, streamlining the production process and minimizing the risk of human errors. By automating repetitive tasks, manufacturers can achieve higher production volumes, improve overall efficiency, and reduce labor costs.3.2 Precision and Consistency:The cutting-edge software integrated into the forging equipment ensures precise control over temperature, pressure, and other critical parameters. This precision enhances the quality and structural integrity of the forged components, leading to consistent outcomes. Manufacturers can now confidently produce complex shapes and intricate designs, allowing for greater product versatility and customization.3.3 Energy Efficiency:The next-generation forging equipment emphasizes energy efficiency, employing innovative techniques to reduce energy consumption during the forging process. By optimizing power usage and minimizing heat loss, manufacturers can significantly reduce their environmental footprint and operational costs.3.4 Safety and Maintenance:This revolutionary forging equipment prioritizes safety by incorporating advanced safety features such as real-time monitoring, automatic fault detection, and emergency shutdown systems. Additionally, predictive maintenance algorithms continuously monitor the equipment's performance, enabling proactive maintenance planning and minimizing downtime.Section 4: Case Studies and Real-World ApplicationsSeveral leading manufacturers across various industries have already adopted this next-generation forging equipment, benefiting from its advanced capabilities.4.1 Automotive Industry:For automobile manufacturers, the new forging equipment enables the production of lightweight, high-strength components critical for improving fuel efficiency and enhancing vehicle performance. Moreover, the precision and consistency of the equipment ensure the production of complex engine parts, resulting in enhanced reliability and durability.4.2 Aerospace Sector:The aerospace industry demands uncompromising quality, reliability, and precision. The new forging equipment meets these requirements, enabling the production of critical aerospace components, including turbine blades, landing gear, and structural elements. The equipment's high precision ensures the parts meet stringent quality standards, enhancing overall aircraft safety.Section 5: Future Implications and ConclusionThe next-generation forging equipment represents a giant leap forward for the manufacturing industry. This innovative technology opens doors for manufacturers to achieve higher productivity, improved quality, and greater customization. As more companies embrace this cutting-edge forging machinery, the industry as a whole will experience enhanced competitiveness and increased market opportunities. With continuous advancements in materials science and technology, the potential for further innovation in forging equipment remains promising, allowing manufacturers to meet the demands of a rapidly changing world.
Top Quality Rail Base Plate for Your Project Needs
Rail Base PlateRail base plate is an important component in the construction of railway tracks. It serves as a supporting base for the rails and provides stability to the entire track structure. The design and quality of the rail base plate are crucial in ensuring the safety and efficiency of the railway system.The rail base plate is typically made of high-quality steel or iron, and it is installed between the rail and the sleepers. Its primary function is to distribute the load of the train across a larger surface area, thereby reducing the pressure on the sleepers and the underlying ballast. This helps to prevent the track from sinking or deforming under the weight of the trains.In addition to providing support and stability to the rails, the rail base plate also helps to maintain the correct gauge (the distance between the rails) and alignment of the tracks. This is essential for smooth and safe train operations, as any deviation from the standard gauge or alignment can lead to derailments and other serious accidents.Rail base plates are available in various designs and specifications to suit different types of railway tracks and operational requirements. They can be customized to accommodate different rail profiles, such as flat-bottomed rails or grooved rails, and they can be manufactured to withstand heavy loads and extreme weather conditions.One of the leading manufacturers of rail base plates is {company name}. The company has been specializing in the production of railway track components for over {number} years, and it has earned a reputation for delivering high-quality products that meet international standards.{Company name} offers a wide range of rail base plates that are designed to meet the specific needs of railway operators and contractors. Its products are known for their durability, reliability, and cost-effectiveness, making them the preferred choice for railway construction and maintenance projects around the world.The manufacturing process at {company name} involves the use of advanced technology and strict quality control measures to ensure that every rail base plate meets the required standards. The company has a team of experienced engineers and technicians who oversee the production process and conduct thorough inspections to guarantee the performance and safety of the products.In addition to its standard range of rail base plates, {company name} also provides custom solutions to address unique project requirements. Its technical team works closely with clients to understand their specific needs and develop tailor-made designs that will optimize the performance and longevity of the railway tracks.{Company name}'s commitment to excellence extends beyond the quality of its products. The company also places a strong emphasis on customer service, providing technical support, timely delivery, and competitive pricing to ensure customer satisfaction. Its team of sales and support staff is dedicated to helping clients find the best solutions for their railway track needs.With its extensive experience, technical expertise, and dedication to quality, {company name} has established itself as a trusted partner for railway infrastructure projects. Its rail base plates have been used in various railway systems, including high-speed rail networks, urban transit systems, and freight train routes, demonstrating their versatility and reliability in diverse operating environments.As the demand for efficient and reliable railway transportation continues to grow, the role of rail base plates in maintaining safe and stable tracks becomes increasingly vital. With {company name} at the forefront of rail base plate manufacturing, railway operators and contractors can be assured of superior products that will contribute to the longevity and performance of their track systems.
