New Colorful Drawing Tablet Takes the Market by Storm
By:Admin
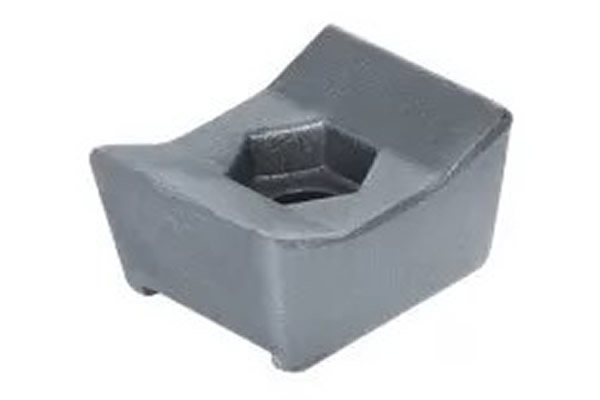
The Color Pad is a high-resolution digital drawing tablet that offers an unparalleled level of precision and sensitivity, making it the perfect tool for creating stunning works of art. Its advanced pressure sensitivity allows users to control the thickness and opacity of their lines with incredible accuracy, while its tilt recognition feature enables natural, fluid movement for a truly immersive drawing experience.
But what truly sets the Color Pad apart is its revolutionary color-matching technology, which allows users to accurately capture and replicate any color they see in the real world. This game-changing feature opens up a world of possibilities for artists and designers, enabling them to seamlessly integrate their digital creations with the physical world around them.
The Color Pad also boasts a sleek, ergonomic design that prioritizes user comfort and convenience. Its compact size and wireless capabilities make it a portable and versatile tool that can be used anywhere, from the studio to the coffee shop. Plus, with its long-lasting battery life, artists can work uninterrupted for hours on end without needing to worry about recharging.
In addition to its advanced hardware, the Color Pad also comes equipped with a user-friendly interface and a wide range of compatible software applications. Whether you’re a seasoned professional or just starting out, the Color Pad’s intuitive design and robust capabilities make it an ideal platform for creating, editing, and sharing your art with the world.
{company name} has a long-standing reputation for developing cutting-edge technology, and the Color Pad is no exception. Their commitment to innovation and quality is evident in every aspect of this revolutionary device, from its state-of-the-art hardware to its seamless integration with industry-leading software applications.
As the world becomes increasingly digital, the demand for tools that empower creativity and self-expression is greater than ever. The Color Pad is not just a drawing tablet; it’s a new way of thinking about art and design in the digital age. With its unparalleled precision, color-matching capabilities, and user-friendly design, the Color Pad is poised to become an indispensable tool for anyone who is passionate about bringing their creative visions to life.
The Color Pad is set to hit the market later this year, and the excitement surrounding its release is already palpable. Artists and designers around the world are eagerly anticipating the opportunity to get their hands on this game-changing device and explore the possibilities it offers for their creative work.
In conclusion, the Color Pad is a game-changer for the digital art and design world. With its advanced technology, innovative features, and user-friendly design, it has the potential to revolutionize the way we create and interact with digital art. As {company name} continues to push the boundaries of what is possible with technology, the Color Pad stands as a testament to their commitment to innovation and excellence in the digital arts.