Latest News in the World of Forgings, Flanges & Fittings
Forgings Flanges & Fittings Announces Expansion and Commitment to Quality Excellence[City, Date] - Forgings Flanges & Fittings (FFF), a leading global manufacturer and supplier of high-quality mechanical and industrial products, is pleased to announce its expansion plans and unwavering commitment to delivering excellence in quality and innovation.With a rich legacy spanning over several decades, FFF has established itself as a reliable and trusted name in the industry. With a diverse product range that includes forgings, flanges, and fittings, the company caters to a wide range of sectors, including oil and gas, petrochemicals, power generation, and various other heavy industries.FFF takes great pride in its state-of-the-art manufacturing facilities, equipped with advanced machinery and a highly skilled workforce. The company's dedication to quality is reflected in every aspect of its operations, from sourcing raw materials to the final inspection of finished goods. FFF's commitment to meeting and exceeding international quality standards is evident through its various certifications, including ISO 9001 and API monograms.Recognizing the growing demand for its products and the need to cater to a global clientele, FFF has embarked on an ambitious expansion plan. The company aims to enhance its production capabilities by investing in cutting-edge technologies and expanding its manufacturing facilities. This expansion will allow FFF to increase its production capacity, meet customer demands more efficiently, and maintain its position as a market leader.The expansion plan also includes the establishment of new distribution centers in key regions, strategically located to ensure timely and seamless delivery of products to customers worldwide. By strengthening its distribution network, FFF aims to further enhance its customer service and extend its reach to new markets.To support its expansion efforts, FFF is committed to fostering innovation and research and development within the organization. By continuously investing in technological advancements and product improvements, FFF aims to stay at the forefront of industry trends and deliver cutting-edge solutions to its customers.Furthermore, FFF recognizes the importance of sustainability and aims to reduce its environmental impact through responsible manufacturing practices. The company is dedicated to implementing sustainable initiatives, such as the efficient utilization of resources, waste reduction, and the adoption of eco-friendly technologies.Over the years, FFF has built strong relationships with its clients, based on trust, reliability, and superior quality. The company remains committed to providing the highest level of customer satisfaction by offering tailor-made solutions and exceptional after-sales service. FFF values its customers' feedback and continuously works towards improving its processes to meet evolving customer needs effectively.As FFF embarks on this new phase of growth, it reaffirms its commitment to upholding the highest standards of quality, reliability, and customer satisfaction. By expanding its operations, investing in research and development, and prioritizing sustainability, FFF aims to solidify its position as a global leader in the mechanical and industrial products industry.About Forgings Flanges & FittingsFounded in [Year], Forgings Flanges & Fittings (FFF) is a globally recognized manufacturer and supplier of high-quality mechanical and industrial products. With a vast product portfolio catering to various industries, FFF has established itself as a trusted name known for its commitment to quality and customer satisfaction. FFF's manufacturing facilities are equipped with cutting-edge technology, and its skilled workforce ensures the delivery of superior products to clients worldwide. The company's dedication to excellence has earned it several certifications, confirming its compliance with international quality standards. For more information, please visit [Company Website].Press Contact:[Name][Title][Phone][Email]
How To Make Successful Casting Investments: A complete Guide
Investment in Casting IndustryThe global casting industry has been experiencing significant growth over the past few years, and this trend is expected to continue in the foreseeable future. One of the leading companies in this industry, {} has recently announced a substantial investment in its casting division. This investment not only marks a significant milestone for the company but also reflects the positive outlook for the casting industry as a whole.{} is a renowned company with a strong presence in the casting industry. With a reputation for delivering high-quality products and innovative solutions, the company has established itself as a key player in the global market. Its commitment to excellence and continuous improvement has set it apart from its competitors, and the recent investment in its casting division is a testament to its dedication to staying ahead of the curve.The investment in the casting division is aimed at expanding production capacity, increasing efficiency, and enhancing the overall capabilities of the company. With the demand for cast metal products on the rise, this investment comes at a crucial time and positions {} to capitalize on the growing market opportunities. By leveraging the latest technologies and implementing best practices, the company is well-positioned to meet the evolving needs of its customers and maintain its competitive edge in the industry.In addition to its focus on technological advancements, {} is also committed to sustainability and environmental responsibility. The investment in the casting division includes initiatives to reduce energy consumption, minimize waste, and lower the company's carbon footprint. By integrating sustainable practices into its operations, {} is not only contributing to a healthier planet but also meeting the expectations of environmentally conscious customers and stakeholders.Furthermore, the investment in the casting division is expected to create new job opportunities and drive economic growth in the regions where {} operates. As