Company News & Blog
Handcrafted Blacksmith Hooks: A Timeless Addition to Your Home
Blacksmith Made Hooks Combine Tradition and Quality CraftsmanshipIn an age where mass-produced goods dominate the market, it can be rare to find products that are imbued with the time-honored traditions of craftsmanship. However, one company, {}, is bucking this trend by producing a line of meticulously handcrafted blacksmith made hooks that showcase the beauty of traditional metalworking techniques.{} is a family-owned business that has been in operation for over three generations, and their dedication to preserving the art of blacksmithing is evident in every piece they create. Their team of skilled artisans are passionate about their craft and are committed to producing high-quality, durable products that will stand the test of time.The process of creating {}'s blacksmith made hooks begins with the selection of high-quality materials. The company sources the finest steel, ensuring that each hook is not only visually stunning, but also strong and resilient. Once the raw materials have been chosen, the blacksmiths at {} begin the painstaking process of shaping and forging the metal by hand.Each hook is individually crafted, with the blacksmiths using traditional tools and techniques to create intricate and unique designs. The care and attention to detail that goes into the production of these hooks is evident in the finished product, with every piece showcasing the marks of the blacksmith's hammer and the subtle imperfections that are the hallmark of handmade goods.The result is a range of blacksmith made hooks that are not only functional, but also works of art in their own right. Whether used for hanging coats, towels, or decorative items, these hooks add a touch of rustic elegance to any space. Each hook is unique, with its own character and charm, and serves as a testament to the skill and dedication of the craftsmen at {}.In addition to the beauty of their design, {}'s blacksmith made hooks are also renowned for their durability. Unlike mass-produced hooks that are often made from inferior materials and prone to breaking or bending, {}'s hooks are built to last. The strength and resilience of the steel ensures that these hooks can withstand heavy loads without warping or becoming damaged, making them a practical and long-lasting choice for any home or business.One of the most appealing aspects of {}'s blacksmith made hooks is the sense of tradition and history that they embody. In a world where so much is disposable and fleeting, these hooks are a reminder of a time when craftsmanship was highly valued, and products were made to be cherished and passed down through generations. By choosing a {} hook, customers are not only investing in a practical and beautiful item, but also in a piece of living history.As a company that is deeply committed to sustainable and ethical practices, {} is dedicated to ensuring that their blacksmith made hooks are not only of the highest quality, but also have a minimal impact on the environment. By using traditional forging methods and locally sourced materials, {} seeks to reduce their carbon footprint and support the local economy.In an era where many consumers are seeking out products that are both environmentally friendly and socially responsible, {}'s commitment to sustainability sets them apart from other manufacturers. Coupled with the timeless beauty and superior craftsmanship of their blacksmith made hooks, it is clear that {} is a company that is dedicated to producing goods that are not only functional and aesthetically pleasing, but also mindful of the world we live in.In conclusion, {}'s blacksmith made hooks are a true testament to the enduring appeal of traditional craftsmanship. With their timeless beauty, exceptional durability, and commitment to sustainability, these hooks are a perfect blend of form and function. For anyone seeking a touch of old-world charm and quality that will last a lifetime, {}'s blacksmith made hooks are an ideal choice.
Cylinder Forging: A Crucial Industrial Process for Manufacturing Strong Components
Cylinder Forging: Elevating Manufacturing Standards in the Automotive IndustryDriving the automotive industry's aspiration for excellence, Cylinder Forging, a leading player in the world of high-performance automotive components, continues to redefine manufacturing standards. With a firm commitment to innovation, quality, and customer satisfaction, the company has established itself as a prominent player in the global automotive market.Headquartered in [Location], Cylinder Forging is renowned for its exceptional expertise in the forging and production of cylinder blocks, heads, and other critical components for a wide range of automotive applications. Their advanced manufacturing processes, combined with their relentless pursuit of perfection, have earned them a distinguished reputation among automakers and enthusiasts worldwide.The company prides itself on its state-of-the-art forging facilities, equipped with top-tier machinery and cutting-edge technologies. These facilities enable Cylinder Forging to produce high-quality components that meet stringent industry standards. Their commitment to innovation also extends to their research and development department, which constantly pushes the boundaries of automotive engineering.One of Cylinder Forging's key strengths lies in its highly skilled workforce. The company boasts a team of experienced engineers, technicians, and quality control experts who work tirelessly to deliver superior products. Their collaborative approach fosters a culture of excellence and helps ensure the reliability, durability, and performance of every component that leaves their production line.Cylinder Forging's dedication to quality is further enhanced by its robust quality control processes. Each stage of the manufacturing process is executed with meticulous attention to detail, adhering to industry-leading quality standards. This commitment to excellence has resulted in numerous certifications and accolades, including ISO 9001 and ISO/TS 16949 certifications, reaffirming Cylinder Forging's unwavering commitment to delivering products of the highest quality.Recognizing that customer satisfaction is paramount, Cylinder Forging prioritizes open and transparent communication. Understanding the unique requirements of each client, the company offers customized solutions to meet their exact specifications. Their customer-centric approach has forged strong partnerships with some of the world's most renowned automakers, making Cylinder Forging a trusted supplier in the global automotive landscape.In addition to their unwavering dedication to manufacturing excellence, Cylinder Forging is committed to adopting sustainable practices throughout its operations. The company understands the environmental impact associated with the manufacturing process and actively seeks ways to minimize its carbon footprint. From energy-efficient machinery to waste reduction initiatives, Cylinder Forging demonstrates its responsibility towards environmental stewardship.Looking ahead, Cylinder Forging has its sights set on spearheading further innovation in the automotive industry. With a clear focus on emerging technologies and evolving customer demands, the company is well-positioned to cater to the needs of an ever-changing market. By fostering collaboration with industry partners, investing in research and development, and nurturing talent, Cylinder Forging aims to continuously push the boundaries of what is possible in automotive engineering.As the automotive industry evolves, Cylinder Forging remains dedicated to providing its customers with components that surpass expectations. With its commitment to innovation, quality, and sustainability, Cylinder Forging will continue to elevate manufacturing standards, inspiring the next generation of high-performance automotive components and driving excellence throughout the automotive industry.
The Benefits of Aluminum Forging in Manufacturing and Automotive Industries
Aluminum Forging is the process of shaping aluminum using extreme pressure and heat to create high-strength, lightweight components. The process is used in a variety of industries, including aerospace, automotive, and industrial manufacturing. One of the leading companies in the aluminum forging industry is {}.{} is a global leader in aluminum forging, providing high-quality components to a wide range of industries. With state-of-the-art facilities and a team of experienced engineers and technicians, {} has established itself as a trusted partner for companies seeking reliable and durable aluminum parts.The company’s expertise in aluminum forging is evident in its ability to produce complex and intricate components with tight tolerances. {} utilizes advanced forging techniques and equipment to ensure exceptional precision and consistency in every part it produces. This level of precision is critical for industries such as aerospace and automotive, where safety and reliability are paramount.In addition to its advanced forging capabilities, {} also offers a range of secondary processes to further enhance the performance and appearance of its aluminum components. These processes include heat treatment, CNC machining, and surface finishing, allowing {} to deliver fully finished parts to its customers.One of the key advantages of aluminum forging is the material’s strength-to-weight ratio. Aluminum is significantly lighter than steel, making it an ideal choice for applications where weight reduction is critical. However, despite its light weight, aluminum forged parts offer exceptional strength and durability, making them suitable for demanding operating conditions.The aerospace industry, in particular, relies on the high-performance characteristics of aluminum forged components. {} has extensive experience supplying critical parts for commercial and military aircraft, including structural components, landing gear parts, and engine components. The company’s dedication to quality and precision has earned it a reputation as a premier supplier to the aerospace industry.In the automotive sector, aluminum forging is increasingly being used to improve fuel efficiency and reduce emissions. {} works closely with automotive manufacturers to develop lightweight, high-strength components for use in engines, transmission systems, and chassis components. By utilizing aluminum forged parts, automakers can achieve significant weight savings without sacrificing performance or safety.Beyond aerospace and automotive, {} serves a wide range of industries, including defense, industrial equipment, and consumer electronics. The company’s commitment to innovation and engineering excellence has positioned it as a trusted partner for companies seeking high-quality aluminum forged components.As the demand for lightweight, high-strength components continues to grow across various industries, {} remains at the forefront of aluminum forging technology. The company’s investment in research and development, coupled with its dedication to quality and precision, ensures that it will continue to meet the evolving needs of its customers.In conclusion, {} is a leading provider of aluminum forging services, offering advanced capabilities and a commitment to excellence in every part it produces. With a strong track record of supplying critical components to the aerospace, automotive, and industrial sectors, {} is poised to continue its leadership in the aluminum forging industry.