the company expands its production capacity and broadens its capabilities, it will need to hire skilled workers, engineers, and support staff to meet the growing demand for its products. This will not only benefit the local economies but also contribute to the development of a highly skilled workforce in the casting industry.Commenting on the investment, the CEO of {} expressed optimism about the future of the casting industry and the company's position in the market. He stated, "The investment in our casting division reflects our confidence in the growth potential of the industry and our commitment to delivering value to our customers. By expanding our capabilities and investing in sustainable practices, we are positioning {} for long-term success and leadership in the casting market."The announcement of the investment in the casting division has been well-received by industry experts, analysts, and stakeholders. Many have lauded {} for its forward-thinking approach and strategic investments, which are expected to yield positive outcomes for the company and the casting industry as a whole.Looking ahead, the investment in the casting division is poised to elevate {} to new heights of success and strengthen its position as a global leader in the casting industry. With a focus on innovation, sustainability, and customer satisfaction, {} is well-equipped to navigate the evolving market dynamics and capitalize on the opportunities that lie ahead. As the demand for cast metal products continues to rise, the investment will enable {} to meet this demand while maintaining its reputation for excellence and reliability.In conclusion, the recent investment in the casting division underscores {}'s unwavering commitment to innovation, sustainability, and growth. By expanding its production capacity, enhancing efficiency, and embracing sustainable practices, the company is poised to seize the opportunities presented by the thriving casting industry. As a result, {} is well-positioned to drive positive change, create value for its stakeholders, and maintain its leadership position in the global market.
Improve Floor Safety with Durable and Versatile Plastic Floor Pads
Plastic Floor Pad Revolutionizes Cleaning Industry with Cutting-Edge TechnologyIn recent years, the demand for efficient and effective cleaning solutions has been on the rise, and that's where the plastic floor pad, pioneered by an innovative company, comes into play. With a vision to provide the cleaning industry with a game-changing solution, this company has completely transformed the way floors are cleaned. By combining cutting-edge technology with a commitment to sustainable practices, the plastic floor pad has quickly become the go-to choice for businesses and households around the globe.Traditional floor cleaning methods typically involve the use of bulky and cumbersome equipment that is not only time-consuming but also inefficient. However, with the introduction of the plastic floor pad, cleaning tasks have become much easier and more cost-effective. This revolutionary product is made from a durable and eco-friendly plastic material, which ensures optimal performance while also reducing environmental impact.One of the key features that sets the plastic floor pad apart from its competitors is its unique design. The advanced technology used in its manufacturing process allows for an increased surface area, resulting in a much more efficient cleaning process. The pad's microfibers are intricately woven together, creating a strong yet gentle material that tackles even the toughest dirt and grime.Another significant advantage of the plastic floor pad is its versatility. It can be used on a wide range of surfaces, including hardwood, laminate, and tile floors, making it an ideal choice for both residential and commercial applications. Whether it's removing stubborn stains or simply giving floors a deep clean, this product is guaranteed to deliver outstanding results every time.Furthermore, the plastic floor pad is equipped with a user-friendly attachment system, which makes it compatible with most cleaning machines available in the market. This means that upgrading existing cleaning equipment to incorporate this innovative pad is a straightforward and cost-effective process for businesses. Additionally, its easy-to-remove and replace design ensures minimal downtime during the cleaning process, resulting in increased efficiency and productivity.Moreover, the company behind the plastic floor pad is committed to sustainability, and this dedication is deeply ingrained in every aspect of their operations. By utilizing recycled plastic materials in the pad's manufacturing process, they are actively contributing to reducing plastic waste and promoting a circular economy. This commitment to sustainable practices has garnered the company widespread recognition and praise from environmental organizations worldwide.The plastic floor pad has already made significant waves in the cleaning industry, revolutionizing the way floors are cleaned. Its cutting-edge technology, versatility, and commitment to sustainability have earned it a loyal customer base and numerous accolades. Users have reported remarkable improvements in cleaning efficiency, reduced cleaning costs, and a noticeable decrease in environmental impact.As the demand for eco-friendly and efficient cleaning solutions continues to grow, the plastic floor pad is poised to dominate the market. With its revolutionary design, commitment to sustainability, and proven effectiveness, it is not surprising that more and more businesses and households are making the switch. Embracing this innovative technology allows for cleaner and healthier living and working environments while minimizing our impact on the planet.In conclusion, the plastic floor pad has become a game-changer in the cleaning industry. With its revolutionary design, advanced technology, and commitment to sustainability, it has transformed the way floors are cleaned. As businesses and households continue to prioritize efficiency and environmental responsibility, the plastic floor pad is at the forefront, leading the charge towards a cleaner and greener future.