How To Make Successful Casting Investments: A complete Guide
Investment in Casting IndustryThe global casting industry has been experiencing significant growth over the past few years, and this trend is expected to continue in the foreseeable future. One of the leading companies in this industry, {} has recently announced a substantial investment in its casting division. This investment not only marks a significant milestone for the company but also reflects the positive outlook for the casting industry as a whole.{} is a renowned company with a strong presence in the casting industry. With a reputation for delivering high-quality products and innovative solutions, the company has established itself as a key player in the global market. Its commitment to excellence and continuous improvement has set it apart from its competitors, and the recent investment in its casting division is a testament to its dedication to staying ahead of the curve.The investment in the casting division is aimed at expanding production capacity, increasing efficiency, and enhancing the overall capabilities of the company. With the demand for cast metal products on the rise, this investment comes at a crucial time and positions {} to capitalize on the growing market opportunities. By leveraging the latest technologies and implementing best practices, the company is well-positioned to meet the evolving needs of its customers and maintain its competitive edge in the industry.In addition to its focus on technological advancements, {} is also committed to sustainability and environmental responsibility. The investment in the casting division includes initiatives to reduce energy consumption, minimize waste, and lower the company's carbon footprint. By integrating sustainable practices into its operations, {} is not only contributing to a healthier planet but also meeting the expectations of environmentally conscious customers and stakeholders.Furthermore, the investment in the casting division is expected to create new job opportunities and drive economic growth in the regions where {} operates. As the company expands its production capacity and broadens its capabilities, it will need to hire skilled workers, engineers, and support staff to meet the growing demand for its products. This will not only benefit the local economies but also contribute to the development of a highly skilled workforce in the casting industry.Commenting on the investment, the CEO of {} expressed optimism about the future of the casting industry and the company's position in the market. He stated, "The investment in our casting division reflects our confidence in the growth potential of the industry and our commitment to delivering value to our customers. By expanding our capabilities and investing in sustainable practices, we are positioning {} for long-term success and leadership in the casting market."The announcement of the investment in the casting division has been well-received by industry experts, analysts, and stakeholders. Many have lauded {} for its forward-thinking approach and strategic investments, which are expected to yield positive outcomes for the company and the casting industry as a whole.Looking ahead, the investment in the casting division is poised to elevate {} to new heights of success and strengthen its position as a global leader in the casting industry. With a focus on innovation, sustainability, and customer satisfaction, {} is well-equipped to navigate the evolving market dynamics and capitalize on the opportunities that lie ahead. As the demand for cast metal products continues to rise, the investment will enable {} to meet this demand while maintaining its reputation for excellence and reliability.In conclusion, the recent investment in the casting division underscores {}'s unwavering commitment to innovation, sustainability, and growth. By expanding its production capacity, enhancing efficiency, and embracing sustainable practices, the company is poised to seize the opportunities presented by the thriving casting industry. As a result, {} is well-positioned to drive positive change, create value for its stakeholders, and maintain its leadership position in the global market.
High-Quality Hot Forging Parts for Your Industrial Needs
Hot Forging Parts, a leading manufacturing company in the field of hot forging, is known for its high-quality products and exceptional customer service. With a strong focus on innovation and technology, the company has established itself as an industry leader, delivering reliable and cost-effective solutions to its global clientele. Hot Forging Parts specializes in the manufacture of a wide range of hot forged products, including automotive parts, industrial machinery components, and aerospace components. The company has earned a reputation for its ability to produce complex and precision-engineered parts, meeting the stringent requirements of various industries. The company’s manufacturing facilities are equipped with state-of-the-art forging equipment and technology, allowing for the production of superior quality parts with tight tolerances and high mechanical properties. This enables Hot Forging Parts to meet the evolving needs of its customers and deliver products that exceed industry standards. In addition to its advanced manufacturing capabilities, Hot Forging Parts has a team of highly skilled and experienced engineers and technicians who are committed to delivering excellence in every aspect of the business. The company’s dedication to continuous improvement and investment in research and development has enabled it to stay ahead of the competition and provide cutting-edge solutions to its customers. The company’s commitment to quality and customer satisfaction is evident in its adherence to rigorous quality control measures at every stage of the manufacturing process. From the selection of raw materials to the final inspection of finished products, Hot Forging Parts ensures that each part meets the highest standards of quality and performance. Hot Forging Parts also places a strong emphasis on environmental sustainability, incorporating eco-friendly practices into its operations. The company is dedicated to minimizing its environmental impact and has implemented energy-efficient processes and waste reduction initiatives in its manufacturing facilities. With a global client base spanning across various industries, Hot Forging Parts has established strong and enduring relationships with its customers. The company prides itself on its ability to understand and adapt to the unique requirements of each customer, providing customized solutions that meet their specific needs. As the demand for hot forged parts continues to grow, Hot Forging Parts remains committed to staying at the forefront of the industry. Through its relentless pursuit of excellence and continuous innovation, the company aims to further expand its presence in the global market and strengthen its position as a trusted provider of high-quality hot forged products.In conclusion, Hot Forging Parts has solidified its reputation as a leading manufacturer of hot forged products, known for its unwavering commitment to quality, innovation, and customer satisfaction. With its advanced manufacturing capabilities, dedicated team of professionals, and strong focus on sustainability, the company is well-positioned to meet the evolving needs of its customers and drive continued growth in the industry.