Mastering the Art of Lost Wax Casting: Exploring the Intricacies of Wax Casting for Supreme Craftsmanship
Title: Innovations in Lost Wax Casting Elevate Manufacturing IndustryIntroduction:In the ever-evolving landscape of manufacturing, Lost Wax Casting has emerged as a revolutionary technique that offers endless possibilities for creating intricate and high-quality metal products. This ancient method, also known as investment casting, showcases the fusion of tradition and modern technology, leading to remarkable advancements in various industries. In this news piece, we will delve into the world of Lost Wax Casting and explore its applications, benefits, and the contributions made by a leading company in this field, {}. I. History and Evolution of Lost Wax Casting:Lost Wax Casting has a rich history that dates back over 5,000 years. The technique was initially employed by ancient Egyptians to create jewelry and intricate ornaments. Over time, this casting process spread to other civilizations such as the Greeks, Romans, and Chinese, who utilized it to craft sculptures and decorative objects. However, it was not until the 20th century that Lost Wax Casting witnessed significant improvements. With the advent of advanced materials and cutting-edge technology, the process became more precise and efficient, enabling the creation of complex shapes and intricate details.II. The Lost Wax Casting Process:Lost Wax Casting involves several meticulous steps to produce exceptional metal products. The process begins with the creation of a detailed wax prototype, often done by skilled craftsmen or aided by computer-aided design (CAD). This wax model is coated with a ceramic shell, and when the shell hardens, the wax is melted or burned out, leaving behind a cavity.Next, molten metal, such as aluminum, bronze, or stainless steel, is poured into the cavity through small vents. Once the metal solidifies, the ceramic shell is cracked open, revealing the finished product. The cast product is then subjected to further finishing processes like polishing, painting, or plating, resulting in a flawless end product.III. Applications of Lost Wax Casting:Lost Wax Casting has a wide array of applications, making it indispensable in numerous industries. Some notable areas where this casting process finds extensive utilization include:1. Jewelry and Fashion: Lost Wax Casting revolutionized the jewelry industry by enabling the creation of intricate and delicate designs that were previously unattainable. This process allows jewelers to cast unique pieces with precision and flawless finish.2. Art and Sculpture: Artists and sculptors embrace Lost Wax Casting for its ability to preserve the intricate details and artistic vision of their creations. This technique ensures that every detail, no matter how small, is accurately captured, giving life to stunning sculptures.3. Aerospace and Automotive: Lost Wax Casting plays a vital role in the production of critical aerospace and automotive components. The technique allows for the creation of complex and lightweight parts that enhance fuel efficiency, reduce costs, and improve overall performance.IV. Leading Company Elevating Lost Wax Casting:{}, a leading innovator in Lost Wax Casting, has taken this ancient technique to new heights. Committed to delivering exceptional services, {}, has extensively embraced cutting-edge technology and streamlined processes to offer unparalleled precision and efficiency.The company continually invests in advanced machinery, such as computer numerical control (CNC) machines, 3D printers, and scanning equipment. These technologies, combined with their expert team of skilled craftsmen, enable the creation of intricate and high-quality castings.Additionally, {} stands out for its commitment to sustainability. Through its environment-friendly practices, such as the use of recycled materials and minimizing waste, the company aims to reduce its carbon footprint while delivering exceptional products.In conclusion, Lost Wax Casting has emerged as a transformative technique that offers endless possibilities for creating intricate metal products across various industries. With {} at the forefront of technological advancements in this field, the manufacturing industry can expect further innovations and a brighter future filled with exceptional castings.