Unveiling the Intricate Process of Forging: An In-Depth Look
Title: Innovations in the Process of Forging Revolutionize Manufacturing IndustryIntroduction:The process of forging, a centuries-old technique of shaping metal, has undergone a transformation thanks to groundbreaking innovations introduced by several industry leaders. In particular, companies like {} have played a pivotal role in revolutionizing the manufacturing sector through their cutting-edge technologies and techniques. This article discusses how these advancements have improved the forging process, leading to enhanced product quality, increased production efficiency, and higher customer satisfaction.Body:1. The Foundations of Forging:Forging is the process of shaping metal through the application of tremendous pressure, usually with the help of hydraulic or mechanical force. Known for its strength, durability, and reliability, forged components find applications in various industries, including automotive, aerospace, defense, and construction. Traditionally, forging was a labor-intensive process that required skilled craftsmen to manually shape the metal into the desired form. However, with the advent of modern technologies, the forging industry has witnessed significant advancements, which have simplified and optimized the manufacturing process.2. Introduction of Advanced Materials:One key innovation lies in the utilization of advanced materials for forging applications. With the development of high-strength alloys, superalloys, and composite materials, manufacturers now have access to materials with enhanced characteristics, such as superior mechanical properties, heat resistance, and corrosion resistance. By utilizing these advanced materials, companies have been able to produce components that are not only lighter and more durable but also better suited for specific operational conditions.3. Computer-Aided Design and Manufacturing (CAD/CAM) Integration:Integration of computer-aided design and manufacturing (CAD/CAM) systems has been instrumental in streamlining the entire forging process. By digitizing the design, simulation, and manufacturing phases, engineers can now create intricate component geometries with enhanced precision and accuracy. CAD/CAM integration allows for the optimization of tooling and die designs, reducing material waste and production costs while improving overall product quality.4. Automation and Robotics:The introduction of automation and robotics in forging facilities has led to a significant boost in production efficiency and consistency. Intelligent robotic systems can now handle complex tasks previously performed by human operators, such as loading and unloading parts, transferring components between workstations, and performing quality inspections. This integration of automation not only improves productivity and reduces labor costs but also ensures a higher level of precision, repeatability, and safety throughout the manufacturing process.5. Simulation and Predictive Analysis:Simulations and predictive analysis tools are transforming the way manufacturers approach the forging process. Advanced software can simulate the behavior of metals under extreme heat and pressure, accurately predicting how they will deform, crack, or fail. By simulating different scenarios, engineers can optimize the process parameters, tooling designs, and material selection, reducing the time and costs associated with physical prototyping and testing. This technological advancement allows for faster development cycles, improved component quality, and increased overall efficiency.6. Additive Manufacturing in Forging:Additive manufacturing, often referred to as 3D printing, has also found its way into the realm of forging. Through the utilization of metal powders and advanced printing techniques, complex components can be fabricated layer by layer, eliminating the need for traditional forging processes. This disruptive technology offers increased design flexibility, reduced material waste, and shorter production times, enabling manufacturers to create intricate and lightweight components that were previously unattainable.7. Quality Assurance and Traceability:In addition to process improvements, modern forging techniques have also enhanced quality assurance and traceability. Manufacturers now employ advanced inspection technologies, such as non-destructive testing and optical measurement systems, to ensure that components meet the highest industry standards. Additionally, blockchain-based systems facilitate real-time traceability, providing customers with transparent information about the origin, production, and testing of forged components. These advancements instill confidence in the quality and reliability of the products while meeting the rigorous demands of various regulatory bodies.Conclusion:The evolution of the forging process, driven by the innovative technologies introduced by companies such as {}, has ushered in a new era of manufacturing excellence. From advanced materials and CAD/CAM integration to automation, simulation, and additive manufacturing, these advancements have significantly improved product quality, production efficiency, and customer satisfaction. The future of forging appears promising, with continued research and development propelling the industry towards greater innovation and success.
High-Quality Forged Ball Valve: A Reliable Solution for Your Plumbing Needs
FORGING BALL VALVES: Ensuring Precision and Performance for Industrial ApplicationsIn today's rapidly advancing industrial landscape, companies are constantly seeking innovative solutions to bolster their operational efficiency and ensure the highest standards of performance. Among the critical components that enable smooth operations are forging ball valves, which play a vital role in controlling the flow of various fluids and gases. By combining advanced engineering techniques with cutting-edge materials, manufacturers are revolutionizing the quality and reliability of these valves, propelling industries into the future.Seeking to deliver these benefits to numerous industries, {Company Name}, a leading manufacturer of industrial valves, has introduced its state-of-the-art forging ball valves. With a reputation built on decades of engineering expertise and commitment to customer satisfaction, {Company Name} is dedicated to meeting the evolving needs of industries worldwide.Forging is a manufacturing process that involves shaping metal by applying compressive forces using hammers or presses. Compared to casting, forging enhances the mechanical properties of components, ensuring greater strength, durability, and resistance to external stress factors. By incorporating forging techniques into the production of ball valves, {Company Name} aims to provide superior performance and reliability, minimizing downtime and maximizing productivity for their customers.One of the key advantages of {Company Name}'s forging ball valves lies in their ability to withstand high-pressure environments. These valves are designed to efficiently regulate fluid and gas flow even under extreme operating conditions. This ensures uninterrupted operations for industries such as oil and gas, power generation, and petrochemicals, where pressure differentials can be substantial.Furthermore, {Company Name}'s forging ball valves offer exceptional resistance to corrosion, erosion, and wear and tear. Their robust construction and advanced material selection mitigate the risk of leakage or failure, improving the overall safety and reliability of industrial processes. By ensuring the integrity of fluid containment systems, these valves help protect employees, the environment, and valuable equipment.In addition to their superior performance, {Company Name}'s forging ball valves are engineered for ease of maintenance. The valves incorporate features that allow for quick and effortless disassembly and reassembly, which minimizes downtime during routine inspections or repairs. This results in increased operational efficiency and reduced maintenance costs for industries where uptime is critical.As a responsible industry player, {Company Name} also prioritizes environmental sustainability. The forging process employed in the manufacture of these valves reduces material waste compared to traditional casting methods, making it an environmentally friendly option. Furthermore, by prolonging the lifespan of equipment and preventing leaks or failures, {Company Name}'s forging ball valves contribute to the conservation of resources and the reduction of greenhouse gas emissions.{Company Name} continues to lead the forging ball valve industry through ongoing research and development. Its dedicated team of engineers constantly explores new materials, designs, and manufacturing techniques to enhance the performance and reliability of their valves. By closely collaborating with customers, {Company Name} ensures that its products are tailored to meet specific industry requirements and exceed expectations.In conclusion, {Company Name}'s forging ball valves offer a new standard of precision, performance, and reliability in the industrial sector. By leveraging the advantages of the forging process, these valves provide enhanced durability, resistance to high pressure and corrosion, and ease of maintenance, ultimately driving operational efficiency for a wide range of industries. As the company continues to innovate and collaborate, it remains at the forefront of forging ball valve technology, empowering industries worldwide to achieve excellence in their operations.
Top Quality Machining Parts for Your Industry Needs
Machining Parts: Meeting the Needs of Customers with Precision and QualityIn today's rapidly evolving manufacturing industry, precision and quality are crucial factors that determine the success of any product. As a leading provider of machining parts, [Company Name] has been at the forefront of meeting the diverse needs of its customers with its commitment to precision and quality. With a strong emphasis on advanced technologies and skilled workforce, [Company Name] has continued to set new benchmarks in the machining parts industry.Established in [year], [Company Name] has consistently delivered innovative and high-quality machining parts solutions to a wide range of industries, including automotive, aerospace, medical, and electronics. The company's strong focus on research and development has enabled it to stay ahead of the curve and provide cutting-edge solutions to its customers. With a state-of-the-art manufacturing facility equipped with the latest CNC machines and advanced testing equipment, [Company Name] has the capability to produce precision parts with complex geometries and tight tolerances.One of the key strengths of [Company Name] lies in its team of highly skilled engineers and technicians who possess a deep understanding of machining processes and are dedicated to delivering the highest quality products. The company takes pride in its ability to work closely with its customers to understand their unique requirements and provide tailored solutions that meet their specific needs. Whether it's a small batch of custom parts or a large-scale production run, [Company Name] has the capabilities and expertise to deliver precision parts that exceed customer expectations.[Company Name] offers a wide range of machining processes, including milling, turning, grinding, and EDM, to produce components with a high degree of accuracy and surface finish. The company's commitment to quality is evident in its rigorous quality control processes that ensure every part meets the highest standards before it is delivered to the customer. With a focus on continuous improvement and lean manufacturing principles, [Company Name] is able to optimize production processes and minimize lead times, enabling it to meet the demands of the fast-paced manufacturing industry.Furthermore, [Company Name] has invested in advanced CAD/CAM software and simulation tools that enable it to optimize part designs and manufacturing processes, leading to improved efficiency and cost-effectiveness. The company also leverages its expertise in materials science to recommend the most suitable materials for specific applications, ensuring that the final product meets the required performance and durability standards.In addition to its technical capabilities, [Company Name] places a strong emphasis on building long-term relationships with its customers. The company's customer-centric approach is reflected in its flexibility to accommodate rush orders and its willingness to go the extra mile to ensure customer satisfaction. With a focus on open communication and transparency, [Company Name] aims to be a reliable and trusted partner for its customers, offering them the support and expertise they need to bring their ideas to life.Looking ahead, [Company Name] is committed to further enhancing its capabilities and expanding its presence in the global machining parts market. The company's relentless pursuit of excellence and dedication to serving its customers with precision and quality will continue to be the driving force behind its success. As the manufacturing industry continues to evolve, [Company Name] is well-positioned to meet the evolving needs of its customers and remain a leader in the machining parts industry.In conclusion, [Company Name] is a trusted provider of precision machining parts, with a strong focus on quality, innovation, and customer satisfaction. With its advanced technologies, skilled workforce, and customer-centric approach, the company is well-equipped to meet the diverse needs of its customers and deliver solutions that exceed expectations. As [Company Name] continues to set new benchmarks in the machining parts industry, it remains committed to being a reliable and trusted partner for its customers, providing them with the precision parts they need to succeed in today's competitive marketplace.
Effective Forging Equipment: Boosting Efficiency and Precision for Industrial Operations
Title: Next-Generation Forging Equipment Revolutionizes the Manufacturing IndustryIntroduction:In today's ever-evolving manufacturing industry, companies are constantly seeking innovative tools and technologies to enhance their production processes. The latest breakthrough in forging equipment, developed by an industry-leading company, promises to revolutionize the way manufacturers produce high-quality components. Leveraging cutting-edge technologies, this next-generation forging equipment improves efficiency, reduces costs, and ensures superior product quality.Section 1: What is Forging Equipment?Forging equipment refers to machines and tools used in metalworking processes, specifically the shaping and forming of metal components through the application of heat and pressure. The process involves deforming metal using localized compressive forces to achieve the desired shape and strength in the final product. Traditionally, forging has been performed using hammers or presses, but recent advancements in technology have paved the way for more sophisticated and efficient equipment.Section 2: Company Introduction and ExpertiseWith a rich history of innovation and expertise in the manufacturing industry, the company behind this next-generation forging equipment has established itself as a global leader. Drawing on decades of experience and extensive research and development, this industry pioneer has consistently delivered groundbreaking solutions that have reshaped various industrial sectors. Combining state-of-the-art technologies with a commitment to operational excellence, the company ensures its products meet the highest standards of quality, efficiency, and safety.Section 3: The Features and Benefits of the Next-Generation Forging EquipmentThe next-generation forging equipment developed by this pioneering company introduces several new features and benefits that set it apart from traditional forging machinery.3.1 Advanced Automation:The new forging equipment leverages advanced automation technologies, including robotics, machine learning, and artificial intelligence. This automation drastically reduces the need for manual intervention, streamlining the production process and minimizing the risk of human errors. By automating repetitive tasks, manufacturers can achieve higher production volumes, improve overall efficiency, and reduce labor costs.3.2 Precision and Consistency:The cutting-edge software integrated into the forging equipment ensures precise control over temperature, pressure, and other critical parameters. This precision enhances the quality and structural integrity of the forged components, leading to consistent outcomes. Manufacturers can now confidently produce complex shapes and intricate designs, allowing for greater product versatility and customization.3.3 Energy Efficiency:The next-generation forging equipment emphasizes energy efficiency, employing innovative techniques to reduce energy consumption during the forging process. By optimizing power usage and minimizing heat loss, manufacturers can significantly reduce their environmental footprint and operational costs.3.4 Safety and Maintenance:This revolutionary forging equipment prioritizes safety by incorporating advanced safety features such as real-time monitoring, automatic fault detection, and emergency shutdown systems. Additionally, predictive maintenance algorithms continuously monitor the equipment's performance, enabling proactive maintenance planning and minimizing downtime.Section 4: Case Studies and Real-World ApplicationsSeveral leading manufacturers across various industries have already adopted this next-generation forging equipment, benefiting from its advanced capabilities.4.1 Automotive Industry:For automobile manufacturers, the new forging equipment enables the production of lightweight, high-strength components critical for improving fuel efficiency and enhancing vehicle performance. Moreover, the precision and consistency of the equipment ensure the production of complex engine parts, resulting in enhanced reliability and durability.4.2 Aerospace Sector:The aerospace industry demands uncompromising quality, reliability, and precision. The new forging equipment meets these requirements, enabling the production of critical aerospace components, including turbine blades, landing gear, and structural elements. The equipment's high precision ensures the parts meet stringent quality standards, enhancing overall aircraft safety.Section 5: Future Implications and ConclusionThe next-generation forging equipment represents a giant leap forward for the manufacturing industry. This innovative technology opens doors for manufacturers to achieve higher productivity, improved quality, and greater customization. As more companies embrace this cutting-edge forging machinery, the industry as a whole will experience enhanced competitiveness and increased market opportunities. With continuous advancements in materials science and technology, the potential for further innovation in forging equipment remains promising, allowing manufacturers to meet the demands of a rapidly changing world.
Unveiling the Troubling Reality of Counterfeit Auto Parts in the Industry
Title: Increased Concerns Raised Over the Proliferation of Counterfeit Automotive ComponentsIntroduction:In an increasingly globalized market, the automotive industry has been witnessing a concerning rise in the manufacture and distribution of forged automotive components. Manufacturers and suppliers are grappling with the threat that counterfeit products pose to consumer safety, vehicle performance, and brand reputation. This article aims to shed light on the issue of forged automotive components while highlighting the importance of using genuine and quality parts.Counterfeit Components: A Growing ThreatThe automotive industry has long been plagued by counterfeit parts, and the problem continues to worsen with the proliferation of criminal networks. These manufacturers and suppliers produce substandard automotive components, often by copying legitimate ones or by forging the logos and trademarks of reputable brands. Counterfeiters target various parts of vehicles, including engine components, suspension systems, braking systems, and electrical systems, among others.The Dangers of Counterfeit ComponentsUtilizing counterfeit automotive components can have severe ramifications on multiple levels. Firstly, with quality and safety compromised, the risk of accidents and fatalities on the road drastically increases. Poorly manufactured components can malfunction, leading to sudden failures, reduced braking efficiency, compromised steering controls, and potential engine breakdowns. In addition to jeopardizing driver and passenger safety, counterfeit parts can also cause significant damage to the vehicle itself, leading to costly repairs.Brand Reputation and Economic ConsequencesCounterfeit automotive components undermine the reputation and trust built by established automobile manufacturers and suppliers. Consumers unknowingly purchasing counterfeit components associate their poor performance or failure with the genuine brand, causing reputational damage. Furthermore, this phenomenon adversely affects the original manufacturers/brands by diluting market share and profits. The loss of revenue due to counterfeit parts ultimately hinders innovation, research, and development within the automotive industry.Identifying Genuine Automotive ComponentsTo safeguard against the use of counterfeit parts, it is crucial for consumers to be aware of the signs that distinguish genuine automotive components from counterfeit ones. Looking for incorrect branding, logos, and trademarks, poor quality packaging, misspelled words, and overall low-quality construction should raise immediate red flags. Furthermore, purchasing automotive components from authorized dealers, reputable suppliers, or directly from the original manufacturer can significantly reduce the risk of buying counterfeit parts.Industry Response and Collaborative EffortsRecognizing the severity of the issue, automobile manufacturers, suppliers, industry associations, and law enforcement agencies have been working collaboratively to combat the proliferation of counterfeit parts. These efforts include conducting raids on illegal manufacturing facilities, raising awareness among the public regarding counterfeit parts' risks, enhancing supply chain security, and promoting regulations to curb the production and distribution of forged automotive components.The Importance of Consumer EducationWhile considerable strides have been made in tackling the counterfeit automotive component market, consumer education remains vital. By understanding the dangers associated with counterfeit parts, consumers can make informed decisions that prioritize safety and quality. It is essential for drivers and vehicle owners to conduct research, seek expert advice, and only purchase genuine parts from authorized dealerships or reliable suppliers.ConclusionThe rise in counterfeit automotive components poses a significant threat to driver safety, vehicle performance, and brand reputation. Consumers must remain vigilant, educating themselves about the dangers of these forged parts and taking proactive measures to ensure the use of genuine automotive components. Through increased awareness, stringent regulations, collaborative efforts, and responsible purchasing decisions, the automotive industry can combat the proliferation of counterfeit components and ensure safer roads for everyone.